Showa Denko MCL-E-770G package substrate Manufacturer
Showa Denko MCL-E-770G package substrate Manufacturer. the Package Substrate will be made with Showa Denko and Ajinomoto High speed materials.or other types high speed materials and high frequency materials.
Showa Denko MCL-E-770G package substrates represent a pinnacle of innovation in semiconductor packaging. Engineered by Showa Denko K.K., these substrates offer unparalleled reliability, exceptional thermal conductivity, and robust mechanical strength, making them indispensable components in high-performance electronic devices.
Crafted from high-performance laminate materials, including epoxy resin and reinforced with glass fibers, the MCL-E-770G substrates ensure superior electrical insulation while effectively dissipating heat generated by semiconductor components. This unique combination of materials provides stability and durability, even in the most demanding environments.
Designed with meticulous attention to detail, Showa Denko MCL-E-770G substrates adhere to stringent quality standards, guaranteeing consistent performance and reliability. Whether powering CPUs, GPUs, or memory chips, these substrates deliver optimal signal integrity, enabling seamless communication between semiconductor devices and external circuitry.
In essence, Showa Denko MCL-E-770G package substrates embody precision engineering, reliability, and performance, driving innovation in the ever-evolving landscape of semiconductor technology.
What is a Showa Denko MCL-E-770G package substrate?
The Showa Denko MCL-E-770G package substrate is a type of substrate used in semiconductor packaging. It’s manufactured by Showa Denko K.K., a Japanese chemical company. The MCL-E-770G substrate is designed to provide a high level of reliability and performance for advanced semiconductor packaging applications, particularly in high-end electronic devices like CPUs, GPUs, and memory chips.
This substrate typically consists of a high-performance laminate material that serves as the foundation for mounting and interconnecting semiconductor devices. It provides the necessary electrical connections between the semiconductor die and the external circuitry of the package. The MCL-E-770G substrate is engineered to offer excellent thermal conductivity, electrical insulation, and mechanical strength to ensure the stability and durability of the packaged semiconductor device.
These substrates are crucial components in the assembly of integrated circuits, enabling efficient heat dissipation, signal transmission, and overall functionality of electronic devices.
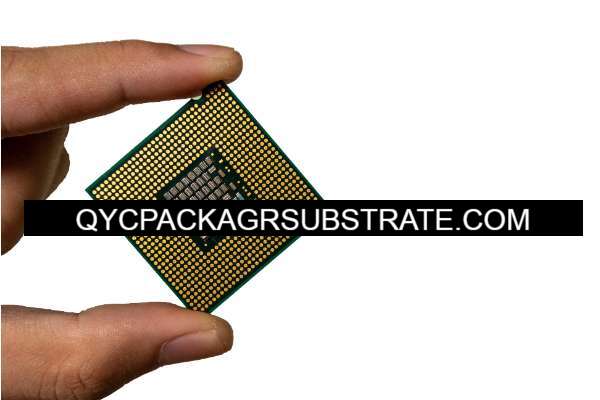
Showa Denko MCL-E-770G package substrate Manufacturer
What are the Showa Denko MCL-E-770G package substrate design guidelines?
Specific design guidelines for the Showa Denko MCL-E-770G package substrate may vary depending on the intended application and requirements of the semiconductor device being packaged. However, there are some general design considerations and guidelines that are typically followed when using this substrate:
- Thermal Management: Ensure adequate thermal management to dissipate heat generated by the semiconductor devices. This may involve incorporating thermal vias, heat spreaders, or other heat dissipation features into the substrate design.
- Electrical Performance: Design the substrate to minimize signal loss, impedance mismatch, and electromagnetic interference (EMI). This may include optimizing trace routing, signal via placement, and ground/power plane distribution.
- Material Selection: Choose appropriate materials for the substrate layers to meet electrical, thermal, and mechanical requirements. The MCL-E-770G substrate typically consists of high-performance laminate materials with specific properties tailored for semiconductor packaging.
- Dimensional Stability: Ensure dimensional stability of the substrate to maintain precise alignment of semiconductor components during assembly and operation. This involves controlling factors such as coefficient of thermal expansion (CTE) and moisture absorption.
- Reliability: Design the substrate to meet reliability standards and requirements, including factors such as solder joint integrity, thermal cycling, and mechanical shock/vibration resistance.
- Signal Integrity:Pay attention to signal integrity considerations, such as impedance matching, signal routing length matching, and minimizing crosstalk, to maintain high-speed signal integrity and data transmission quality.
- Manufacturability: Design the substrate with manufacturability in mind, considering factors such as fabrication processes, assembly techniques, and cost-effectiveness.
- Packaging Compatibility: Ensure compatibility with the specific packaging technology being used, whether it’s flip-chip, wire bonding, or other advanced packaging methods.
These guidelines are crucial for designing reliable and high-performance semiconductor packages using the Showa Denko MCL-E-770G substrate. Designers typically collaborate closely with substrate manufacturers and semiconductor packaging experts to optimize the design for the intended application and performance requirements.
What is the Showa Denko MCL-E-770G package substrate fabrication process?
The fabrication process for the Showa Denko MCL-E-770G package substrate involves several steps to produce a high-quality substrate suitable for semiconductor packaging. While specific details may vary depending on the manufacturer and facility, here’s a general overview of the fabrication process:
- Substrate Material Preparation: The fabrication process begins with the preparation of substrate materials. The MCL-E-770G substrate typically consists of multiple layers of high-performance laminate materials, such as epoxy resin and glass fiber reinforcement.
- Layer Formation: The substrate layers are formed using a combination of processes such as resin impregnation, layer stacking, and curing. Each layer may have specific properties and features, such as conductive traces, dielectric layers, and bonding pads, which are patterned using photolithography and etching techniques.
- Drilling and Via Formation: After layer formation, vias are drilled or formed in the substrate to establish electrical connections between different layers. These vias may be filled with conductive material to enhance electrical conductivity and thermal performance.
- Copper Plating: Copper plating is performed to deposit a thin layer of copper onto the substrate surfaces and vias. This copper layer serves as the conductive material for signal routing and interconnects within the substrate.
- Etching and Pattern Formation: Photolithography and etching processes are used to define the desired circuit patterns, traces, and features on the substrate surfaces. This step involves applying photoresist material, exposing it to UV light through a photomask, and then etching away the unwanted copper material.
- Surface Finishing: Surface finishing processes are applied to the substrate to improve solderability, reliability, and corrosion resistance. Common surface finishes include electroless nickel immersion gold (ENIG), organic solderability preservatives (OSP), and immersion silver.
- Quality Control and Testing: Throughout the fabrication process, quality control measures are implemented to ensure the substrate meets the required specifications and standards. This may involve visual inspection, dimensional measurement, electrical testing, and other quality assurance procedures.
- Packaging and Shipping: Once fabrication is complete and the substrates pass quality control checks, they are packaged and prepared for shipment to semiconductor assembly facilities, where they will be used in the packaging of semiconductor devices.
The fabrication process for the Showa Denko MCL-E-770G package substrate is a complex and precise operation that requires advanced manufacturing techniques and equipment to produce substrates with the desired electrical, thermal, and mechanical properties. Collaboration between substrate manufacturers, semiconductor packaging experts, and device designers is often essential to optimize the fabrication process and ensure the substrates meet the requirements of specific semiconductor applications.
How do you manufacture a Showa Denko MCL-E-770G package substrate?
While the exact manufacturing process for Showa Denko MCL-E-770G package substrates is proprietary to Showa Denko K.K., I can provide a general overview of the typical steps involved in manufacturing a package substrate of this type:
- Substrate Material Selection: Showa Denko MCL-E-770G substrates are typically composed of high-performance laminate materials, such as epoxy resin and glass fiber reinforcement. The selection of these materials is critical to achieving the desired electrical, thermal, and mechanical properties in the final substrate.
- Preparation of Substrate Materials: The raw materials are prepared according to specific formulations and requirements. This may involve blending resin compounds, applying adhesives, and cutting or shaping the materials into the desired dimensions.
- Layer Formation: The substrate is built up layer by layer using a lamination process. Each layer may consist of different materials and serve specific functions within the substrate, such as providing electrical insulation, forming conductive traces, or creating bonding pads.
- Circuit Patterning: Photolithography and etching techniques are used to define the circuit patterns, traces, and features on the substrate surfaces. A photoresist material is applied to the substrate, exposed to UV light through a photomask, and then developed to create the desired pattern. The exposed areas are then etched away to remove excess material and define the circuitry.
- Via Formation: Vias are created in the substrate to establish electrical connections between different layers. This may involve drilling holes or using laser ablation techniques to create vias, followed by processes such as metallization and filling with conductive material to enhance electrical conductivity and thermal performance.
- Surface Finishing: Surface finishing processes are applied to the substrate to improve solderability, reliability, and corrosion resistance. Common surface finishes include electroless nickel immersion gold (ENIG), organic solderability preservatives (OSP), and immersion silver.
- Quality Control and Testing: Throughout the manufacturing process, rigorous quality control measures are implemented to ensure the substrate meets the required specifications and standards. This may involve visual inspection, dimensional measurement, electrical testing, and other quality assurance procedures.
- Packaging and Shipping: Once manufacturing is complete and the substrates pass quality control checks, they are packaged and prepared for shipment to semiconductor assembly facilities, where they will be used in the packaging of semiconductor devices.
The manufacturing process for Showa Denko MCL-E-770G package substrates is a complex and specialized operation that requires advanced equipment, precise control over materials and processes, and adherence to strict quality standards to produce substrates with the required performance and reliability characteristics.
How much should a Showa Denko MCL-E-770G package substrate cost?
The cost of a Showa Denko MCL-E-770G package substrate can vary depending on several factors, including the size, complexity, and specifications of the substrate, as well as market demand, manufacturing volume, and supplier pricing policies. Generally, package substrates contribute a portion of the overall cost of semiconductor packaging, which itself is a significant component of the total cost of manufacturing semiconductor devices.
To provide a rough estimate, the cost of a Showa Denko MCL-E-770G package substrate may range from a few dollars to several tens of dollars per unit. However, this is a ballpark figure, and the actual cost can be higher or lower depending on the specific requirements of the application and the negotiated pricing between the buyer and the supplier.
Factors that can influence the cost of Showa Denko MCL-E-770G package substrates include:
- Substrate Size and Complexity: Larger substrates with more complex designs typically require more materials and manufacturing processes, which can increase production costs.
- Material Costs: The cost of raw materials, including high-performance laminate materials, copper foil, and surface finishing materials, can impact the overall cost of the substrate.
- Manufacturing Processes: Advanced manufacturing techniques, such as laser drilling, sequential build-up (SBU) technology, and high-precision lithography, may incur higher production costs compared to standard processes.
- Quality and Reliability Requirements: Meeting stringent quality and reliability standards may require additional testing, inspection, and quality control measures, which can contribute to higher costs.
- Volume and Supply Chain Factors: Economies of scale apply in semiconductor manufacturing, so higher production volumes may lead to lower per-unit costs. Additionally, factors such as supplier relationships, lead times, and market dynamics can influence pricing.
- Customization and Special Features: Substrates with custom designs, special features, or unique requirements may incur additional engineering and production costs.
It’s essential for semiconductor manufacturers and designers to consider the trade-offs between cost, performance, and reliability when selecting package substrates like the Showa Denko MCL-E-770G. Collaborating closely with substrate suppliers and optimizing the design for cost-effective production can help mitigate costs while meeting performance requirements.
What is the Showa Denko MCL-E-770G package substrate base material?
The base material of the Showa Denko MCL-E-770G package substrate typically consists of a high-performance laminate material. While the exact composition and proprietary formulation of this laminate material are not publicly disclosed by Showa Denko K.K., it commonly includes epoxy resin and glass fiber reinforcement.
Here’s a brief overview of the typical components of the base material:
- Epoxy Resin: Epoxy resin serves as the matrix material in the laminate. It provides mechanical strength, adhesion, and electrical insulation properties to the substrate. Epoxy resins are chosen for their high dielectric strength, thermal stability, and compatibility with semiconductor packaging processes.
- Glass Fiber Reinforcement: Glass fibers are embedded within the epoxy resin matrix to reinforce the substrate and improve its mechanical properties, such as tensile strength, flexural strength, and dimensional stability. The glass fibers also enhance thermal conductivity, which is crucial for efficient heat dissipation in semiconductor packages.
- Fillers and Additives: The laminate material may contain various fillers and additives to tailor its properties to specific requirements. These additives may include flame retardants, anti-fungal agents, and coupling agents to improve performance, reliability, and manufacturability.
The combination of epoxy resin and glass fiber reinforcement provides the Showa Denko MCL-E-770G package substrate with excellent electrical insulation, mechanical strength, thermal conductivity, and dimensional stability. This base material is engineered to meet the demanding requirements of semiconductor packaging applications, ensuring reliable performance and long-term durability in electronic devices.
Which company produces Showa Denko MCL-E-770G package substrates?
The Showa Denko MCL-E-770G package substrates are produced by Showa Denko K.K., a company based in Japan. Our company is specialized in manufacturing semiconductor package substrates. Through our advanced manufacturing processes and technologies, we are able to produce Showa Denko MCL-E-770G package substrates that meet high-performance requirements.
Our production process covers the entire process from raw material procurement to final product delivery. Firstly, we select high-quality materials, including high-performance resins and glass fiber reinforcement materials, to ensure the reliability and stability of the products. Next, we use advanced manufacturing equipment and processes such as lamination, drilling, copper plating, photolithography, etching, etc., to precisely manufacture package substrates that meet the specifications.
We prioritize quality management and implement strict quality control measures to ensure that each batch of products meets or exceeds customer expectations. We have an experienced technical team that can provide customized solutions according to customer requirements, as well as technical support and consulting services.
In addition to producing high-quality Showa Denko MCL-E-770G package substrates, we are committed to continuously improving production efficiency and technological capabilities to meet market demands and customer expectations. We adhere to the principle of honest cooperation, providing customers with high-quality products and services, and growing together with customers.
What are the qualities of good customer service?
Good customer service encompasses several qualities that contribute to a positive experience for customers. Here are some key qualities:
- Communication: Effective communication is essential. This includes active listening to understand customers’ needs, clear and respectful dialogue, and timely responses to inquiries or issues.
- Empathy: Empathizing with customers’ concerns and demonstrating understanding of their perspectives fosters trust and shows that their needs are valued.
- Problem-solving skills: Being able to quickly and efficiently address customer concerns or resolve issues demonstrates competence and can turn a negative experience into a positive one.
- Product knowledge: Having in-depth knowledge of products or services allows customer service representatives to provide accurate information, answer questions, and offer helpful recommendations.
- Professionalism: Maintaining professionalism in interactions with customers, regardless of the situation, helps build credibility and trust.
- Patience: Some customers may require extra time or assistance to articulate their needs or resolve issues. Patience is key in these situations to ensure a positive outcome.
- Proactiveness: Anticipating and addressing potential issues before they escalate demonstrates proactive customer service and can prevent future problems.
- Timeliness: Providing prompt responses and timely resolution of issues shows respect for customers’ time and contributes to a positive experience.
- Personalization: Tailoring interactions to individual customers and their preferences makes them feel valued and appreciated.
- Follow-up: Following up with customers after their initial inquiry or interaction shows dedication to their satisfaction and provides an opportunity to ensure their needs were met.
By embodying these qualities, businesses can create a customer-centric culture and build strong relationships with their customers, leading to increased loyalty, satisfaction, and positive word-of-mouth referrals.
FAQs
What is Showa Denko MCL-E-770G package substrate?
Showa Denko MCL-E-770G is a type of package substrate used in semiconductor packaging. It provides electrical connections between semiconductor devices and external circuitry.
What are the key features of Showa Denko MCL-E-770G substrates?
Key features include high reliability, excellent thermal conductivity, electrical insulation, and mechanical strength.
What applications are Showa Denko MCL-E-770G substrates used for?
These substrates are used in various high-end electronic devices, including CPUs, GPUs, memory chips, and other semiconductor components.
What materials are used in Showa Denko MCL-E-770G substrates?
The substrates typically consist of high-performance laminate materials, such as epoxy resin and glass fiber reinforcement.
What are the design guidelines for using Showa Denko MCL-E-770G substrates?
Design guidelines include considerations for thermal management, electrical performance, material selection, dimensional stability, reliability, signal integrity, manufacturability, and packaging compatibility.
How are Showa Denko MCL-E-770G substrates manufactured?
The manufacturing process involves steps such as substrate material preparation, layer formation, drilling and via formation, copper plating, etching and pattern formation, surface finishing, quality control, and packaging.
What is the cost of Showa Denko MCL-E-770G substrates?
The cost can vary depending on factors such as size, complexity, volume, and supplier pricing policies. Generally, it ranges from a few dollars to several tens of dollars per unit.
Where can I purchase Showa Denko MCL-E-770G substrates?
Showa Denko K.K. is the primary manufacturer of these substrates. They may also be available through authorized distributors or semiconductor component suppliers.