Molded Interconnect Substrate Manufacturer
We are a professional Molded Interconnect Substrate Manufacturer, we mainly produce ultra-small bump pitch substrate, ultra-small trace and spacing packaging substrate and PCBs.
Molded Interconnect Substrates (MIS) revolutionize electronics manufacturing by seamlessly integrating structural and electrical functionalities into a single compact component. These substrates, typically composed of thermoplastic materials like polycarbonate or liquid crystal polymer, feature conductive traces and vias intricately embedded within their structure. MIS manufacturing involves advanced techniques such as laser ablation, printing conductive inks, or metal deposition to create precise electrical pathways directly onto the substrate material. The molding process encapsulates these features, yielding a monolithic structure that enhances design flexibility and reduces the size and weight of electronic devices. MIS find widespread applications across industries, including consumer electronics, automotive, medical devices, and aerospace, where space-saving, lightweight, and reliable solutions are paramount. With their ability to streamline production processes, improve electrical performance, and foster innovative designs, Molded Interconnect Substrates represent a significant advancement in electronics manufacturing technology.
What is a Molded Interconnect Substrate?
A Molded Interconnect Substrate (MIS) is a type of substrate used in electronics manufacturing, particularly in the production of compact and lightweight electronic devices. MIS integrates both the structural and electrical functions into a single molded component, typically made from a thermoplastic material like polycarbonate or liquid crystal polymer.
The MIS process involves creating conductive traces, vias, and other electronic features directly onto the substrate material. This is achieved through various methods such as laser ablation, metal deposition, or printing conductive inks. These features are then embedded or encapsulated within the substrate material through a molding process, forming a robust and compact structure.
One of the key advantages of MIS is its ability to reduce the size and weight of electronic devices while also simplifying the manufacturing process by eliminating the need for separate components like printed circuit boards (PCBs). Additionally, MIS can offer improved electrical performance and reliability due to shorter interconnect lengths and reduced parasitic effects.
MIS technology finds applications in a wide range of industries including consumer electronics, automotive, medical devices, and wearable technology, where space-saving and lightweight designs are critical. It enables the production of smaller, more durable, and functional electronic products that meet the demands of modern technology.
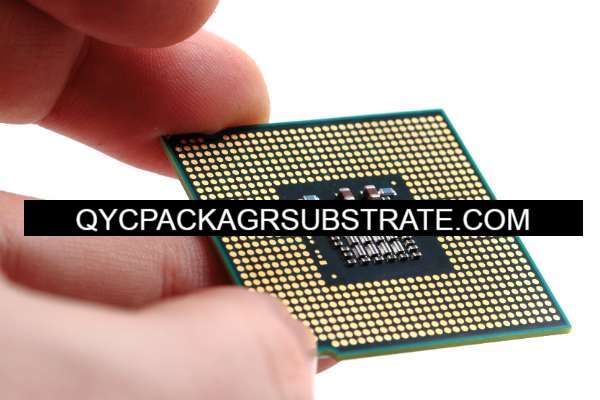
Molded Interconnect Substrate Manufacturer
What are the Molded Interconnect Substrate Design Guidelines?
Designing with Molded Interconnect Substrates (MIS) involves specific guidelines to ensure optimal performance and manufacturability. Here are some key design guidelines:
- Layer Stackup: Determine the layer stackup based on the specific requirements of the application, considering factors such as signal integrity, power distribution, and thermal management.
- Traces and Vias:Design traces and vias with appropriate widths and spacing to meet electrical requirements while ensuring manufacturability. Consider factors such as signal integrity, impedance control, and current carrying capacity.
- Component Placement: Optimize component placement to minimize signal path lengths, reduce parasitic effects, and optimize thermal management. Consider the spatial constraints and mechanical requirements of the device.
- Material Selection: Choose substrate materials based on electrical, mechanical, and thermal requirements of the application. Common materials include thermoplastics like polycarbonate or liquid crystal polymer (LCP).
- Circuit Design: Utilize design techniques such as controlled impedance routing, differential signaling, and proper grounding to ensure signal integrity and minimize electromagnetic interference (EMI).
- Encapsulation: Design the encapsulation process to ensure proper coverage and protection of electronic features. Consider factors such as material compatibility, adhesion, and thermal stability.
- Manufacturability: Design for manufacturability by considering the capabilities and limitations of the MIS fabrication process. Avoid complex geometries, sharp corners, and features that may compromise the integrity of the substrate.
- Testing and Inspection: Incorporate test points and inspection features into the design to facilitate testing and quality control during the manufacturing process.
- Environmental Considerations: Design for environmental robustness by selecting materials and coatings that can withstand temperature variations, humidity, and chemical exposure.
- Documentation: Provide detailed documentation including drawings, specifications, and assembly instructions to communicate design requirements effectively to manufacturers.
By following these design guidelines, engineers can create MIS designs that meet performance requirements, ensure reliability, and streamline the manufacturing process.
What is the Molded Interconnect Substrate Fabrication Process?
The fabrication process of Molded Interconnect Substrates (MIS) involves several steps to create the integrated structural and electrical components. Here’s a general overview of the fabrication process:
- Substrate Preparation: The process begins with the preparation of the substrate material, typically a thermoplastic polymer such as polycarbonate or liquid crystal polymer (LCP). The substrate material is typically in the form of sheets or pellets.
- Mold Design and Tooling: A mold is designed based on the desired substrate geometry and electrical features. The mold consists of cavities and channels that define the shape of the substrate and accommodate the placement of conductive traces and vias.
- Conductive Feature Deposition: Conductive features such as traces, pads, and vias are deposited onto the substrate material using various methods such as laser ablation, printing conductive inks, or metal deposition techniques like sputtering or plating. These features define the electrical interconnections within the substrate.
- Molding Process: The substrate material, with the conductive features deposited on it, is placed into the mold cavities. The mold is then closed, and the substrate material is heated to its melting point, allowing it to flow and conform to the shape of the mold. This process encapsulates the conductive features within the substrate material, creating a monolithic structure.
- Cooling and Solidification: After molding, the substrate material is cooled and allowed to solidify, maintaining the shape and integrity of the molded part. Cooling may occur gradually to prevent warping or deformation of the substrate.
- Post-Processing: Once the substrate has solidified, post-processing steps may be performed, including trimming excess material, surface finishing, and applying coatings or protective layers to enhance electrical performance and durability.
- Quality Control and Testing: The fabricated MIS undergoes quality control measures to ensure that it meets the specified electrical and mechanical requirements. This may involve visual inspection, electrical testing, and dimensional verification.
- Assembly Integration: Finally, the fabricated MIS may be integrated into larger electronic assemblies or devices through processes such as soldering, adhesive bonding, or mechanical fastening, depending on the application requirements.
Overall, the fabrication process of Molded Interconnect Substrates combines traditional molding techniques with advanced electronics manufacturing methods to create compact, lightweight, and highly integrated electronic components.
How do you manufacture a Molded Interconnect Substrate?
Manufacturing a Molded Interconnect Substrate (MIS) involves a combination of traditional molding processes with specialized techniques for depositing conductive features onto the substrate material. Here’s a step-by-step overview of the manufacturing process:
- Substrate Material Preparation:The process begins with preparing the substrate material, which is typically a thermoplastic polymer such as polycarbonate, liquid crystal polymer (LCP), or similar materials. The substrate material is usually in the form of sheets or pellets.
- Mold Design and Fabrication: A mold is designed based on the desired shape and features of the MIS. The mold consists of cavities and channels that define the substrate geometry and accommodate the placement of conductive traces and vias. The mold is typically made from steel or aluminum and is precision machined to high tolerances.
- Conductive Feature Deposition: Conductive features such as traces, pads, and vias are deposited onto the substrate material using specialized techniques. Common methods include laser ablation, printing conductive inks, or metal deposition techniques like sputtering or plating. These features define the electrical interconnections within the substrate.
- Molding Process: The substrate material, with the deposited conductive features, is placed into the mold cavities. The mold is then closed, and the substrate material is heated to its melting point, allowing it to flow and conform to the shape of the mold. This process encapsulates the conductive features within the substrate material, forming a monolithic structure.
- Cooling and Solidification: After molding, the substrate material is cooled and allowed to solidify, maintaining the shape and integrity of the molded part. Cooling may occur gradually to prevent warping or deformation of the substrate.
- Post-Processing: Once the substrate has solidified, post-processing steps may be performed. This can include trimming excess material, surface finishing, and applying coatings or protective layers to enhance electrical performance and durability.
- Quality Control and Testing: The manufactured MIS undergoes rigorous quality control measures to ensure that it meets the specified electrical and mechanical requirements. This may involve visual inspection, electrical testing, and dimensional verification.
- Assembly Integration: Finally, the MIS may be integrated into larger electronic assemblies or devices through processes such as soldering, adhesive bonding, or mechanical fastening, depending on the application requirements.
Throughout the manufacturing process, careful attention is paid to maintaining the integrity of the conductive features and ensuring that the final product meets the required performance standards.
How much should a Molded Interconnect Substrate cost?
The cost of a Molded Interconnect Substrate (MIS) can vary widely depending on several factors, including:
- Material Cost: The cost of the substrate material itself, which can vary based on factors such as material type (e.g., polycarbonate, liquid crystal polymer), grade, and supplier pricing.
- Manufacturing Process Complexity: The complexity of the manufacturing process, including the number of layers, the intricacy of the design, and the required precision of features, can significantly impact the cost.
- Conductive Feature Deposition: The method used for depositing conductive features onto the substrate material, such as laser ablation, printing conductive inks, or metal deposition techniques, can affect the overall cost.
- Mold Design and Fabrication: The cost of designing and fabricating the molds used in the manufacturing process can vary depending on factors such as mold complexity, material type, and machining requirements.
- Volume and Scale:Economies of scale can impact the cost, with larger production volumes generally leading to lower per-unit costs due to efficiencies in manufacturing and material procurement.
- Quality Requirements: If stringent quality requirements are necessary, such as tight tolerances, specific performance characteristics, or regulatory compliance, additional testing and quality control measures may increase the overall cost.
- Additional Processes: Any additional processes required, such as post-processing steps (e.g., trimming, surface finishing, coating), assembly integration, or testing, can add to the total cost.
Given these factors, it’s challenging to provide a specific cost estimate without more detailed information about the specific requirements of the MIS, such as the design complexity, material specifications, and production volume. Typically, MIS costs are determined on a case-by-case basis by manufacturers based on these factors and customer-specific needs.
What is Molded Interconnect Substrate base material?
The base material used in Molded Interconnect Substrates (MIS) is typically a thermoplastic polymer. Common materials include:
- Polycarbonate: Known for its high impact strength, temperature resistance, and optical clarity, polycarbonate is a popular choice for MIS applications. It offers good dimensional stability and can be easily molded into complex shapes.
- Liquid Crystal Polymer (LCP): LCP is another common substrate material for MIS. It has excellent chemical resistance, low moisture absorption, and high temperature performance. LCP can be molded with precision, making it suitable for intricate designs.
- Polyethylene Terephthalate (PET):PET is a widely used thermoplastic polymer known for its excellent mechanical properties, chemical resistance, and dimensional stability. It is often used in applications where cost-effectiveness is a primary consideration.
- Polyethylene Naphthalate (PEN):Similar to PET, PEN offers high mechanical strength, thermal stability, and chemical resistance. It is commonly used in applications requiring high-temperature performance.
These base materials provide the structural foundation for MIS and serve as the substrate onto which conductive features are deposited. The choice of base material depends on various factors such as mechanical requirements, thermal performance, chemical resistance, and cost considerations, as well as the specific needs of the application.
Which company makes Molded Interconnect Substrates?
Many companies have extensive experience and technology in manufacturing Molded Interconnect Substrates (MIS). For example, companies such as Mitsubishi Electric in Japan, LPKF Laser & Electronics in the United States, and LPKF in Germany have demonstrated outstanding performance in the field of MIS manufacturing. These companies utilize advanced processes and technologies to produce high-quality, high-performance MIS, which are widely used in electronics, automotive, medical devices, and other industries.
Our company also has the capability to manufacture Molded Interconnect Substrates. We have an experienced R&D team proficient in advanced MIS manufacturing technologies. Our production process includes:
- Design and Engineering: Our engineering team can design MIS structures that meet customer requirements, taking into account factors such as circuit layout, signal integrity, and thermal management.
- Material Selection and Procurement: We choose high-quality base materials such as polycarbonate (PC) and liquid crystal polymer (LCP) as the substrate materials for MIS and ensure the reliability and stability of the materials.
- Production Process and Manufacturing: We have advanced production equipment and process technologies to achieve precision processing and molding of MIS. We use various methods such as laser ablation, printing conductive inks, and metal deposition to integrate conductive circuits and components directly into the MIS substrate.
- Quality Control and Testing: We strictly adhere to quality management systems to ensure that each batch of products meets customer requirements and standards. We conduct rigorous inspections and testing, including visual inspection, electrical performance testing, and dimensional measurement, to ensure product quality.
- Customized Production and Services:We can provide customized MIS solutions according to customer requirements and offer comprehensive technical support and after-sales service to ensure customer satisfaction.
With our professional team, advanced technology, and strict quality control, our company can provide high-quality, high-performance Molded Interconnect Substrates to meet the various application needs of customers.
What are the 7 qualities of good customer service?
Good customer service is essential for building strong relationships with customers and fostering loyalty. Here are seven qualities that contribute to good customer service:
- Responsiveness: A good customer service representative is responsive and attentive to customers’ needs. They promptly address inquiries, concerns, or issues raised by customers, demonstrating a willingness to help and resolve problems in a timely manner.
- Empathy: Empathy is the ability to understand and share the feelings of others. Good customer service involves empathizing with customers’ situations, showing compassion, and acknowledging their emotions. Empathetic responses help build rapport and trust with customers.
- Communication Skills: Effective communication is crucial in customer service. Good customer service representatives communicate clearly and courteously, both verbally and in writing. They listen actively to customers, ask clarifying questions, and provide information or solutions in a way that is easy to understand.
- Problem-Solving Abilities: Good customer service involves being able to identify and solve customers’ problems effectively. Customer service representatives should have strong problem-solving skills, using creativity and resourcefulness to find solutions that meet customers’ needs and expectations.
- Product Knowledge: Customer service representatives should have a thorough understanding of the products or services offered by the company. This enables them to provide accurate information, answer questions, and offer relevant advice or recommendations to customers.
- Professionalism: Professionalism is essential in customer service interactions. Good customer service representatives maintain a positive attitude, remain calm under pressure, and conduct themselves with integrity and respect. They handle difficult situations with professionalism and strive to leave customers feeling valued and satisfied.
- Follow-Up and Accountability:After resolving a customer’s issue or inquiry, good customer service includes following up to ensure that the customer is satisfied with the resolution. Additionally, taking accountability for any mistakes or shortcomings and taking steps to rectify them demonstrates a commitment to customer satisfaction and continuous improvement.
By embodying these qualities, businesses can deliver exceptional customer service experiences that build loyalty, enhance reputation, and drive long-term success.
FAQs
What are Molded Interconnect Substrates (MIS)?
Molded Interconnect Substrates (MIS) are structural components used in electronics manufacturing, integrating both the mechanical structure and electrical interconnects into a single molded part. They typically consist of a thermoplastic substrate material with conductive traces, vias, and other electronic features embedded within.
What are the advantages of using MIS?
MIS offer several advantages including reduced size and weight of electronic devices, simplified manufacturing processes, improved electrical performance due to shorter interconnect lengths, and enhanced reliability compared to traditional printed circuit boards (PCBs).
What industries use MIS?
MIS find applications in various industries including consumer electronics, automotive, medical devices, aerospace, and telecommunications. They are used in a wide range of products such as smartphones, wearables, automotive sensors, and medical implants.
How are MIS manufactured?
The manufacturing process of MIS involves depositing conductive features onto a thermoplastic substrate material, usually through techniques like laser ablation, printing conductive inks, or metal deposition. The substrate material is then molded to encapsulate the conductive features, forming a monolithic structure.
What materials are used in MIS?
Common substrate materials used in MIS include polycarbonate (PC), liquid crystal polymer (LCP), polyethylene terephthalate (PET), and polyethylene naphthalate (PEN). These materials offer properties such as high strength, thermal stability, and chemical resistance.
What are the design considerations for MIS?
Designing with MIS requires considerations such as layer stackup, traces and vias design, component placement, material selection, manufacturability, environmental factors, and testing and inspection requirements.
What are the cost considerations for MIS?
The cost of MIS can vary depending on factors such as material cost, manufacturing process complexity, volume and scale of production, quality requirements, and additional processes such as testing and assembly integration.