Mini Ceramics PCB manufacturing
Mini Ceramics PCB manufacturing, Small size Ceramics Mini PCBs supplier. Our company has made many types Ceramics PCBs and Ceramics package substrates from 1 layer to 20 layers. extra small units size, smallest via holes, extra small gap and trace.
Mini Ceramics PCBs are specialized printed circuit boards (PCBs) manufactured using ceramic materials, such as alumina (Al2O3) or aluminum nitride (AlN), instead of traditional organic substrates. These PCBs offer unique advantages, including high thermal conductivity, excellent electrical insulation, and superior mechanical stability. Mini Ceramics PCBs are designed for miniaturized electronic devices and high-performance applications where space constraints, thermal management, and reliability are critical factors.
The use of ceramic materials in PCB manufacturing allows for improved heat dissipation, making Mini Ceramics PCBs suitable for high-power and high-frequency applications. Additionally, ceramics provide excellent dimensional stability, ensuring reliable performance in harsh operating environments. With their advanced properties, Mini Ceramics PCBs enable designers to create compact and reliable electronic systems while meeting stringent performance requirements.
Overall, Mini Ceramics PCBs represent a specialized solution for applications demanding compact size, high performance, and robust reliability, making them a preferred choice in various industries such as telecommunications, aerospace, medical devices, and consumer electronics.
What is a Mini Ceramics PCB?
Mini Ceramics PCB manufacturing and package substrate manufacturing. We use advanced Msap and Sap technology, High multilayer interconnection substrates from 4 to 18 layers,
A “Mini Ceramics PCB” is likely a term referring to a printed circuit board (PCB) made using ceramic materials and designed for miniaturized electronic devices or applications. Ceramics offer several advantages in PCB manufacturing, such as high thermal conductivity, excellent electrical insulation properties, and good mechanical stability.
Miniaturization in electronics often requires PCBs with smaller form factors to fit within tight spaces. Mini Ceramics PCBs may be used in various applications, including telecommunications, aerospace, medical devices, and consumer electronics, where size, performance, and reliability are crucial factors.
These PCBs can be manufactured using advanced techniques to achieve precise dimensions and intricate circuitry layouts. Additionally, the use of ceramic materials can enhance the performance of electronic components, especially in high-frequency and high-power applications, due to their ability to dissipate heat efficiently.
Overall, Mini Ceramics PCBs represent a specialized type of circuit board tailored for miniaturized electronic systems, offering benefits in terms of size, performance, and reliability.
What are the Mini Ceramics PCB Design Guidelines?
Mini Ceramics PCB design guidelines typically revolve around maximizing the benefits of ceramic materials while ensuring optimal performance and reliability of the electronic system. Here are some general design guidelines:
- Thermal Considerations: Since ceramics offer high thermal conductivity, ensure that heat-generating components are efficiently thermally connected to the ceramic substrate. Proper thermal vias and heat sinks may be necessary to dissipate heat effectively.
- Dielectric Properties: Ceramics provide excellent electrical insulation, but it’s important to consider dielectric properties to minimize signal loss and interference. Maintain appropriate trace widths and spacing to achieve desired impedance matching and signal integrity.
- Mechanical Stability: Ceramic PCBs are known for their mechanical stability, but still, consider mechanical stress during assembly and operation. Avoid placing components or traces near areas prone to mechanical stress, such as mounting holes or board edges.
- Component Placement: Carefully layout components to minimize signal path lengths, reduce electromagnetic interference, and optimize thermal management. Group components according to their functions and connectivity to simplify routing and improve overall performance.
- Via Design: Implement proper via design to ensure electrical connectivity between layers while minimizing signal degradation and impedance mismatches. Use thermal vias to enhance heat dissipation and maintain uniform temperature distribution.
- Environmental Considerations: Ceramic PCBs may be used in harsh environments, so consider factors such as humidity, temperature fluctuations, and chemical exposure during the design phase. Choose appropriate materials and coatings to enhance durability and reliability.
- Manufacturability: Work closely with PCB manufacturers familiar with ceramic substrates to ensure design feasibility and manufacturability. Consider manufacturing constraints such as minimum feature sizes, tolerances, and process capabilities.
- Testing and Validation: Perform thorough testing and validation to ensure the final design meets performance requirements and reliability standards. Consider environmental testing, such as thermal cycling and vibration testing, to assess the PCB’s robustness under various operating conditions.
By following these guidelines, designers can optimize Mini Ceramics PCB layouts for improved performance, reliability, and manufacturability in miniaturized electronic systems.
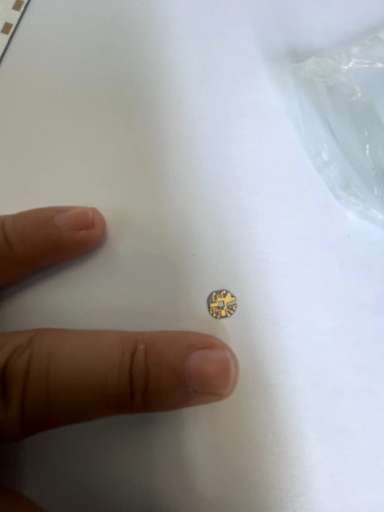
Mini Ceramics PCB
What is the Mini Ceramics PCB Fabrication Process?
The fabrication process for Mini Ceramics PCBs shares similarities with traditional PCB manufacturing processes but involves specialized techniques suited for ceramic materials. Here’s a general overview of the fabrication process:
- Substrate Preparation: The process begins with preparing the ceramic substrate material, typically alumina (Al2O3) or aluminum nitride (AlN). Substrate preparation involves cutting the ceramic material into the desired size and shape using precision machining techniques such as laser cutting or diamond sawing.
- Surface Preparation: After cutting, the substrate surfaces are cleaned and prepared for subsequent processing steps. This may involve treatments such as chemical etching or mechanical polishing to achieve smooth and clean surfaces suitable for circuitry deposition.
- Circuit Patterning: Next, conductive traces and pads are patterned onto the ceramic substrate to form the circuitry. This can be done using various techniques such as screen printing, thick-film deposition, or thin-film deposition methods like sputtering or chemical vapor deposition (CVD).
- Dielectric Layer Deposition: Insulating dielectric layers are deposited over the conductive traces to electrically isolate them and provide additional mechanical support. Dielectric materials such as glass or ceramic pastes may be screen-printed or deposited using thin-film techniques.
- Via Formation: Vias, which are small holes that establish electrical connections between different layers of the PCB, are drilled or laser-ablated through the substrate. These vias are then filled with conductive material using processes like via filling or electroplating.
- Component Attachment: Electronic components such as resistors, capacitors, and integrated circuits are attached to the substrate using soldering techniques or specialized bonding methods suitable for ceramic materials.
- Surface Finish: A surface finish is applied to the PCB to protect the exposed metal surfaces from oxidation and provide solderability. Common surface finishes include gold plating, immersion silver, or tin/lead solder coatings.
- Testing and Inspection: The fabricated PCB undergoes rigorous testing and inspection to ensure proper functionality and adherence to design specifications. This may involve electrical testing, visual inspection, and dimensional measurements.
- Final Assembly: Once the PCB passes quality assurance tests, it may be assembled into the final electronic system, integrating additional components and interconnections as required.
- Quality Control: Throughout the fabrication process, quality control measures are implemented to monitor and maintain the quality and consistency of the Mini Ceramics PCBs, ensuring reliability and performance in end-use applications.
By following these steps, manufacturers can produce high-quality Mini Ceramics PCBs tailored to the specific requirements of miniaturized electronic devices and systems.
How do you manufacture a Mini Ceramics PCB?
Manufacturing a Mini Ceramics PCB involves several steps tailored to the unique properties of ceramic materials. Below is a detailed overview of the manufacturing process:
- Design Phase:
– Design the PCB layout using specialized PCB design software, considering the size constraints and performance requirements of the miniaturized electronic device.
– Optimize the design for thermal management, signal integrity, and mechanical stability, taking advantage of ceramic material properties.
- Substrate Preparation:
– Begin with raw ceramic substrates, typically alumina (Al2O3) or aluminum nitride (AlN).
– Cut the ceramic substrate into the desired size and shape using precision machining techniques such as laser cutting or diamond sawing.
– Clean the substrate surfaces to remove any contaminants and prepare them for subsequent processing steps.
- Circuit Patterning:
– Apply conductive traces and pads onto the ceramic substrate to form the desired circuitry.
– This can be achieved using techniques such as screen printing, thick-film deposition, or thin-film deposition methods like sputtering or chemical vapor deposition (CVD).
– Ensure precise alignment and registration of the circuit patterns on the substrate.
- Dielectric Layer Deposition:
– Deposit insulating dielectric layers over the conductive traces to electrically isolate them and provide mechanical support.
– Dielectric materials such as glass or ceramic pastes may be screen-printed or deposited using thin-film techniques.
- Via Formation:
– Create vias, which are small holes that establish electrical connections between different layers of the PCB, by drilling or laser-ablation.
– Fill the vias with conductive material using processes like via filling or electroplating to establish interconnections between layers.
- Component Attachment:
– Attach electronic components such as resistors, capacitors, and integrated circuits to the substrate using soldering techniques or specialized bonding methods suitable for ceramic materials.
– Ensure proper alignment and soldering integrity to maintain electrical connections.
- Surface Finish:
– Apply a surface finish to protect the exposed metal surfaces from oxidation and provide solderability.
– Common surface finishes include gold plating, immersion silver, or tin/lead solder coatings.
- Testing and Inspection:
– Conduct rigorous testing and inspection of the fabricated PCB to ensure proper functionality and adherence to design specifications.
– This may involve electrical testing, visual inspection, and dimensional measurements to verify quality and reliability.
- Final Assembly:
– Once the PCB passes quality assurance tests, it can be assembled into the final electronic system, integrating additional components and interconnections as required.
- Quality Control:
– Implement quality control measures throughout the manufacturing process to monitor and maintain the quality and consistency of the Mini Ceramics PCBs, ensuring reliability and performance in end-use applications.
By following these steps, manufacturers can produce high-quality Mini Ceramics PCBs optimized for miniaturized electronic devices and systems.
How much should a Mini Ceramics PCB cost?
The cost of a Mini Ceramics PCB can vary widely depending on several factors such as the complexity of the design, the materials used, the manufacturing processes involved, and the quantity ordered. Here are some factors that influence the cost:
- Design Complexity: PCBs with intricate circuit layouts, dense component placement, and advanced features such as high-speed signal routing or embedded components may incur higher design and manufacturing costs.
- Material Selection: The type of ceramic substrate used, such as alumina (Al2O3) or aluminum nitride (AlN), can affect the cost. Additionally, specialized materials with enhanced properties may come at a higher price.
- Manufacturing Processes: The fabrication techniques employed, such as screen printing, thick-film deposition, or thin-film deposition methods, can impact costs. More complex manufacturing processes may require specialized equipment and skilled labor, resulting in higher costs.
- Quantities Ordered: Typically, ordering larger quantities of Mini Ceramics PCBs can reduce the unit cost due to economies of scale. However, prototype or small-batch orders may incur higher costs per unit.
- Additional Services: Additional services such as surface finishing, testing, assembly, and quality assurance may add to the overall cost of the PCBs.
- Supplier and Location: The choice of PCB manufacturer and their location can influence pricing. Manufacturers with advanced capabilities and expertise in ceramic PCBs may charge higher prices.
- Lead Time: Expedited manufacturing or shorter lead times may come at an additional cost.
Given these factors, it’s challenging to provide a precise cost without specific details about the Mini Ceramics PCB requirements. Generally, Mini Ceramics PCBs can range from a few dollars for simple prototypes to hundreds of dollars for complex, high-performance designs in larger quantities. It’s advisable to consult with PCB manufacturers and obtain quotes based on your specific project requirements to determine the cost accurately.
What is the Mini Ceramics PCB base material?
The base material for Mini Ceramics PCBs typically consists of ceramic substrates, which are engineered materials designed to provide excellent thermal, mechanical, and electrical properties suitable for electronic applications. Two common types of ceramic materials used as base substrates for Mini Ceramics PCBs are:
- Alumina (Al2O3): Alumina ceramic substrates offer good thermal conductivity, high mechanical strength, and excellent electrical insulation properties. Alumina is widely used in Mini Ceramics PCBs due to its relatively low cost, high dielectric strength, and compatibility with various manufacturing processes.
- Aluminum Nitride (AlN): Aluminum nitride ceramic substrates provide even higher thermal conductivity compared to alumina, making them ideal for applications requiring efficient heat dissipation. AlN substrates also exhibit excellent electrical insulation properties and can withstand high operating temperatures, making them suitable for high-power and high-frequency electronic devices.
These ceramic materials are chosen for Mini Ceramics PCBs because they can withstand harsh operating conditions, offer good dimensional stability, and provide reliable performance in miniaturized electronic systems. Additionally, they allow for the integration of complex circuitry while maintaining mechanical integrity and thermal management capabilities.
Which company makes Mini Ceramics PCBs?
Many companies specialize in manufacturing Mini Ceramics PCBs, with some having extensive experience and expertise in this field. These companies typically offer customized solutions to meet customers’ demands for small, high-performance PCBs. For example, both domestic and international PCB manufacturers, electronic equipment manufacturers, and high-tech companies may be involved in this field.
Our company is a professional PCB manufacturer with advanced technology and equipment, as well as an experienced team of engineers. We can provide customized Mini Ceramics PCB solutions to meet specific requirements in terms of size, performance, and reliability.
Our manufacturing process and procedures include:
- Advanced CAD/CAM design and layout techniques to ensure PCB designs meet customers’ specifications.
- High-precision cutting and processing of ceramic substrates to ensure precise dimensions and shapes.
- Various process options, including thick-film printing, thin-film deposition, and drilling, to achieve intricate circuit patterns and structures.
- Strict quality control and testing processes to ensure each PCB meets customers’ quality standards and performance requirements.
- Flexible production capabilities to meet customers’ demands for both small and large quantities of Mini Ceramics PCBs.
Our advantages include:
- Professional team: We have an experienced team of engineers who can provide technical support and consulting services.
- High-quality products: We use advanced manufacturing equipment and strict quality control processes to ensure each PCB has excellent quality and reliability.
- Customized services: We can customize Mini Ceramics PCBs according to customers’ specific requirements, meeting their application needs and performance requirements.
- Competitive prices: We offer competitive prices to provide customers with cost-effective solutions.
In summary, our company has extensive experience and expertise in providing high-quality, customized Mini Ceramics PCB solutions to meet the demands of small electronic devices and high-performance applications.
What are the 7 qualities of good customer service?
Good customer service is characterized by several key qualities that contribute to a positive customer experience and foster long-term customer satisfaction. Here are seven qualities of good customer service:
- Responsiveness: A good customer service team responds promptly to customer inquiries, requests, and concerns. They acknowledge customer communication in a timely manner, whether through phone calls, emails, or social media, and strive to provide quick resolutions to issues.
- Empathy: Empathy involves understanding and relating to the customer’s feelings, concerns, and perspectives. Good customer service representatives demonstrate empathy by actively listening to customers, showing compassion for their challenges, and expressing genuine understanding and concern.
- Knowledgeability: A good customer service team possesses in-depth knowledge about the company’s products, services, policies, and procedures. They are well-trained to answer customer questions accurately, provide relevant information, and offer helpful guidance or troubleshooting assistance.
- Professionalism: Professionalism is essential in all customer interactions. Good customer service representatives maintain a courteous and respectful demeanor, communicate clearly and effectively, and conduct themselves with integrity and professionalism at all times.
- Problem-solving Skills: Good customer service involves effectively resolving customer issues and addressing their concerns. Customer service representatives should be skilled problem-solvers, capable of identifying root causes of problems, exploring solutions, and implementing appropriate actions to meet customer needs and expectations.
- Proactiveness: Proactiveness in customer service involves anticipating customer needs and taking proactive measures to address potential issues before they escalate. Good customer service teams actively seek feedback from customers, identify areas for improvement, and implement proactive strategies to enhance the customer experience.
- Consistency: Consistency is key to delivering excellent customer service across all interactions and touchpoints. Good customer service teams strive to maintain consistency in their communication, service delivery, and problem-solving approaches, ensuring that customers receive a consistently high level of service regardless of the channel or representative they interact with.
By embodying these qualities, businesses can build strong relationships with customers, foster loyalty and trust, and differentiate themselves in a competitive marketplace.
FAQs
What are Mini Ceramics PCBs?
Mini Ceramics PCBs are printed circuit boards (PCBs) made using ceramic materials and designed for miniaturized electronic devices or applications. They offer advantages such as high thermal conductivity, excellent electrical insulation, and mechanical stability.
What are the advantages of Mini Ceramics PCBs?
Mini Ceramics PCBs offer several advantages, including high thermal conductivity for efficient heat dissipation, excellent electrical insulation properties, mechanical stability, and compatibility with high-frequency and high-power applications.
What types of ceramic materials are used in Mini Ceramics PCBs?
Common ceramic materials used in Mini Ceramics PCBs include alumina (Al2O3) and aluminum nitride (AlN). These materials provide the necessary thermal, electrical, and mechanical properties required for electronic applications.
What are the applications of Mini Ceramics PCBs?
Mini Ceramics PCBs are used in various applications, including telecommunications, aerospace, medical devices, consumer electronics, and automotive electronics, where size, performance, and reliability are critical factors.
How are Mini Ceramics PCBs manufactured?
The manufacturing process for Mini Ceramics PCBs involves several steps, including substrate preparation, circuit patterning, dielectric layer deposition, via formation, component attachment, surface finishing, testing, and inspection. Specialized techniques tailored to ceramic materials are employed throughout the process.
What factors affect the cost of Mini Ceramics PCBs?
The cost of Mini Ceramics PCBs depends on factors such as the complexity of the design, materials used, manufacturing processes involved, quantity ordered, additional services required, supplier, and lead time.
Where can I find manufacturers of Mini Ceramics PCBs?
Manufacturers of Mini Ceramics PCBs can be found through online directories, industry trade shows, or by contacting PCB manufacturers directly. It’s essential to choose a reputable manufacturer with experience in ceramic PCBs and a track record of quality and reliability.
What are the design considerations for Mini Ceramics PCBs?
Design considerations for Mini Ceramics PCBs include thermal management, dielectric properties, mechanical stability, component placement, via design, environmental considerations, manufacturability, and testing/validation.
How can I ensure the reliability of Mini Ceramics PCBs?
Ensuring the reliability of Mini Ceramics PCBs involves selecting high-quality materials, following best practices in design and manufacturing, conducting thorough testing and inspection, and working with experienced and reputable PCB manufacturers.
Can Mini Ceramics PCBs be customized for specific applications?
Yes, Mini Ceramics PCBs can be customized to meet specific application requirements, including size, performance, thermal management, and environmental considerations. Working closely with PCB manufacturers experienced in ceramic substrates can help achieve customized solutions.