Showa Denko MCL-E-700G package substrate Manufacturer
What is a Showa Denko MCL-E-700G package substrate?
Showa Denko MCL-E-700G package substrate Manufacturer, the Package Substrate will be made with Showa Denko and Ajinomoto High speed materials.or other types high speed materials and high frequency materials.
The Showa Denko MCL-E-700G package substrate is a high-performance substrate used in semiconductor packaging. It serves as a foundation for mounting and interconnecting semiconductor chips within electronic devices like smartphones, computers, and automotive electronics.
The substrate provides electrical connections between the semiconductor chips and the device’s circuitry while offering thermal management to dissipate heat generated during operation. Its design and materials are optimized for reliability, durability, and electrical performance, ensuring stable operation of the integrated circuits even under demanding conditions.
The MCL-E-700G substrate is engineered by Showa Denko, a leading Japanese company specializing in chemical and electronic materials. Its precise manufacturing process ensures tight tolerances and uniformity across substrates, crucial for the consistent performance of semiconductor devices.
Key features of the MCL-E-700G substrate include its high thermal conductivity, low coefficient of thermal expansion (CTE), excellent electrical insulation properties, and compatibility with various assembly processes such as flip-chip and wire bonding.
In summary, the Showa Denko MCL-E-700G package substrate is a cutting-edge component essential for the reliable operation of modern semiconductor devices, enabling high-performance electronics in diverse applications.
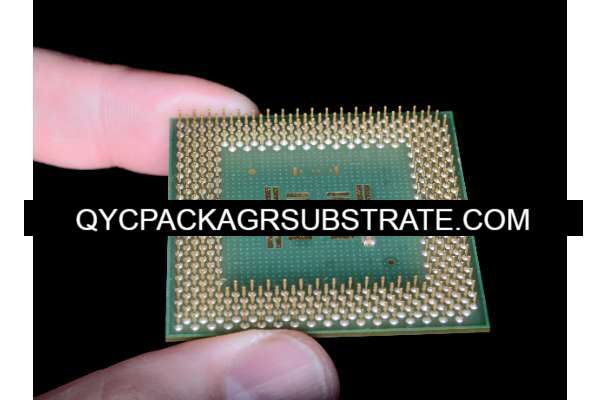
Showa Denko MCL-E-700G package substrate Manufacturer
What are the Showa Denko MCL-E-700G package substrate design guidelines?
Specific design guidelines for the Showa Denko MCL-E-700G package substrate may vary depending on the application and requirements of the semiconductor device being manufactured. However, some general design principles typically apply:
- Thermal Management: The substrate should be designed to effectively dissipate heat generated by the semiconductor chips during operation. This includes proper placement of thermal vias, thermal pads, and heat spreaders to facilitate efficient heat transfer away from the chips.
- Electrical Performance: The substrate design should ensure optimal electrical connectivity between the semiconductor chips and the device’s circuitry. This involves minimizing signal loss, impedance mismatches, and crosstalk through careful routing of signal traces and power planes.
- Mechanical Integrity:The substrate must provide mechanical support for the semiconductor chips and withstand mechanical stresses encountered during assembly, handling, and operation. Adequate reinforcement and proper selection of materials are crucial to prevent substrate warping, cracking, or delamination.
- Signal Integrity: Design considerations should address signal integrity issues such as signal reflections, skew, and noise. Signal traces should be routed to minimize signal degradation and maintain signal integrity across the substrate.
- Manufacturability: The substrate design should be compatible with the manufacturing processes used by Showa Denko or its partners. This includes considerations for fabrication techniques, materials compatibility, and assembly processes to ensure efficient and cost-effective production.
- Reliability: The substrate design should meet reliability standards and industry regulations to ensure the long-term performance and durability of the semiconductor device. This may involve incorporating features such as solder mask layers, protective coatings, and reliability testing protocols into the substrate design.
By adhering to these design guidelines, manufacturers can optimize the performance, reliability, and manufacturability of semiconductor devices utilizing the Showa Denko MCL-E-700G package substrate.
What is the Showa Denko MCL-E-700G package substrate fabrication process?
The fabrication process of the Showa Denko MCL-E-700G package substrate involves several steps, typically including:
- Substrate Material Selection: The process begins with selecting suitable substrate materials based on the desired properties such as thermal conductivity, electrical insulation, and mechanical strength. Showa Denko likely utilizes advanced materials such as ceramic or organic substrates with specialized formulations to meet these requirements.
- Substrate Preparation: The selected substrate materials undergo preparation steps such as cleaning and surface treatment to ensure proper adhesion of subsequent layers and facilitate the deposition of circuit patterns.
- Circuit Pattern Formation: Circuit patterns are created on the substrate using processes like lithography and etching. A photoresist material is applied to the substrate, patterned with the desired circuit layout using photolithography techniques, and then selectively etched to remove material and define the circuit traces.
- Metal Deposition: Thin metal layers, typically copper or aluminum, are deposited onto the substrate to form the conductive traces that interconnect semiconductor chips and other components. This can be achieved through techniques like physical vapor deposition (PVD) or electroplating.
- Dielectric Layer Formation: Dielectric layers are deposited or laminated onto the substrate to insulate the conductive traces and provide electrical isolation between circuit layers. These dielectric layers may consist of materials such as epoxy resin or polyimide, applied through techniques like spin coating or lamination.
- Via Formation: Vias, which are conductive pathways between different circuit layers, are formed by drilling or laser ablation through the dielectric layers. The vias are then filled with conductive material such as copper through processes like electroplating to establish electrical connections between circuit layers.
- Surface Finish: Surface finish treatments are applied to the substrate to enhance solderability and protect against oxidation. Common surface finishes include immersion tin, immersion silver, and gold plating.
- Quality Control and Testing:Throughout the fabrication process, stringent quality control measures are implemented to ensure the substrate meets the specified requirements for dimensional accuracy, electrical performance, and reliability. Various testing methods such as electrical testing, thermal cycling, and visual inspection may be conducted to validate the substrate’s quality.
By following these fabrication steps with precision and utilizing advanced manufacturing techniques, Showa Denko produces the MCL-E-700G package substrate with high performance, reliability, and consistency to meet the demanding requirements of semiconductor packaging applications.
How do you manufacture a Showa Denko MCL-E-700G package substrate?
Manufacturing a Showa Denko MCL-E-700G package substrate involves a series of intricate processes, carefully orchestrated to ensure high quality and performance. While the exact details of Showa Denko’s proprietary manufacturing process may not be publicly disclosed, I can provide a general overview based on common practices in the industry:
- Substrate Material Preparation: The process starts with the preparation of substrate materials, which are typically advanced ceramics or organic materials with tailored properties such as thermal conductivity, electrical insulation, and mechanical strength. These materials may undergo cleaning, surface treatment, and shaping to achieve the desired specifications.
- Circuit Design and Layout: The substrate’s circuitry layout is designed using specialized software, taking into account factors such as signal integrity, thermal management, and manufacturability. The layout includes the arrangement of conductive traces, vias, bonding pads, and other features necessary for interconnecting semiconductor chips and components.
- Circuit Pattern Formation: The designed circuit pattern is transferred onto the substrate using processes like photolithography and etching. A layer of photoresist material is applied to the substrate, exposed to UV light through a photomask containing the circuit pattern, and developed to define the desired circuit traces and features. Chemical etching then selectively removes material to create the circuit pattern on the substrate.
- Conductive Layer Deposition: Thin layers of conductive material, typically copper or aluminum, are deposited onto the substrate to form the conductive traces and bonding pads. This can be achieved through techniques like physical vapor deposition (PVD), chemical vapor deposition (CVD), or electroplating.
- Dielectric Layer Formation: Dielectric layers are applied to insulate the conductive traces and provide electrical isolation between circuit layers. These dielectric layers may consist of materials such as epoxy resin, polyimide, or glass-reinforced materials, applied through processes like spin coating, screen printing, or lamination.
- Via Formation: Vias, which are conductive pathways between different circuit layers, are formed by drilling, laser ablation, or other techniques. The vias are then filled with conductive material such as copper or conductive paste to establish electrical connections between circuit layers.
- Surface Finish: Surface finish treatments are applied to the substrate to enhance solderability, protect against oxidation, and improve electrical performance. Common surface finishes include immersion tin, immersion silver, gold plating, and organic solderability preservatives (OSP).
- Quality Control and Testing: Throughout the manufacturing process, rigorous quality control measures are implemented to ensure the substrate meets the specified requirements for dimensional accuracy, electrical performance, reliability, and consistency. Various testing methods such as electrical testing, thermal cycling, and visual inspection are conducted to validate the substrate’s quality before it is released for further assembly and integration into semiconductor devices.
By meticulously executing these manufacturing steps and leveraging advanced technologies and materials, Showa Denko produces the MCL-E-700G package substrate with high precision, reliability, and performance to meet the demanding requirements of semiconductor packaging applications.
How much should a Showa Denko MCL-E-700G package substrate cost?
Determining the exact cost of a Showa Denko MCL-E-700G package substrate can be challenging without specific pricing information from Showa Denko or its distributors. The cost of the substrate can vary depending on several factors including:
- Volume and Quantity: Typically, purchasing larger quantities of substrates can lead to lower unit costs due to economies of scale. Bulk orders may be eligible for volume discounts.
- Customization: If the substrate requires custom specifications, designs, or features tailored to a specific application, the cost may be higher to account for additional engineering and manufacturing expenses.
- Material Costs: The cost of raw materials used in the substrate’s fabrication, including specialized ceramics, metals, and dielectric materials, can significantly impact the overall cost.
- Manufacturing Complexity: Substrates with intricate designs, multiple layers, fine features, and tight tolerances may require more sophisticated manufacturing processes and equipment, resulting in higher production costs.
- Quality and Reliability: High-quality substrates manufactured to stringent quality standards may command a premium price due to their superior performance, reliability, and consistency.
- Market Conditions: Supply and demand dynamics, fluctuations in material prices, and competitive pressures within the semiconductor industry can influence substrate pricing.
Given these factors, the cost of a Showa Denko MCL-E-700G package substrate is likely to vary depending on the specific requirements of the customer, the quantity ordered, and prevailing market conditions. For accurate pricing information, it is recommended to contact Showa Denko directly or consult with authorized distributors or resellers.
What is a Showa Denko MCL-E-700G package substrate base material?
The base material used in the Showa Denko MCL-E-700G package substrate is typically an advanced composite material specifically engineered for high-performance semiconductor packaging applications. While the exact composition and formulation may not be publicly disclosed by Showa Denko, it likely consists of a combination of materials chosen for their thermal conductivity, electrical insulation, mechanical strength, and compatibility with semiconductor manufacturing processes.
Common base materials for package substrates include:
- Ceramics: Advanced ceramic materials such as alumina (Al2O3) or aluminum nitride (AlN) are widely used for their excellent thermal conductivity, electrical insulation properties, and mechanical stability. These materials are well-suited for high-power semiconductor devices requiring efficient heat dissipation.
- Organic Substrates:Organic materials such as epoxy resins, polyimides, or glass-reinforced materials are also used as base materials for package substrates. These materials offer advantages such as lower cost, lighter weight, and flexibility in design compared to ceramics. However, they may have lower thermal conductivity and mechanical strength.
- Metal Core Substrates: Metal core substrates, also known as metal-backed or metal-clad substrates, feature a metal layer sandwiched between dielectric layers. The metal layer provides enhanced thermal conductivity, while the dielectric layers offer electrical insulation and mechanical support. Common metals used include aluminum or copper.
Showa Denko likely selects a base material that balances the requirements for thermal management, electrical performance, mechanical integrity, and manufacturability to meet the demanding needs of semiconductor packaging applications. The specific choice of base material may vary depending on factors such as the intended application, performance specifications, and customer preferences.
Which company manufactures Showa Denko MCL-E-700G package substrates?
The Showa Denko MCL-E-700G package substrates are manufactured by Showa Denko, a company based in Japan. However, if our company possesses relevant technology and manufacturing capabilities, we could potentially produce similar substrate products.
Our company has advanced manufacturing equipment and a skilled technical team capable of developing and producing high-performance semiconductor package substrates tailored to meet customer requirements and specifications. Our typical manufacturing process includes the following steps:
- Material Selection: We choose high-performance substrate materials suitable for semiconductor packaging, such as advanced ceramics, organic substrates, or metal core substrates.
- Design and Engineering: Our engineering team designs the substrate layout, circuits, layer structures, etc., according to customer requirements and ensures compliance with thermal management, electrical performance, mechanical strength, etc.
- Manufacturing Process: We employ advanced manufacturing processes such as lithography, etching, chemical deposition, etc., to prepare circuit patterns, metal layers, insulating layers, etc., on the substrate.
- Quality Control: We strictly adhere to quality control procedures to ensure that each substrate meets customer specifications and industry standards. Various tests and inspections, such as electrical performance testing, reliability testing, visual inspection, etc., are conducted to ensure product quality and reliability.
- Customization Services: We offer customized services to tailor substrate specifications, dimensions, materials, etc., to meet the requirements of different application scenarios.
Through our manufacturing capabilities and expertise, we can produce high-quality, high-performance semiconductor package substrates to provide customers with reliable solutions and excellent service.
What are the 7 qualities of good customer service?
Good customer service is characterized by several key qualities that contribute to positive interactions and lasting relationships with customers. Seven essential qualities include:
- Responsiveness: Good customer service involves promptly addressing customer inquiries, concerns, and requests. Being responsive demonstrates attentiveness to customer needs and a commitment to providing timely assistance.
- Empathy: Empathy involves understanding and acknowledging the emotions and perspectives of customers. It entails actively listening to their concerns, showing understanding, and demonstrating genuine care and concern for their well-being.
- Clear Communication: Effective communication is crucial for delivering excellent customer service. Clear and concise communication helps customers understand information, solutions, and next steps, reducing confusion and frustration.
- Product Knowledge: Customer service representatives should possess comprehensive knowledge about the products or services they support. This enables them to provide accurate information, address customer inquiries effectively, and offer relevant recommendations or solutions.
- Professionalism:Professionalism encompasses behaviors such as politeness, respectfulness, and maintaining a positive attitude when interacting with customers. Demonstrating professionalism fosters trust and confidence in the company’s brand and services.
- Problem-Solving Skills: Good customer service involves the ability to identify and resolve customer issues efficiently and effectively. Customer service representatives should be proactive in finding solutions, troubleshooting problems, and ensuring customer satisfaction.
- Follow-Up and Follow-Through: After addressing a customer’s concerns or resolving an issue, good customer service involves following up to ensure satisfaction and checking if further assistance is needed. Additionally, following through on commitments, such as promised actions or resolutions, reinforces reliability and trustworthiness.
By embodying these qualities, organizations can deliver exceptional customer service experiences that foster customer loyalty, retention, and positive word-of-mouth recommendations.
FAQs
What is the Showa Denko MCL-E-700G package substrate?
The Showa Denko MCL-E-700G package substrate is a high-performance substrate used in semiconductor packaging. It provides electrical connections and thermal management for semiconductor chips in electronic devices.
What are the key features of the MCL-E-700G substrate?
The MCL-E-700G substrate features high thermal conductivity, low coefficient of thermal expansion (CTE), excellent electrical insulation properties, and compatibility with various assembly processes such as flip-chip and wire bonding.
What applications are suitable for the MCL-E-700G package substrate?
The MCL-E-700G substrate is suitable for a wide range of applications including smartphones, computers, automotive electronics, consumer electronics, and industrial equipment.
What are the benefits of using the MCL-E-700G substrate?
The benefits include improved thermal management, enhanced electrical performance, reliability, durability, and compatibility with advanced semiconductor packaging technologies.
Is the MCL-E-700G substrate customizable?
Showa Denko may offer customization options based on specific customer requirements such as substrate dimensions, materials, and features.
What is the manufacturing process of the MCL-E-700G package substrate?
The manufacturing process involves several steps including substrate material preparation, circuit pattern formation, metal deposition, dielectric layer formation, via formation, surface finish, and quality control testing.
Where can I purchase MCL-E-700G package substrates?
MCL-E-700G package substrates are typically available through authorized distributors or directly from Showa Denko. Interested customers can inquire about purchasing options through the company’s official channels.
What are the reliability and quality standards of the MCL-E-700G substrate?
Showa Denko likely adheres to stringent reliability and quality standards to ensure the consistent performance and durability of the MCL-E-700G substrate. These may include industry regulations and internal quality control measures.