Substrate Packaging Manufacturer
What is Substrate Packaging?
Substrate Packaging Manufacturer and package substrate manufacturer. We use advanced Msap and Sap technology, High multilayer interconnection substrates from 4 to 18 layers,
Substrate packaging typically refers to the process of encapsulating or packaging semiconductor substrates, also known as chips or dies, for use in electronic devices. This packaging process is crucial in protecting the semiconductor chip from environmental factors such as moisture, dust, and mechanical stresses, as well as providing electrical connections to the external circuitry.
Substrate packaging involves several steps, including die attach, wire bonding or flip-chip bonding, encapsulation with a protective material (such as epoxy or molding compound), and sometimes additional processes like leadframe or substrate fabrication.
The choice of packaging technology depends on various factors such as the application, performance requirements, cost considerations, and the size constraints of the electronic device. Common types of substrate packaging include dual in-line packages (DIPs), quad flat packages (QFPs), ball grid arrays (BGAs), chip-scale packages (CSPs), and more advanced packages like wafer-level packaging (WLP) and fan-out wafer-level packaging (FO-WLP).
Effective substrate packaging is essential for ensuring the reliability, durability, and performance of electronic devices across a wide range of applications, from consumer electronics to industrial and automotive sectors.
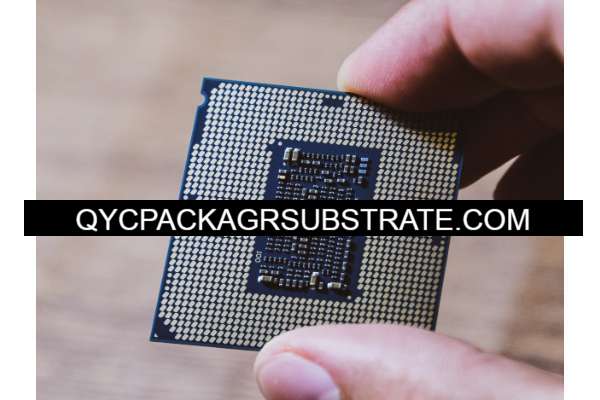
Substrate Packaging Manufacturer
What are the functions of Substrate Packaging?
The functions of substrate packaging include:
Protection: Substrate packaging provides physical protection for semiconductor chips, preventing damage from environmental factors such as moisture, dust, chemicals, and mechanical stress.
Electrical connection: Packaging facilitates electrical connections, allowing semiconductor chips to communicate and interact with external circuits or other devices.
Thermal management: Some packaging technologies also assist in managing the heat generated by semiconductor chips, ensuring that the chips operate within a safe temperature range.
Size and density control: Substrate packaging helps control the size and density of devices, making them more suitable for various applications, such as small electronic devices or high-density integrated circuits.
Reliability: Effective substrate packaging can improve device reliability, extend its lifespan, and reduce the risk of failure due to changes in external environments or operating conditions.
In summary, substrate packaging plays a crucial role in protecting, connecting, managing heat, controlling size, and ensuring reliability for semiconductor chips, making it an indispensable part of modern electronic device manufacturing.
What are the different types of Substrate Packaging?
There are several different types of substrate packaging, each with its own characteristics, advantages, and applications. Some common types include:
Dual in-line packages (DIPs): These are among the oldest and simplest forms of packaging, featuring two rows of parallel pins along the edges of a rectangular plastic or ceramic package.
Quad flat packages (QFPs): QFPs are similar to DIPs but have pins arranged in a grid pattern around the edges of the package, providing more pins in a smaller footprint.
Ball grid arrays (BGAs): BGAs replace traditional pins with solder balls arranged in a grid pattern on the underside of the package, offering better electrical performance, thermal management, and mechanical strength.
Chip-scale packages (CSPs): CSPs are compact packages that closely match the size of the semiconductor chip itself, minimizing the footprint and enabling high-density integration in portable and miniaturized devices.
Wafer-level packaging (WLP): WLP involves packaging individual semiconductor dies directly on the wafer before dicing, eliminating the need for separate packaging processes and reducing costs.
Fan-out wafer-level packaging (FO-WLP): FO-WLP is an advanced form of WLP that allows for additional components, such as passive devices or sensors, to be integrated into the package substrate, offering increased functionality and performance.
System-in-package (SiP): SiP involves integrating multiple semiconductor chips, passive components, and other elements into a single package, enabling highly integrated and customized solutions for specific applications.
These are just a few examples of substrate packaging types, and there are many variations and specialized forms tailored to different requirements and technologies.
What is the relationship between Substrate Packaging and IC packaging?
Substrate packaging and IC (integrated circuit) packaging are closely related but refer to slightly different aspects of the packaging process in semiconductor manufacturing.
Substrate packaging typically refers to the packaging of individual semiconductor dies or chips before they are integrated into a larger electronic system. It involves encapsulating the chip, providing electrical connections, and sometimes integrating passive components onto the substrate.
IC packaging, on the other hand, encompasses the packaging of complete integrated circuits, which may include multiple semiconductor dies, passive components, and other elements, all enclosed within a single package. IC packaging includes not only the packaging of individual dies (substrate packaging) but also the assembly and integration of multiple dies and components into a single package.
In essence, substrate packaging is a subset of IC packaging, focusing specifically on the packaging of individual semiconductor chips or dies. IC packaging, on the other hand, encompasses a broader range of packaging technologies and processes involved in creating fully functional integrated circuits ready for use in electronic devices.
How does Substrate Packaging differ from PCB?
Substrate packaging and PCB (printed circuit board) are both essential components in electronic systems, but they serve different functions and have distinct characteristics:
Function:
Substrate packaging is primarily concerned with encapsulating and providing electrical connections for individual semiconductor chips or dies. It protects the chip from environmental factors and facilitates its integration into larger electronic systems.
PCBs, on the other hand, serve as platforms for mounting and interconnecting various electronic components, including semiconductor chips, passive components, and connectors. They provide the electrical pathways for signals to flow between components and support the overall functionality of the electronic system.
Components:
Substrate packaging typically involves packaging individual semiconductor chips, which may include active components such as transistors, diodes, or integrated circuits, as well as passive components like resistors and capacitors.
PCBs consist of layers of substrate material (such as fiberglass or epoxy resin) with conductive traces printed or etched onto them. They can accommodate various electronic components, including integrated circuits, resistors, capacitors, and connectors.
Integration:
Substrate packaging is a more specialized and focused process, primarily concerned with the packaging of individual semiconductor chips or dies before their integration into larger electronic systems.
PCBs facilitate the integration of multiple electronic components into a single platform, providing the physical and electrical connections needed to create functional electronic systems.
In summary, substrate packaging is specific to the packaging of individual semiconductor chips, providing protection and electrical connections, while PCBs serve as the backbone for integrating various electronic components into complete electronic systems.
What are the structure and production technology of Substrate Packaging?
The structure and production technology of substrate packaging can vary depending on the specific type of packaging and the requirements of the semiconductor device. However, here is a general overview of the structure and production technology commonly used in substrate packaging:
Structure:
Semiconductor Chip or Die: The core component of substrate packaging is the semiconductor chip or die, which contains the active electronic components, such as transistors, diodes, and integrated circuits.
Substrate: The substrate serves as the base or foundation for mounting the semiconductor chip and providing electrical connections. Substrate materials commonly used include ceramics, silicon, or specialized organic materials.
Electrical Interconnects: Electrical interconnects, such as wire bonds or solder bumps, are used to establish electrical connections between the semiconductor chip and the substrate. These interconnects provide the pathways for electrical signals to pass between the chip and the external circuitry.
Encapsulation: Encapsulation materials, such as epoxy or molding compounds, are used to encapsulate and protect the semiconductor chip and interconnects from environmental factors, mechanical stresses, and moisture. Encapsulation also provides additional structural support to the substrate package.
Production Technology:
Die Attach: The semiconductor chip is mounted onto the substrate using a process known as die attach. This process typically involves applying a conductive adhesive or solder paste to bond the chip to the substrate.
Wire Bonding or Flip-Chip Bonding: Electrical connections between the semiconductor chip and the substrate are established using wire bonding or flip-chip bonding techniques. Wire bonding involves using fine wires to connect the chip to the substrate, while flip-chip bonding involves directly bonding solder bumps on the chip to corresponding pads on the substrate.
Encapsulation: Once the semiconductor chip is mounted and electrically connected to the substrate, it is encapsulated with a protective material, such as epoxy or molding compound. This encapsulation process helps to protect the chip from environmental factors and provides additional structural support to the substrate package.
Packaging Process: After encapsulation, the substrate package undergoes various packaging processes, such as curing, trimming, and testing, to ensure the integrity and reliability of the packaged semiconductor device.
Overall, substrate packaging involves a series of precise manufacturing processes to assemble and encapsulate semiconductor chips onto substrates, forming functional and reliable packaged semiconductor devices.
Frequently Asked Questions (FAQs)
What is substrate packaging?
Substrate packaging refers to the process of encapsulating semiconductor chips or dies onto substrates, providing electrical connections and protection for the chips.
What are the types of substrate packaging?
Common types of substrate packaging include dual in-line packages (DIPs), quad flat packages (QFPs), ball grid arrays (BGAs), chip-scale packages (CSPs), wafer-level packaging (WLP), and fan-out wafer-level packaging (FO-WLP).
What are the functions of substrate packaging?
The functions of substrate packaging include protection of semiconductor chips, electrical connection establishment, thermal management, size and density control, and reliability enhancement.
How does substrate packaging differ from PCB?
Substrate packaging focuses on encapsulating and providing electrical connections for individual semiconductor chips, while PCBs serve as platforms for mounting and interconnecting various electronic components within a complete electronic system.
What is the production technology of substrate packaging?
Production technology for substrate packaging involves processes such as die attach, wire bonding or flip-chip bonding, encapsulation with protective materials, and various packaging processes like curing, trimming, and testing.
Conclusion
In conclusion, substrate packaging plays a crucial role in the semiconductor industry by encapsulating semiconductor chips onto substrates, providing electrical connections, and protecting the chips from environmental factors and mechanical stresses. Common types of substrate packaging include DIPs, QFPs, BGAs, CSPs, WLP, and FO-WLP, each offering unique advantages and applications.
The functions of substrate packaging include protection, electrical connection establishment, thermal management, size and density control, and reliability enhancement. Substrate packaging differs from PCBs, which serve as platforms for mounting and interconnecting various electronic components within complete electronic systems.
Production technology for substrate packaging involves precise processes such as die attach, wire bonding or flip-chip bonding, encapsulation with protective materials, and various packaging processes like curing, trimming, and testing.
Overall, substrate packaging is essential for the manufacture of reliable and functional semiconductor devices used in a wide range of electronic applications. It ensures the integrity, performance, and longevity of semiconductor chips within electronic systems.