Micro cavity substrates manufacturing
Micro cavity substrates and Open a cavity or multiple cavity on the PCB or BGA substrates. we made many Cavity PCBs from 3 layer to 20 layers with High speed and high frequency materials.
Microcavity substrates serve as the foundational materials for creating microcavities, which are minute structures engineered to confine light or electromagnetic waves within a small volume. These substrates play a pivotal role in a wide array of optical and photonic devices, ranging from lasers to optical sensors. Characterized by their precise dimensions, tailored optical properties, and compatibility with semiconductor fabrication techniques, microcavity substrates enable the precise control of light-matter interactions at the nanoscale. By confining light within the microcavity, these substrates enhance the efficiency, sensitivity, and performance of optical devices. They facilitate the generation of high-quality optical resonances and enable the development of compact and efficient photonic systems. With advancements in microfabrication technologies, microcavity substrates continue to drive innovation in fields such as telecommunications, biomedical imaging, quantum optics, and beyond, paving the way for the development of next-generation optical devices with enhanced functionalities and performance.
What is a Micro Cavity Substrate?
Micro cavity substrates manufacturing. we can produce the best samllest bump pitch with 100um, the best smallest trace are 9um. and the smallest gap are 9um. most of the design are 15um to 30um trace and spacing.
A micro cavity substrate typically refers to a substrate material used in the fabrication of microcavities, which are tiny structures designed to confine light or electromagnetic waves within a small volume. These substrates are crucial components in various optical and photonic devices, such as lasers, optical filters, and sensors.
The choice of substrate material is essential as it can affect the performance and characteristics of the microcavity. Common substrate materials include semiconductors like silicon (Si) and compound semiconductors such as gallium arsenide (GaAs) or indium phosphide (InP). These materials are chosen for their optical properties, compatibility with semiconductor fabrication techniques, and ability to integrate with other components.
Micro cavity substrates are engineered with precise dimensions and properties to enable the formation of microcavities with specific optical characteristics, such as high reflectivity, low loss, and tailored resonance frequencies. These substrates may undergo various fabrication processes, including lithography, etching, and deposition, to create the desired microcavity structures.
What are the Micro Cavity Substrate Design Guidelines?
Microcavity substrate design guidelines vary depending on the specific application and desired optical properties. However, some general principles and considerations for designing microcavity substrates include:
- Material Selection: Choose a substrate material with suitable optical properties for the intended application. Common materials include silicon (Si), gallium arsenide (GaAs), indium phosphide (InP), and other semiconductor materials.
- Optical Properties: Consider the refractive index and absorption characteristics of the substrate material, as they can affect the performance of the microcavity. Substrates with low absorption and high refractive index contrast with surrounding media are often preferred for efficient light confinement.
- Dimensional Control: Precisely control the dimensions of the substrate, including thickness and lateral dimensions, to achieve the desired optical resonance conditions within the microcavity.
- Surface Quality: Ensure the substrate surface is smooth and free from defects that could scatter or absorb light, as these imperfections can degrade the performance of the microcavity.
- Reflectivity Enhancement: Implement techniques to enhance the reflectivity of the cavity mirrors, such as using dielectric coatings or distributed Bragg reflectors, to improve the cavity quality factor (Q-factor) and resonance efficiency.
- Integration Compatibility: Design the substrate to be compatible with integration processes for other components or fabrication steps in the device manufacturing process, such as lithography, etching, and deposition.
- Thermal Management: Consider thermal properties of the substrate material and implement measures to dissipate heat efficiently, especially for high-power applications, to avoid thermal degradation of the device.
- Fabrication Techniques: Choose appropriate fabrication techniques tailored to the selected substrate material and desired microcavity structure, ensuring precision and reproducibility in manufacturing.
- Simulation and Optimization: Use computational tools and simulation techniques to model and optimize the microcavity design, considering factors such as mode confinement, resonance frequency, and quality factor.
- Application-Specific Requirements: Tailor the design to meet specific application requirements, such as wavelength range, spectral bandwidth, and sensitivity, ensuring optimal performance in the intended use case.
By carefully considering these guidelines and optimizing the design parameters, designers can create microcavity substrates that meet the performance specifications and requirements of their intended applications.
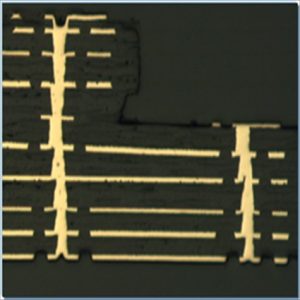
Micro cavity substrates
What is the Micro Cavity Substrate Fabrication Process?
The fabrication process for microcavity substrates involves several steps, including material preparation, patterning, etching, deposition, and characterization. Below is a general overview of the typical fabrication process:
- Material Selection: Choose a substrate material suitable for the intended application, considering factors such as optical properties, compatibility with fabrication techniques, and thermal properties.
- Cleaning and Preparation: Clean the substrate surface thoroughly to remove any contaminants or residues that could affect subsequent processing steps. Surface treatment methods such as chemical cleaning or plasma cleaning may be employed.
- Patterning: Use lithography techniques to define the desired microcavity structure on the substrate surface. This typically involves applying a photoresist layer, exposing it to UV light through a mask with the desired pattern, and developing to transfer the pattern onto the substrate.
- Etching: Etch the substrate to create the cavity structure defined by the pattern. Various etching techniques may be employed depending on the substrate material and desired cavity geometry, including wet chemical etching, dry etching (such as reactive ion etching), or a combination of both.
- Deposition: Deposit additional materials onto the substrate surface to create mirrors or other components within the microcavity. This may involve techniques such as physical vapor deposition (PVD), chemical vapor deposition (CVD), or atomic layer deposition (ALD) to deposit thin films of metals, dielectrics, or semiconductors.
- Mirror Coating: Apply reflective coatings to the cavity mirrors to enhance optical reflectivity and improve cavity performance. Dielectric coatings or distributed Bragg reflectors (DBRs) are commonly used for this purpose.
- Characterization and Testing: Characterize the fabricated microcavity substrates to evaluate their optical properties, dimensional accuracy, and performance metrics such as resonance frequency and quality factor. Techniques such as optical microscopy, scanning electron microscopy (SEM), and optical spectroscopy may be employed for characterization.
- Optimization and Refinement: Iteratively optimize the fabrication process based on characterization results and feedback, refining parameters such as etching conditions, deposition thicknesses, and surface treatments to improve substrate performance and reproducibility.
- Integration: Integrate the fabricated microcavity substrates with other components or devices as necessary for the intended application, such as bonding them to semiconductor chips, optical fibers, or supporting structures.
- Packaging and Protection: Package the completed devices to protect them from environmental factors such as moisture and contamination, ensuring long-term stability and reliability in operation.
Throughout the fabrication process, careful attention to process control, material compatibility, and quality assurance is essential to ensure the reproducibility and reliability of the fabricated microcavity substrates.
How do you manufacture a Micro Cavity Substrate?
Manufacturing a microcavity substrate involves several intricate steps that require precision and expertise in microfabrication techniques. Here’s a detailed overview of the typical manufacturing process:
- Substrate Selection: Choose a substrate material suitable for the intended application, considering factors such as optical properties, thermal conductivity, and compatibility with fabrication processes. Common substrate materials include silicon (Si), gallium arsenide (GaAs), indium phosphide (InP), and various other semiconductors or dielectric materials.
- Cleaning and Preparation: Clean the substrate surface thoroughly to remove contaminants and ensure good adhesion for subsequent processing steps. This typically involves cleaning with solvents, followed by rinsing and drying.
- Photolithography: Use photolithography to define the desired microcavity structures on the substrate surface. This process involves coating the substrate with a photoresist, exposing it to UV light through a photomask with the desired pattern, and developing the resist to transfer the pattern onto the substrate.
- Etching: Etch the substrate to create the cavity structures defined by the photolithography pattern. Etching techniques may include wet chemical etching, dry etching (e.g., reactive ion etching), or a combination of both. The etching process selectively removes material from the substrate, leaving behind the desired cavity structures.
- Dielectric Mirror Deposition: Deposit dielectric mirror coatings on the cavity walls to enhance optical reflectivity. This can be achieved through techniques such as physical vapor deposition (PVD) or chemical vapor deposition (CVD), where alternating layers of high and low refractive index materials are deposited to create a highly reflective mirror.
- Characterization and Testing: Characterize the fabricated substrates to evaluate their dimensional accuracy, optical properties, and performance metrics such as resonance frequency and quality factor. Techniques such as scanning electron microscopy (SEM), optical microscopy, and spectroscopy may be used for characterization.
- Integration: Integrate the fabricated microcavity substrates with other components or devices as needed for the intended application. This may involve bonding the substrates to semiconductor chips, optical fibers, or supporting structures using techniques such as wafer bonding or adhesive bonding.
- Packaging and Protection: Package the completed devices to protect them from environmental factors such as moisture, dust, and mechanical damage. This typically involves encapsulating the devices in protective materials or packaging them in sealed containers.
Throughout the manufacturing process, stringent quality control measures should be implemented to ensure consistency and reliability in the fabricated microcavity substrates. Additionally, continuous process optimization and refinement may be necessary to improve yield and performance characteristics.
How much should a Micro Cavity Substrate cost?
The cost of a microcavity substrate can vary widely depending on several factors, including the substrate material, fabrication complexity, dimensions, surface quality, and required optical performance. Here are some factors that can influence the cost:
- Substrate Material: Different materials have different costs. For example, silicon substrates are generally less expensive compared to compound semiconductors like gallium arsenide (GaAs) or indium phosphide (InP).
- Fabrication Complexity: The complexity of the fabrication process, including the number of steps involved, the precision required, and the use of specialized equipment, can impact the cost. More intricate designs and tighter tolerances typically result in higher manufacturing costs.
- Dimension and Size: Larger substrates or substrates with larger surface areas may require more material and processing time, leading to higher costs.
- Surface Quality: Substrates with higher surface quality, such as smoother surfaces and fewer defects, may require additional processing steps or higher-quality materials, which can increase the cost.
- Optical Performance: Substrates designed for specific optical performance requirements, such as high reflectivity or low optical loss, may involve additional fabrication steps or specialized materials, contributing to higher costs.
- Volume and Scale: The economies of scale can significantly impact the cost per unit. Larger production volumes often result in lower per-unit costs due to efficiencies in manufacturing processes and bulk material purchasing.
- Customization: Customized or highly specialized microcavity substrates may incur additional engineering and setup costs, particularly if they require unique designs, materials, or fabrication processes.
- Supplier and Location: The cost may vary depending on the supplier, their capabilities, and their location. Suppliers with advanced fabrication facilities and expertise may charge higher prices for their services.
Given these factors, it’s challenging to provide a specific cost without detailed information about the microcavity substrate’s specifications and requirements. Typically, microcavity substrate costs can range from a few hundred to several thousand dollars per substrate, with prices potentially higher for custom or specialized substrates. Large-scale production runs and standard substrate designs may result in lower costs per unit.
What is a Micro Cavity Substrate Base Material?
The base material of a microcavity substrate refers to the foundational material from which the substrate is constructed. This material forms the structural support for the microcavity and provides the platform on which other components, such as mirrors and waveguides, may be fabricated. The choice of base material is critical as it can influence the optical properties, mechanical stability, and compatibility with fabrication processes of the microcavity substrate.
Common base materials for microcavity substrates include:
- Silicon (Si): Silicon is widely used in microelectronics and photonics due to its excellent mechanical properties, compatibility with semiconductor fabrication techniques, and transparency in the near-infrared region. Silicon substrates are suitable for various microcavity applications, including silicon-on-insulator (SOI) platforms and silicon photonic devices.
- Gallium Arsenide (GaAs): Gallium arsenide is a compound semiconductor material with high electron mobility and a direct bandgap, making it suitable for optoelectronic devices such as lasers and detectors. GaAs substrates are commonly used in microcavity applications requiring high-performance optical and electronic properties.
- Indium Phosphide (InP): Indium phosphide is another compound semiconductor material with desirable optical and electronic properties, including a direct bandgap and high electron mobility. InP substrates are commonly used in microcavity devices such as lasers, modulators, and photodetectors operating in the telecommunications wavelength range.
- Other Semiconductor Materials: Besides silicon, gallium arsenide, and indium phosphide, other semiconductor materials such as III-V compound semiconductors (e.g., AlGaAs, InGaAs) and II-VI compound semiconductors (e.g., ZnSe) may also serve as base materials for microcavity substrates, depending on specific application requirements.
- Dielectric Materials: Dielectric materials such as fused silica (quartz), sapphire, and various glasses are sometimes used as base materials for microcavity substrates, particularly in applications requiring high optical transparency and low optical loss.
The selection of the base material depends on factors such as desired optical properties, compatibility with fabrication processes, thermal stability, and cost considerations. Each material has its advantages and limitations, and the choice often depends on the specific requirements of the microcavity device or application.
Which company produces Micro Cavity Substrates?
Currently, many companies produce microcavity substrates, including Thorlabs in the United States, Sumitomo Electric in Japan, Schott in Germany, and the Chinese Academy of Sciences in China. These companies utilize advanced micro-nano processing technology and material preparation processes to produce various types of microcavity substrates to meet the needs of different application fields.
As for our company, we are also a company specializing in micro-nano processing and optoelectronic device manufacturing. We have advanced manufacturing equipment and a skilled technical team capable of designing, processing, and producing various types of microcavity substrates. Our advantages include:
- Customized Production Capability: We can customize microcavity substrates according to the specific requirements of customers, including material selection, size design, surface treatment, and other customization aspects.
- Advanced Processing Technology: We employ the most advanced micro-nano processing technology, including photolithography, etching, thin film deposition, and other processes, to ensure high precision and excellent optical performance of microcavity substrates.
- Quality Control and Assurance: We strictly control the quality during the production process, using advanced inspection equipment and technology to ensure that each microcavity substrate meets the requirements and standards of customers.
- Quick Response and Flexible Production: We have flexible production capabilities and rapid response times, enabling us to meet customer order requirements promptly and provide personalized technical support and services.
In summary, as a professional microcavity substrate manufacturing company, we have the technical expertise and capabilities required for the design, processing, and production of microcavity substrates. We are committed to providing customers with high-quality, customized products, and services.
What are the 7 qualities of good customer service?
Good customer service is essential for building strong customer relationships and fostering loyalty. Here are seven qualities that characterize excellent customer service:
- Responsiveness: A key aspect of good customer service is being responsive to customer inquiries, concerns, and requests in a timely manner. Whether it’s answering phone calls promptly, replying to emails swiftly, or addressing customer issues efficiently, responsiveness shows that you value your customers’ time and are committed to meeting their needs.
- Empathy: Empathy involves understanding and acknowledging the emotions and perspectives of customers. It means listening actively to their concerns, showing compassion for their experiences, and demonstrating genuine concern for their well-being. Empathetic customer service can help build trust and rapport with customers, even in challenging situations.
- Clear Communication: Effective communication is crucial for delivering excellent customer service. This includes conveying information clearly and concisely, using language that is easy for customers to understand, and providing accurate and relevant details. Clear communication helps prevent misunderstandings and ensures that customers have the information they need to make informed decisions.
- Problem-solving Skills: Good customer service representatives possess strong problem-solving skills to address customer issues and resolve problems effectively. This may involve identifying the root cause of the problem, proposing viable solutions, and taking proactive steps to ensure customer satisfaction. The ability to think critically and creatively when faced with challenges is essential for delivering exceptional service.
- Professionalism: Professionalism encompasses various aspects of behavior, including courtesy, respect, and integrity. Good customer service representatives maintain a professional demeanor at all times, regardless of the situation, and strive to uphold ethical standards and company policies. Professionalism helps build credibility and trust with customers and enhances the overall customer experience.
- Product Knowledge: Having a deep understanding of the products or services offered allows customer service representatives to provide accurate information, address customer inquiries, and offer relevant recommendations or solutions. A comprehensive knowledge base enables representatives to assist customers more effectively and instills confidence in their expertise.
- Follow-up and Follow-through: Following up with customers after their initial interaction and ensuring that their needs have been met demonstrates a commitment to customer satisfaction. Good customer service involves following through on promises, commitments, or resolutions made during interactions, and taking proactive steps to ensure that customers are satisfied with the outcome. Following up also provides an opportunity to gather feedback and identify areas for improvement.
By embodying these qualities, businesses can deliver outstanding customer service experiences that leave a positive impression on customers and contribute to long-term success.
FAQs (Frequently Asked Questions)
What is a microcavity substrate?
A microcavity substrate is a foundational material used in the fabrication of microcavities, which are tiny structures designed to confine light or electromagnetic waves within a small volume. These substrates play a crucial role in various optical and photonic devices, such as lasers, optical filters, and sensors.
What materials are commonly used for microcavity substrates?
Common materials for microcavity substrates include silicon (Si), gallium arsenide (GaAs), indium phosphide (InP), and various other semiconductor or dielectric materials. The choice of material depends on factors such as optical properties, compatibility with fabrication techniques, and application requirements.
What are the key characteristics of a good microcavity substrate?
Important characteristics of microcavity substrates include high optical transparency, low optical loss, precise dimensional control, smooth surface quality, and compatibility with integration processes. These characteristics ensure optimal performance and reliability in microcavity devices.
How are microcavity substrates fabricated?
The fabrication process for microcavity substrates typically involves steps such as material preparation, patterning, etching, deposition, mirror coating, and characterization. Advanced microfabrication techniques, including photolithography, etching, and thin-film deposition, are used to create the desired microcavity structures with high precision.
What are the applications of microcavity substrates?
Microcavity substrates find applications in various fields, including telecommunications, optical sensing, biomedical imaging, and quantum optics. They are used in devices such as lasers, photonic integrated circuits, resonators, and optical filters, where precise control of light-matter interactions is required.
How do microcavity substrates enhance device performance?
Microcavity substrates enable the creation of optical cavities with tailored resonance frequencies, high-quality factors (Q-factors), and efficient light-matter interactions. These properties enhance the performance of devices by improving optical confinement, increasing sensitivity, and reducing optical losses.
What factors should be considered when selecting a microcavity substrate?
When selecting a microcavity substrate, factors to consider include optical properties, material compatibility, fabrication complexity, dimensional requirements, thermal management capabilities, and cost considerations. It’s essential to choose a substrate that meets the specific needs of the intended application.
Where can I purchase microcavity substrates?
Microcavity substrates can be purchased from various suppliers, including semiconductor manufacturers, optical component suppliers, and research institutions. Online platforms and specialized distributors may also offer microcavity substrates for sale.