Military circuit board Manufacturer
Military circuit board Manufacturer. the Package Substrate will be made with Showa Denko and Ajinomoto High speed materials.or other types high speed materials and high frequency materials.
Military circuit boards are specialized electronic components designed and manufactured to meet the rigorous demands of military applications. These circuit boards are engineered with the highest standards of reliability, durability, and performance to ensure optimal operation in harsh and challenging environments. Built to withstand extreme temperatures, humidity, shock, vibration, and electromagnetic interference, military circuit boards play a crucial role in defense electronics, including communication systems, radar systems, avionics, and weapon systems. They incorporate advanced technologies, high-quality materials, and stringent manufacturing processes to deliver exceptional performance and longevity under demanding conditions. Military circuit boards adhere to strict military standards and specifications, such as MIL-PRF-31032 and MIL-STD-810, and undergo extensive testing to ensure compliance and reliability. With their robust construction and advanced features, military circuit boards play a critical role in supporting the mission-critical operations of military forces worldwide.
What is a Military Circuit Board?
A military circuit board is a type of printed circuit board (PCB) specifically designed to meet the stringent requirements of military applications. These circuit boards are used in various military equipment including communication devices, radar systems, avionics, control systems, and other defense electronics. Military circuit boards are engineered to perform reliably under extreme conditions and to ensure durability, longevity, and functionality in harsh environments. Here are some key features and aspects of military circuit boards:
- Robustness and Durability: Military circuit boards are built to withstand harsh conditions such as high and low temperatures, humidity, mechanical shocks, and vibrations. The materials used are typically of higher quality to enhance durability and performance stability.
- High Reliability: These boards are manufactured to meet strict standards for reliability, as failures can have critical implications. They are often designed with redundant pathways and other fail-safe features to ensure continuous operation even if part of the circuit fails.
- Compliance with Military Standards: Military PCBs must comply with specific military standards and specifications, such as MIL-PRF-31032 or MIL-STD-810. These standards cover various aspects including design, manufacturing processes, testing, and quality control.
- Advanced Technologies: To cater to the complex and evolving needs of military technology, these circuit boards can incorporate advanced technologies such as high-density interconnects (HDI), rigid-flex PCBs, and materials with high thermal conductivity for better heat dissipation.
- Secure and Confidential: Given the sensitive nature of many military applications, the design and manufacturing of these PCBs often involve strict controls to protect against espionage and tampering.
- Customization: Military circuit boards can be highly customized to fit specific applications and devices, often integrating unique layouts, components, and connectors to meet specialized requirements.
These specialized characteristics generally make military circuit boards more expensive compared to standard PCBs used in commercial applications. The design and production involve careful consideration and rigorous testing to ensure they can reliably function in critical and life-threatening situations.
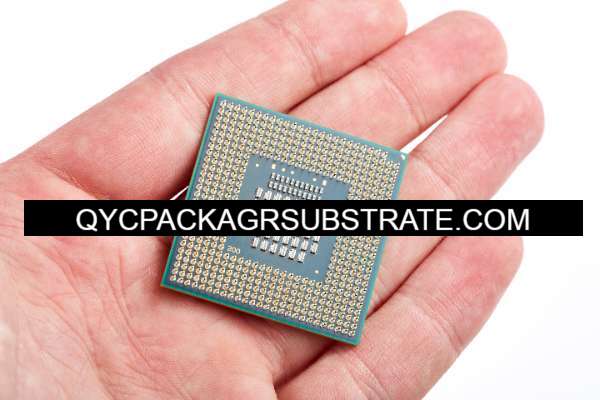
Military circuit board Manufacturer
What are the Military Circuit Board Design Guidelines?
Military circuit board design guidelines outline specific requirements and best practices for designing circuit boards intended for military applications. While the exact guidelines can vary depending on the specific military standards and specifications applicable to a project, here are some common design considerations:
- Compliance with Military Standards: Ensure that the design adheres to relevant military standards such as MIL-PRF-31032, MIL-STD-810, MIL-PRF-55110, or others as specified. These standards cover various aspects including design rules, materials, manufacturing processes, testing procedures, and quality control measures.
- Environmental Considerations: Design the circuit board to operate reliably under extreme environmental conditions such as temperature variations, humidity, shock, vibration, salt spray, and electromagnetic interference (EMI). Consider using conformal coatings and ruggedized components to enhance environmental resistance.
- Component Selection: Choose components that meet military-grade specifications for reliability, performance, and environmental robustness. Ensure that components are rated for the required temperature range, shock and vibration resistance, and have long-term availability to support maintenance and upgrades.
- Layout and Routing: Follow good PCB layout practices to minimize signal degradation, electromagnetic interference, and crosstalk. Place critical components strategically to optimize signal integrity and thermal management. Use controlled impedance traces for high-speed signal paths and minimize trace lengths for sensitive signals.
- Power Distribution: Design a robust power distribution network to ensure stable and reliable power delivery to all components, especially in systems with high-power requirements or varying loads. Implement proper decoupling and filtering techniques to minimize noise and voltage fluctuations.
- Signal Integrity: Pay attention to signal integrity considerations such as impedance matching, signal termination, and signal routing to minimize reflections, ringing, and jitter. Perform signal integrity analysis and simulation to validate the design and optimize performance.
- EMI/EMC Compliance: Design the circuit board to mitigate electromagnetic interference (EMI) and ensure compliance with electromagnetic compatibility (EMC) requirements. Use shielding, ground planes, and proper routing techniques to minimize EMI emissions and susceptibility.
- Testing and Validation: Plan for thorough testing and validation of the circuit board design to verify functionality, reliability, and compliance with military standards. Perform environmental testing, reliability testing, and functional testing under simulated operating conditions to identify and address any issues.
- Security and Tamper Resistance: Incorporate security features and tamper-resistant measures to protect against unauthorized access, reverse engineering, and tampering. Implement secure boot mechanisms, encryption, and physical security features as required by the specific military application.
- Documentation and Traceability: Maintain comprehensive documentation of the circuit board design, including schematics, layout files, bill of materials (BOM), and manufacturing specifications. Ensure traceability of components and manufacturing processes to support quality assurance and future maintenance.
By following these design guidelines, engineers can develop military circuit boards that meet the stringent requirements for reliability, performance, and durability in critical defense applications.
What is the Military Circuit Board Fabrication Process?
The fabrication process for military circuit boards involves several steps to manufacture printed circuit boards (PCBs) that meet the stringent requirements of military standards and specifications. Here’s an overview of the typical fabrication process:
- Design Preparation: The process begins with the preparation of the PCB design files using electronic design automation (EDA) software. Engineers create the circuit schematic, define the layout, and specify design rules according to military standards and project requirements.
- Material Selection:Select high-quality materials that comply with military standards and specifications. This includes choosing the appropriate substrate material (e.g., FR-4, polyimide) and copper thickness to meet the required performance and environmental requirements.
- Manufacturing Documentation: Generate manufacturing documentation including Gerber files, drill files, and fabrication drawings that specify the PCB dimensions, layer stackup, hole sizes, and other critical details for fabrication.
- Preparation of Substrate: The substrate material is prepared by cutting it to the required size and cleaning it to remove any contaminants. Surface treatment processes may be applied to enhance adhesion and promote solderability.
- Layer Stackup: Based on the PCB design, multiple layers of substrate material are stacked together, and copper foil is bonded to the substrate layers using heat and pressure. The layer stackup configuration is carefully designed to accommodate signal routing, power distribution, and impedance control requirements.
- Circuit Patterning: The circuit patterns are transferred onto the copper foil using a process called photolithography. A photoresist material is applied to the copper surface, exposed to ultraviolet light through a mask, and then developed to create the desired copper traces and pads.
- Etching: The exposed copper areas not protected by the photoresist are etched away using chemical etchants, leaving behind the desired copper traces and patterns on the substrate.
- Drilling: Precision holes are drilled into the PCB substrate to create vias and component mounting holes. Advanced techniques such as laser drilling may be used for high-density interconnect (HDI) boards.
- Plating:Conductive metal plating is applied to the drilled holes to create electrical connections between different layers of the PCB. This process, known as through-hole plating or vias filling, enhances electrical conductivity and reliability.
- Surface Finishing: The exposed copper surfaces are coated with a surface finish to protect against oxidation, promote solderability, and enhance durability. Common surface finishes for military PCBs include electroless nickel immersion gold (ENIG), immersion silver, and organic solderability preservatives (OSP).
- Final Inspection and Testing: The fabricated PCBs undergo thorough inspection and testing to ensure they meet the required specifications and quality standards. This may include visual inspection, electrical testing, dimensional measurements, and adherence to military standards.
- Documentation and Traceability: Comprehensive documentation is generated to record the fabrication process details, material certifications, and quality control records. Traceability of materials and manufacturing processes is maintained to support quality assurance and compliance requirements.
By following these steps and adhering to military standards and specifications, manufacturers can produce high-quality circuit boards suitable for use in critical military applications.
How do you manufacture a Military Circuit Board?
Manufacturing a military circuit board involves a series of intricate steps to ensure that the final product meets the rigorous standards and specifications required for military applications. Here’s an overview of the manufacturing process:
- Design and Specification Review: Before manufacturing begins, the PCB design and specifications are thoroughly reviewed to ensure compliance with military standards and project requirements. Any necessary adjustments or optimizations are made at this stage.
- Material Procurement: High-quality materials that meet military standards are sourced, including the substrate material (e.g., FR-4, polyimide), copper foil, solder mask, surface finish chemicals, and other components required for the PCB assembly.
- Preparation of Manufacturing Documentation: Detailed manufacturing documentation is prepared based on the PCB design files, including Gerber files, drill files, assembly drawings, bill of materials (BOM), and work instructions. This documentation guides the fabrication process and ensures consistency and accuracy.
- Substrate Preparation: The substrate material is prepared by cutting it to the required size and shape. Surface treatment processes may be applied to clean and condition the substrate surface for subsequent processing steps.
- Layer Stackup: Multiple layers of substrate material are stacked together according to the PCB design requirements. Copper foil is bonded to the substrate layers using heat and pressure to create the conductive layers of the PCB.
- Circuit Patterning: The circuit patterns are transferred onto the copper layers using photolithography. A layer of photoresist material is applied to the copper surface, exposed to UV light through a mask, and then developed to define the desired copper traces and pads.
- Etching:Chemical etchants are used to selectively remove the exposed copper areas not protected by the photoresist, leaving behind the desired circuit patterns on the copper layers.
- Drilling: Precision holes are drilled into the PCB substrate to create vias and component mounting holes. Advanced drilling techniques such as laser drilling may be used for high-density interconnect (HDI) boards.
- Plating: Conductive metal plating is applied to the drilled holes to create electrical connections between different layers of the PCB. This process, known as through-hole plating or vias filling, enhances electrical conductivity and reliability.
- Surface Finishing: The exposed copper surfaces are coated with a surface finish to protect against oxidation, promote solderability, and enhance durability. Common surface finishes for military PCBs include electroless nickel immersion gold (ENIG), immersion silver, and organic solderability preservatives (OSP).
- Solder Mask Application: A layer of solder mask is applied to the PCB surface, leaving only the desired areas exposed for soldering components. The solder mask protects the copper traces from oxidation and contamination while providing insulation between conductive elements.
- Silkscreen Printing: Identifying information such as component labels, reference designators, and polarity markings are applied to the PCB surface using silkscreen printing for assembly guidance.
- Component Placement: Surface-mount and through-hole components are placed onto the PCB according to the assembly instructions and the component placement plan specified in the design files.
- Soldering: The components are soldered onto the PCB using soldering techniques such as reflow soldering, wave soldering, or selective soldering, depending on the component type and assembly requirements.
- Inspection and Testing: The assembled PCBs undergo thorough inspection and testing to verify functionality, quality, and compliance with military standards. This includes visual inspection, automated optical inspection (AOI), electrical testing, and functional testing under simulated operating conditions.
- Quality Assurance and Documentation: Comprehensive documentation is generated to record the manufacturing process details, inspection results, test data, and compliance certifications. This documentation provides traceability and supports quality assurance throughout the PCB manufacturing process.
By following these manufacturing steps and adhering to military standards and specifications, manufacturers can produce high-quality circuit boards suitable for use in critical military applications.
How much should a Military Circuit Board cost?
The cost of a military circuit board can vary widely depending on several factors such as:
- Complexity: The complexity of the circuit board design influences the manufacturing cost. More complex designs with dense component placement, high layer counts, and advanced technologies (such as HDI or rigid-flex PCBs) will typically incur higher costs.
- Materials: Military-grade materials and components often come at a premium compared to standard materials. High-quality substrates, copper foils, surface finishes, and conformal coatings are typically more expensive but are necessary to meet the stringent requirements of military standards.
- Manufacturing Processes: Certain manufacturing processes, such as laser drilling, impedance control, and tight tolerances, may add to the overall cost of manufacturing. Additionally, compliance with military standards often requires additional testing, inspection, and quality control measures, which can increase costs.
- Volume:The volume of PCBs being manufactured also affects the cost per unit. Higher volume orders usually benefit from economies of scale, resulting in lower unit costs. Conversely, low-volume or prototype orders may have higher unit costs due to setup fees and lower production efficiency.
- Testing and Certification: Military circuit boards often require extensive testing and certification to ensure compliance with military standards. The cost of these testing procedures, as well as obtaining certifications, can contribute to the overall cost of the PCB.
- Supplier and Location: The choice of PCB manufacturer and their location can impact costs. Manufacturers with specialized expertise in military-grade PCBs may charge higher prices, while offshore manufacturing may offer lower labor costs but potentially longer lead times and quality control concerns.
Given these factors, it’s challenging to provide a specific cost estimate without knowing the details of the project, including the PCB specifications, quantity, and manufacturing requirements. However, military circuit boards are generally more expensive compared to standard commercial PCBs due to the additional requirements for reliability, durability, and performance under harsh conditions.
For a rough estimate, the cost of a military-grade PCB can range from several hundred to several thousand dollars per unit, depending on the factors mentioned above. It’s recommended to consult with PCB manufacturers and suppliers to obtain accurate cost estimates based on the specific project requirements.
What is the Military Circuit Board base material?
The base material for military circuit boards, like most standard PCBs, typically consists of a substrate material that provides mechanical support and electrical insulation for the circuitry. The choice of base material depends on factors such as the application requirements, environmental conditions, and performance specifications. Some common base materials used for military circuit boards include:
- FR-4 (Flame Retardant 4): FR-4 is a widely used substrate material composed of woven fiberglass cloth impregnated with epoxy resin. It offers good mechanical strength, thermal stability, and electrical insulation properties. FR-4 is suitable for a wide range of military applications and is available in various grades to meet specific performance requirements.
- Polyimide: Polyimide is a high-performance polymer material known for its excellent thermal stability, chemical resistance, and mechanical properties. Polyimide-based circuit boards, often referred to as “flexible PCBs” or “flex circuits,” are used in military applications where flexibility, lightweight, and resistance to harsh environments are critical.
- Rogers Corporation Materials: Rogers Corporation manufactures specialty high-frequency laminates tailored for demanding RF/microwave applications in military systems. These materials offer low dielectric loss, high thermal conductivity, and exceptional electrical performance at high frequencies.
- Aluminum or Copper Metal Core: For military applications requiring high thermal conductivity and heat dissipation, metal-core PCBs (MCPCBs) may be used. These PCBs feature a metal core (usually aluminum or copper) that provides superior thermal management capabilities, making them suitable for power electronics and high-power RF applications.
- Ceramic: Ceramic-based PCBs offer excellent thermal stability, mechanical strength, and high-frequency performance. They are used in military radar systems, RF/microwave circuits, and other high-performance applications where stringent electrical and thermal requirements must be met.
- Specialized Composites: In some cases, specialized composite materials may be used for military circuit boards to meet specific requirements such as lightweight, high strength, or resistance to extreme temperatures and harsh chemicals.
The choice of base material depends on various factors such as the operating environment (temperature, humidity, vibration), frequency of operation, power requirements, and specific performance criteria mandated by military standards and specifications (e.g., MIL-PRF-31032, MIL-PRF-55110). Military-grade circuit boards often use materials with enhanced reliability, durability, and performance characteristics to ensure operation in demanding military applications.
Which company makes Military Circuit Boards?
Many companies specialize in manufacturing military circuit boards, including well-known North American companies such as Sanmina, Northrop Grumman, and Lockheed Martin, as well as international companies like Thales and BAE Systems in Europe. These companies have extensive experience and expertise in designing, manufacturing, and testing circuit boards that meet military standards and specifications.
Our company also manufactures military circuit boards. We have advanced manufacturing equipment and technology, and we work closely with the military industry supply chain to ensure that our products meet stringent military standards and specifications. Our manufacturing process strictly follows international standards, and our team has extensive experience and expertise to meet the needs of various military applications.
We are committed to providing high-quality, reliable, and performance-stable military circuit boards. Our products undergo rigorous quality control and testing processes to ensure their reliability and durability in harsh environments. Our engineering team can customize designs according to customer requirements, and our manufacturing capabilities can meet various scale and production requirements.
Through our company, customers can benefit from the following advantages:
- Expertise and Experience: We have extensive experience and expertise in designing and manufacturing circuit boards that comply with military standards.
- High Quality and Reliability: We employ advanced manufacturing technology and strict quality control processes to ensure product quality and reliability.
- Customization Capability: We can customize designs and manufacture circuit boards according to customer-specific requirements to meet their specific application needs.
- Flexibility and Responsiveness: We can quickly respond to customer needs and provide flexible manufacturing solutions to meet different scale and time requirements.
In summary, our company has the expertise, technology, and resources required to manufacture military circuit boards, providing customers with high-quality, reliable, and customized solutions.
What are the qualities of good customer service?
Good customer service is characterized by several key qualities that aim to meet and exceed customer expectations while building positive relationships and loyalty. Here are some qualities of good customer service:
- Responsiveness: Good customer service involves being prompt and responsive to customer inquiries, requests, and concerns. This includes timely responses to emails, phone calls, and messages, as well as addressing customer needs promptly.
- Empathy: Empathy is essential in understanding and acknowledging the customer’s feelings, concerns, and perspectives. Customer service representatives should listen actively, show genuine concern, and demonstrate empathy towards the customer’s situation.
- Clear Communication: Effective communication is crucial for providing good customer service. Customer service representatives should communicate clearly and concisely, using language that is easy to understand and free from jargon. They should also ensure that the customer understands the information provided and any steps or solutions offered.
- Knowledge and Expertise: Good customer service requires a deep understanding of the product or service being offered. Customer service representatives should be knowledgeable about the company’s offerings, policies, procedures, and frequently asked questions. They should also possess the expertise to troubleshoot problems and provide accurate information and solutions to customers.
- Professionalism: Professionalism involves maintaining a courteous, respectful, and professional demeanor at all times when interacting with customers. This includes being polite, patient, and courteous, even in challenging or stressful situations. Customer service representatives should also maintain confidentiality and adhere to ethical standards.
- Problem-Solving Skills: Good customer service involves effectively resolving customer issues and complaints in a timely and satisfactory manner. Customer service representatives should be proactive in identifying and addressing customer problems, offering viable solutions, and following up to ensure customer satisfaction.
- Flexibility and Adaptability: Customers’ needs and preferences may vary, so good customer service requires flexibility and adaptability. Customer service representatives should be able to tailor their approach and solutions to meet the unique needs of each customer and situation.
- Consistency:Consistency is key to building trust and credibility with customers. Good customer service should be consistent across all touchpoints and interactions, regardless of the channel (e.g., phone, email, chat, in-person). Customers should receive the same level of service and attention each time they interact with the company.
- Customer Education: Providing education and guidance to customers can enhance their experience and satisfaction. Customer service representatives should proactively educate customers about product features, usage tips, troubleshooting techniques, and available resources to empower them to make informed decisions and maximize the value of their purchase.
- Feedback Management: Good customer service involves actively soliciting and listening to customer feedback to identify areas for improvement and enhance the overall customer experience. Customer service representatives should encourage feedback, respond constructively to complaints and suggestions, and use feedback to drive continuous improvement initiatives.
By embodying these qualities, organizations can deliver exceptional customer service that fosters loyalty, satisfaction, and positive word-of-mouth recommendations.
FAQs
What are military circuit boards?
Military circuit boards are specialized printed circuit boards (PCBs) designed and manufactured to meet the stringent requirements of military applications. They are built to withstand extreme environmental conditions, provide high reliability, and ensure durability in harsh operational environments.
What makes military circuit boards different from commercial ones?
Military circuit boards are designed and manufactured to comply with specific military standards and specifications, such as MIL-PRF-31032 or MIL-STD-810. They undergo rigorous testing and adhere to strict quality control measures to ensure reliability, durability, and performance in critical defense applications.
What are the key features of military circuit boards?
Military circuit boards feature robust construction, high reliability, and enhanced performance characteristics. They are designed to withstand extreme temperatures, humidity, shock, vibration, and electromagnetic interference (EMI). They also incorporate advanced technologies and materials for improved thermal management, signal integrity, and durability.
What are some common applications of military circuit boards?
Military circuit boards are used in a wide range of defense electronics and systems, including communication devices, radar systems, avionics, control systems, guidance systems, weapon systems, and surveillance equipment.
What standards govern the manufacturing of military circuit boards?
Military circuit boards must comply with various military standards and specifications, such as MIL-PRF-31032, MIL-STD-810, MIL-PRF-55110, and others. These standards cover design requirements, materials, manufacturing processes, testing procedures, and quality control measures.
How are military circuit boards tested for reliability and performance?
Military circuit boards undergo extensive testing to ensure reliability, performance, and compliance with military standards. Testing may include environmental testing (temperature, humidity, shock, vibration), thermal cycling, thermal shock, accelerated life testing, and electromagnetic compatibility (EMC) testing.
What materials are used in the construction of military circuit boards?
Military circuit boards may use high-quality substrate materials such as FR-4, polyimide, or specialty laminates. Copper foils, surface finishes (e.g., ENIG, immersion silver), and conformal coatings are also selected for their reliability, performance, and resistance to environmental factors.
How can I ensure that my military circuit boards meet the required specifications?
To ensure compliance with military standards and specifications, it is essential to work with experienced PCB manufacturers who have expertise in designing and manufacturing military-grade circuit boards. Additionally, thorough testing and quality control measures should be implemented throughout the manufacturing process.