Radar/Antenna Substrate Manufacturer
Radar/Antenna Substrate Manufacturer. we can produce the best samllest bump pitch with 100um, the best smallest trace are 9um. and the smallest gap are 9um. most of the design are 15um to 30um trace and spacing. To use the High frequency and high speed materials.
Radar/antenna substrate is a crucial component used to support and transmit radio frequency (RF) signals. Typically made of dielectric materials such as polytetrafluoroethylene (PTFE) or ceramics, these substrates possess characteristics of low loss and high dielectric constant to ensure efficient signal transmission and reception. The design and fabrication of radar/antenna substrates are paramount as they directly impact the performance and stability of antennas. High-quality substrates offer higher signal transmission efficiency and lower signal attenuation, thereby enhancing the sensitivity and accuracy of radar systems. Additionally, radar/antenna substrates must exhibit good heat resistance and mechanical strength to accommodate various environmental conditions and operational requirements. Overall, radar/antenna substrates play an indispensable role in modern radar technology, serving as vital components to ensure system stability and performance.
What is a Radar/Antenna Substrate?
A radar/antenna substrate is a critical component in radar and antenna systems, providing a stable platform for mounting and integrating various electronic components. It serves as the base material upon which the radar or antenna elements are constructed. The substrate typically consists of materials with specific electromagnetic properties tailored to the application’s frequency range, such as fiberglass, ceramics, or specialized composites.
In addition to providing structural support, the substrate must also exhibit properties conducive to efficient electromagnetic wave propagation. These properties include low dielectric loss, high dielectric constant, and uniformity in material composition to minimize signal distortion and maximize antenna performance.
Furthermore, radar/antenna substrates often incorporate features such as printed circuit traces, vias, and impedance-matching structures to facilitate the connection between the antenna elements and the associated electronic circuitry. These features are crucial for achieving desired radiation patterns, impedance matching, and signal integrity.
The design and selection of radar/antenna substrates are influenced by various factors, including operating frequency, power requirements, environmental conditions, and size constraints. Advanced manufacturing techniques, such as printed circuit board (PCB) fabrication and additive manufacturing, enable the production of substrates with intricate designs and precise electromagnetic characteristics tailored to specific radar and antenna applications.
In summary, a radar/antenna substrate is a foundational component that plays a vital role in the performance and functionality of radar and antenna systems, providing support for antenna elements while ensuring optimal electromagnetic properties for efficient signal transmission and reception.
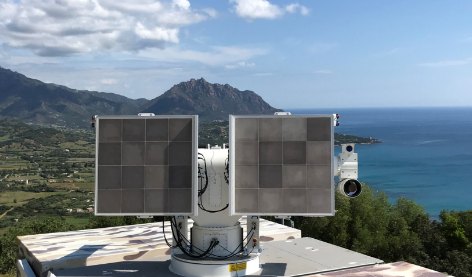
Radar/Antenna Substrate
What are the Radar/Antenna Substrate Design Guidelines?
Designing radar/antenna substrates involves adhering to several guidelines to ensure optimal performance. Here are some key considerations:
- Material Selection: Choose a substrate material with appropriate electromagnetic properties for the desired frequency range. Common materials include fiberglass, ceramics, and specialized composites.
- Dielectric Constant: Opt for a substrate with a consistent dielectric constant to ensure uniform signal propagation and minimize impedance variations across the antenna array.
- Low Loss Tangent: Select a substrate with a low loss tangent to minimize signal attenuation and ensure high efficiency in signal transmission and reception.
- Dimensional Stability: Ensure the substrate material exhibits minimal dimensional changes with temperature variations to maintain antenna performance across different environmental conditions.
- Mechanical Strength: The substrate should possess sufficient mechanical strength to support the antenna elements and withstand mechanical stresses during handling and operation.
- Surface Smoothness: A smooth substrate surface is essential for precise fabrication of antenna elements and to minimize scattering losses.
- Printed Circuit Traces and Vias: Design printed circuit traces and vias on the substrate with appropriate dimensions and spacing to minimize signal losses and impedance mismatches.
- Impedance Matching Structures: Incorporate impedance matching structures, such as microstrip lines or matching networks, to ensure efficient power transfer between the antenna elements and the associated electronics.
- Environmental Considerations: Account for environmental factors such as moisture, temperature, and humidity in substrate selection and design to maintain long-term reliability and performance.
- Manufacturability: Ensure that the substrate design is compatible with the chosen manufacturing processes, such as PCB fabrication or additive manufacturing, to enable cost-effective production without sacrificing performance.
By following these guidelines, designers can develop radar/antenna substrates that meet the specific requirements of their applications, resulting in optimal performance and reliability.
What is the Radar/Antenna Substrate Fabrication Process?
The fabrication process for radar/antenna substrates involves several steps to create a stable platform for mounting antenna elements and integrating electronic components. Here’s a general overview of the typical fabrication process:
- Substrate Material Selection: Choose a substrate material with suitable electromagnetic properties for the desired frequency range, such as fiberglass, ceramics, or specialized composites.
- Preparation: Prepare the substrate material by cutting it to the desired size and shape using cutting tools or precision machining techniques. Ensure that the substrate surface is clean and free from contaminants.
- Surface Treatment: Treat the substrate surface to improve adhesion and enhance electrical properties. Surface treatment methods may include chemical etching, plasma treatment, or the application of adhesion-promoting layers.
- Printed Circuit Board (PCB) Fabrication (if applicable): If the substrate incorporates printed circuit traces or components, use PCB fabrication techniques to pattern conductive traces, vias, and pads on the substrate surface. This process typically involves photolithography, etching, and metal deposition steps.
- Antenna Element Integration: Mount and integrate antenna elements onto the substrate surface using adhesive bonding or soldering techniques. Ensure precise placement and alignment of the antenna elements to achieve the desired radiation pattern and impedance matching.
- Impedance Matching: Implement impedance matching structures, such as microstrip lines or matching networks, to optimize the impedance matching between the antenna elements and the associated electronics.
- Encapsulation (optional): Optionally, encapsulate the substrate and antenna elements with a protective coating or housing to improve durability, weather resistance, and mechanical stability.
- Quality Assurance: Perform quality control checks throughout the fabrication process to ensure dimensional accuracy, electrical integrity, and adherence to design specifications. This may include visual inspections, electrical testing, and dimensional measurements.
- Final Testing and Validation: Conduct final testing and validation of the fabricated radar/antenna substrate to verify performance characteristics such as impedance matching, radiation pattern, and signal transmission/reception efficiency.
By following these fabrication steps, manufacturers can produce radar/antenna substrates that meet the stringent requirements of modern radar and antenna systems, ensuring reliable and high-performance operation in various applications.
How do you manufacture a Radar/Antenna Substrate?
Manufacturing a radar/antenna substrate involves a series of precise steps to create a stable platform for antenna elements and electronic components. Here’s a detailed overview of the manufacturing process:
- Material Selection: Choose a substrate material with suitable electromagnetic properties for the desired frequency range. Common materials include fiberglass-reinforced epoxy laminates (FR4), ceramics, or specialized composites.
- Preparation of Substrate Material: Begin by cutting the substrate material to the desired size and shape using precision cutting tools or machining techniques. Ensure that the substrate surface is clean and free from any contaminants.
- Surface Treatment: Treat the substrate surface to improve adhesion and electrical properties. Surface treatment methods may include chemical etching, plasma treatment, or the application of adhesion-promoting layers.
- Printed Circuit Board (PCB) Fabrication (if applicable): If the substrate incorporates printed circuit traces or components, utilize PCB fabrication techniques. This involves patterning conductive traces, vias, and pads on the substrate surface through processes like photolithography, etching, and metal deposition.
- Antenna Element Integration: Mount and integrate antenna elements onto the substrate surface. This can be done using adhesive bonding or soldering techniques. Ensure precise placement and alignment of the antenna elements to achieve the desired radiation pattern and impedance matching.
- Impedance Matching Structures: Implement impedance matching structures, such as microstrip lines or matching networks, to optimize the impedance matching between the antenna elements and associated electronics.
- Encapsulation (optional): Optionally, encapsulate the substrate and antenna elements with a protective coating or housing. This helps improve durability, weather resistance, and mechanical stability, especially in harsh environments.
- Quality Assurance: Throughout the manufacturing process, conduct quality control checks to ensure dimensional accuracy, electrical integrity, and adherence to design specifications. Visual inspections, electrical testing, and dimensional measurements are typical methods used for quality assurance.
- Final Testing and Validation: Once manufacturing is complete, perform final testing and validation of the radar/antenna substrate. This involves verifying performance characteristics such as impedance matching, radiation pattern, and signal transmission/reception efficiency. Testing may include simulations, lab measurements, and field trials.
- Documentation and Packaging: Document the manufacturing process and specifications for future reference. Package the finished radar/antenna substrates securely to protect them during transportation and storage.
By meticulously following these manufacturing steps, manufacturers can produce radar/antenna substrates that meet the stringent requirements of modern radar and antenna systems, ensuring reliable and high-performance operation in various applications.
How much should a Radar/Antenna Substrate cost?
The cost of a radar/antenna substrate can vary widely depending on several factors, including:
- Material: The choice of substrate material greatly influences the cost. Basic materials like FR4 may be more affordable compared to specialized composites or high-frequency ceramics.
- Complexity: The complexity of the substrate design, including the presence of printed circuit traces, impedance matching structures, and integrated components, can impact the cost of fabrication.
- Manufacturing Process: Different manufacturing processes have varying costs associated with them. For example, PCB fabrication using traditional methods like photolithography and etching may be less expensive than additive manufacturing techniques.
- Quantity: Economies of scale often apply in manufacturing. Larger quantities typically result in lower per-unit costs due to efficiencies in materials, labor, and equipment utilization.
- Quality and Tolerance Requirements: Meeting stringent quality standards and tight tolerance requirements may involve additional costs for inspection, testing, and quality assurance measures.
- Customization: Customized designs or unique specifications may incur additional engineering and setup costs, especially if they require specialized tooling or processes.
- Supplier and Location: The choice of supplier and their location can impact costs due to factors like labor rates, overhead expenses, and shipping logistics.
- Market Dynamics: Market demand and competition can also influence pricing. In a competitive market, prices may be lower, while niche or specialized products may command higher prices.
Given these factors, it’s challenging to provide a specific cost without detailed information about the substrate’s specifications, quantity, and manufacturing requirements. Typically, companies involved in radar/antenna substrate manufacturing would provide quotes based on the project’s specific needs and specifications.
What is a Radar/Antenna Substrate base material?
The base material for radar/antenna substrates can vary depending on the specific requirements of the application, but several common materials are frequently used. Some of the typical base materials for radar/antenna substrates include:
- Fiberglass-Reinforced Epoxy Laminates (FR4):FR4 is a widely used substrate material in electronics and PCB fabrication due to its cost-effectiveness, mechanical strength, and electrical properties suitable for a broad range of frequencies.
- Rogers and Taconic High-Frequency Laminates: These specialized laminates are engineered specifically for high-frequency applications and offer low dielectric loss, tight control over dielectric constant, and excellent dimensional stability.
- Ceramics: Certain types of ceramics, such as alumina (Al2O3) or aluminum nitride (AlN), are favored for their high thermal conductivity, low dielectric loss, and compatibility with high-power applications. They are commonly used in radar systems operating at microwave frequencies.
- Polytetrafluoroethylene (PTFE)-Based Materials (e.g., Teflon): PTFE-based substrates offer low dielectric loss and excellent electrical properties, making them suitable for high-frequency radar and antenna applications.
- Polyimide Films: Polyimide films provide flexibility and thermal stability, making them suitable for flexible or conformal antenna designs and applications requiring resistance to high temperatures.
- Liquid Crystal Polymer (LCP): LCP substrates offer low dielectric constant and low moisture absorption, making them suitable for high-frequency applications where signal integrity is critical.
- Metal-Core Substrates: These substrates consist of a metal core sandwiched between dielectric layers, providing enhanced thermal conductivity and mechanical stability. They are commonly used in high-power radar systems.
The choice of substrate base material depends on various factors such as operating frequency, power requirements, thermal management needs, mechanical constraints, and cost considerations. Designers select the material that best balances these requirements to achieve optimal performance in radar and antenna systems.
Which company makes Radar/Antenna Substrates?
Many companies manufacture radar/antenna substrates, including well-known ones like Rogers Corporation, Taconic Advanced Dielectric Division, Isola Group, Park Electrochemical Corp, as well as material suppliers such as Panasonic, Nelco, and others. These companies offer various types of substrate materials, including specialized materials for high-frequency and microwave applications.
As for our company, we are also one of the manufacturers of radar/antenna substrates. We have advanced manufacturing equipment and technologies to produce substrates that meet high standards and customized requirements. Our manufacturing process covers material preparation, substrate processing, printed circuit board (PCB) fabrication (if applicable), antenna element integration, impedance matching structure implementation, quality assurance, final testing, and more.
Our production process has the following advantages:
- Customization: We can customize substrates according to specific customer requirements, including different material selections, complex PCB wiring, special impedance matching structures, etc.
- Quality Assurance: We strictly control the production process and implement a comprehensive quality management system to ensure the quality and reliability of each production step.
- Technical Strength: We have an experienced team of engineers and technicians who can provide professional technical support and solutions.
- Fast Delivery: With strong production capabilities, we can deliver customer orders on time to ensure that their project schedules are not affected.
- Reasonable Price: We offer competitive prices while ensuring that product quality and performance meet customer expectations.
In summary, as a professional manufacturer of radar/antenna substrates, our company has the ability to produce high-quality, customized substrates and is committed to providing customers with quality products and services.
What are the 7 qualities of good customer service?
Good customer service is essential for building positive relationships with customers and ensuring their satisfaction. Here are seven qualities that characterize good customer service:
- Responsiveness: Being responsive means promptly addressing customer inquiries, concerns, and requests. Responding in a timely manner demonstrates that you value the customer’s time and are committed to providing assistance when needed.
- Empathy: Empathy involves understanding and acknowledging the customer’s feelings, perspectives, and needs. Showing empathy helps build rapport and trust with customers by demonstrating that you genuinely care about their experience and are willing to listen to their concerns.
- Clarity: Providing clear and concise communication is crucial for delivering effective customer service. Use simple language, avoid jargon, and ensure that customers understand the information you provide. Clear communication helps prevent misunderstandings and confusion.
- Professionalism: Maintaining professionalism in interactions with customers is essential for creating a positive impression and fostering trust. This includes being polite, respectful, and courteous at all times, even in challenging situations. Professionalism also involves demonstrating competence and confidence in addressing customer issues.
- Problem-Solving Skills: Good customer service representatives possess strong problem-solving skills to effectively resolve customer issues and concerns. This involves actively listening to the customer, identifying the root cause of the problem, and proposing appropriate solutions in a timely manner.
- Adaptability: Adaptability is the ability to adjust and respond effectively to changing customer needs, preferences, and situations. Good customer service involves being flexible and adaptable in finding solutions that meet the unique requirements of each customer.
- Follow-Up: Following up with customers after resolving an issue or completing a transaction demonstrates commitment to their satisfaction and reinforces the relationship. Follow-up communication can include seeking feedback, offering additional assistance if needed, or expressing appreciation for their business.
By embodying these qualities, businesses can deliver exceptional customer service experiences that foster loyalty, retention, and positive word-of-mouth recommendations.
FAQs
What is a radar/antenna substrate?
A radar/antenna substrate is a base material used for mounting and integrating radar and antenna components. It provides structural support and facilitates efficient electromagnetic wave propagation.
What materials are commonly used for radar/antenna substrates?
Common materials include fiberglass-reinforced epoxy laminates (FR4), ceramics, Rogers and Taconic high-frequency laminates, polytetrafluoroethylene (PTFE)-based materials, polyimide films, liquid crystal polymers (LCP), and metal-core substrates.
What are the key considerations when selecting a radar/antenna substrate?
Important factors to consider include the substrate’s electromagnetic properties, such as dielectric constant and loss tangent, dimensional stability, mechanical strength, surface smoothness, and compatibility with the operating frequency and environmental conditions.
What manufacturing processes are involved in producing radar/antenna substrates?
The manufacturing process typically includes material preparation, surface treatment, printed circuit board (PCB) fabrication (if applicable), antenna element integration, impedance matching structure implementation, encapsulation (optional), quality assurance, and final testing.
What are the advantages of using radar/antenna substrates?
Radar/antenna substrates provide a stable platform for mounting antenna elements and integrating electronic components. They help optimize electromagnetic performance, ensure signal integrity, and enhance overall system reliability and efficiency.
What customization options are available for radar/antenna substrates?
Substrates can be customized based on specific application requirements, including material selection, PCB layout, impedance matching structures, and encapsulation options. Customization allows for tailored solutions to meet the unique needs of different radar and antenna systems.
How can I ensure the quality and reliability of radar/antenna substrates?
Quality assurance measures, such as strict process control, comprehensive testing, and adherence to industry standards, are essential to ensure the quality and reliability of radar/antenna substrates. Working with reputable manufacturers with a proven track record of delivering high-quality products is also important.