Ultra-small PCS BGA Substrates Manufacturer
Ultra-small PCS BGA Substrates Manufacturer,Ultra-small BGA substrates are cutting-edge packaging solutions for semiconductor devices, renowned for their compact size and high performance. These substrates feature densely packed solder balls, facilitating seamless integration of integrated circuits in space-constrained electronic devices. With advanced materials and precision manufacturing techniques, ultra-small BGA substrates offer superior thermal management, signal integrity, and reliability. Ideal for applications where size matters, such as mobile devices, wearables, and IoT gadgets, these substrates enable the creation of smaller, lighter, and more powerful electronics, driving innovation in the ever-evolving tech landscape.
What are Ultra-small BGA Substrates?
Ultra-small BGA substrates, or ball grid array substrates, are advanced packaging solutions used in semiconductor manufacturing. These substrates provide a platform for mounting and connecting integrated circuits (ICs) within electronic devices. They are characterized by their extremely compact size, making them suitable for applications where space is at a premium, such as in mobile devices, wearables, and IoT (Internet of Things) devices.
These substrates feature a grid of solder balls on their underside, which serve as the connections between the IC and the printed circuit board (PCB) or other components. The ultra-small size of these substrates allows for higher component density on a PCB, enabling manufacturers to pack more functionality into smaller devices.
Key features of ultra-small BGA substrates include high-density interconnects, excellent thermal performance, and reliable electrical connections. They are typically constructed using advanced materials such as organic substrates, ceramics, or silicon, depending on the specific requirements of the application.
In addition to their compact size, ultra-small BGA substrates may incorporate advanced technologies such as flip-chip bonding, microvia drilling, and multilayer construction to further enhance performance and reliability.
Overall, ultra-small BGA substrates play a crucial role in enabling the development of smaller, lighter, and more powerful electronic devices across a wide range of industries. Their compact size, high performance, and reliability make them an essential component in modern electronics manufacturing.
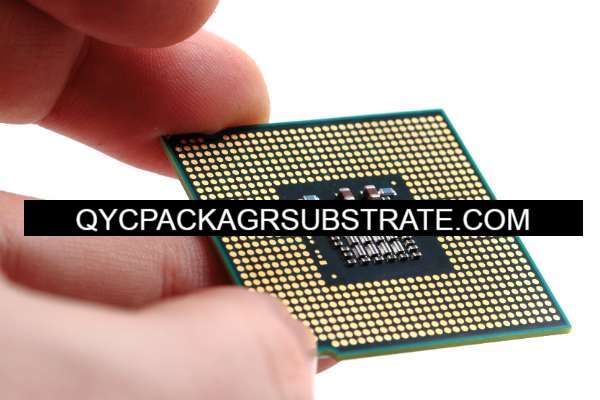
Ultra-small PCS BGA Substrates Manufacturer
What are the Ultra-small BGA Substrates Design Guidelines?
Designing with ultra-small BGA substrates requires careful attention to various guidelines to ensure optimal performance and reliability. Here are some key design guidelines:
- Pad Layout: Ensure that the pad layout on the PCB matches the footprint of the BGA substrate. Pay attention to pad pitch, size, and spacing to ensure proper alignment with the solder balls on the substrate.
- Via Placement: Strategically place vias to provide adequate electrical connections between layers of the PCB and to minimize signal interference. Use microvias for high-density designs to conserve space and improve signal integrity.
- Thermal Management: Incorporate thermal vias and thermal pads to dissipate heat away from the BGA substrate and prevent overheating. Ensure proper airflow and ventilation within the device enclosure to maintain optimal operating temperatures.
- Signal Integrity: Minimize signal skew, reflection, and crosstalk by carefully routing high-speed signals on the PCB. Maintain consistent trace lengths and impedance matching to preserve signal integrity and reduce signal degradation.
- Power Distribution: Design a robust power distribution network to deliver clean and stable power to the BGA substrate and associated components. Use power planes and decoupling capacitors to minimize voltage fluctuations and noise.
- Assembly Considerations: Follow assembly guidelines provided by the substrate manufacturer to ensure proper soldering of the BGA substrate to the PCB. Use appropriate solder paste, stencil design, and reflow profile to achieve reliable solder joints.
- Mechanical Stability: Ensure mechanical stability by securing the BGA substrate to the PCB with proper mounting techniques such as underfill or epoxy encapsulation. Consider mechanical shock and vibration requirements for the intended application.
- Component Placement:Optimize component placement on the PCB to minimize signal path lengths, reduce electromagnetic interference, and facilitate efficient routing of traces. Consider the location of other components and connectors to avoid interference and facilitate assembly.
- Design for Manufacturability:Design the PCB with manufacturability in mind, considering factors such as panelization, fiducial marks, solder mask clearance, and assembly tolerances. Work closely with PCB manufacturers and assembly partners to optimize the design for mass production.
- Testing and Validation: Develop comprehensive testing and validation procedures to verify the performance and reliability of the BGA substrate and the entire electronic system. Conduct electrical testing, thermal analysis, and reliability testing to identify and address any issues early in the design process.
By following these design guidelines, engineers can effectively utilize ultra-small BGA substrates in their designs while ensuring optimal performance, reliability, and manufacturability.
What is the Ultra-small BGA Substrates Fabrication Process?
The fabrication process for ultra-small BGA (Ball Grid Array) substrates involves several key steps to produce the intricate patterns and structures required for mounting and connecting integrated circuits. Here’s an overview of the typical fabrication process:
- Substrate Material Selection: The fabrication process begins with the selection of suitable substrate materials, which may include organic materials such as FR-4, high-performance materials like polyimide or BT resin, or ceramics like alumina or silicon. The choice of material depends on factors such as thermal performance, electrical properties, and cost.
- Substrate Preparation: The selected substrate material undergoes preparation steps such as cleaning, surface treatment, and pre-lamination to ensure optimal adhesion of subsequent layers and to remove any contaminants that could affect the quality of the final product.
- Layer Formation: Multiple layers of conductive and insulating materials are deposited onto the substrate through processes such as sputtering, chemical vapor deposition (CVD), or physical vapor deposition (PVD). These layers form the conductive traces, vias, and insulating layers necessary for routing electrical signals.
- Patterning: Photolithography or other patterning techniques are used to define the desired circuit patterns on each layer of the substrate. A photoresist material is applied to the substrate surface, exposed to ultraviolet (UV) light through a photomask, and developed to selectively remove the photoresist, leaving behind the desired pattern.
- Etching: The exposed areas of the substrate are etched away using wet or dry etching processes, leaving behind the conductive traces and vias defined by the patterned photoresist. Etching may be performed using chemical etchants or plasma etching techniques, depending on the substrate material and desired precision.
- Plating: Electroplating or other metal deposition techniques are used to deposit additional metal layers onto the substrate surface, enhancing conductivity and providing a surface for solder attachment. Plating may also be used to fill vias and create solder bumps or balls for attachment to integrated circuits.
- Solder Mask Application: A solder mask layer is applied to the substrate surface to protect the conductive traces and vias from environmental damage and to define the areas where solder will be applied for component attachment. The solder mask is typically applied using screen printing or inkjet printing techniques.
- Surface Finish: The substrate surface is treated with a surface finish to improve solderability and ensure reliable solder joints during assembly. Common surface finishes include electroless nickel immersion gold (ENIG), electroless nickel electroless palladium immersion gold (ENEPIG), and hot air solder leveling (HASL).
- Testing and Inspection: The fabricated substrates undergo rigorous testing and inspection to ensure they meet quality standards and specifications. Electrical testing, dimensional inspection, and visual inspection are performed to identify any defects or anomalies that may affect performance or reliability.
- Packaging and Delivery: Once the substrates pass inspection, they are packaged and prepared for delivery to customers or assembly partners. Packaging methods may include trays, tape and reel, or other packaging formats suitable for the specific application and handling requirements.
Overall, the fabrication process for ultra-small BGA substrates involves a combination of precision manufacturing techniques, advanced materials, and rigorous quality control measures to produce high-performance substrates for a wide range of electronic applications.
How do you manufacture Ultra-small BGA Substrates?
Manufacturing ultra-small BGA (Ball Grid Array) substrates involves a series of intricate processes to create the complex patterns and structures required for mounting and connecting integrated circuits. Here’s a generalized overview of the manufacturing process:
- Substrate Material Selection: The process begins with selecting the appropriate substrate material based on the desired electrical, thermal, and mechanical properties. Common materials include organic substrates (e.g., FR-4), high-performance materials (e.g., polyimide, BT resin), or ceramics (e.g., alumina, silicon).
- Substrate Preparation: The selected substrate material undergoes preparation steps such as cleaning and surface treatment to ensure optimal adhesion and quality of subsequent layers. Pre-lamination may also be performed to prepare the substrate for layer deposition.
- Layer Deposition: Multiple layers of conductive and insulating materials are deposited onto the substrate using techniques such as sputtering, chemical vapor deposition (CVD), or physical vapor deposition (PVD). These layers form the conductive traces, vias, and insulating layers necessary for routing electrical signals.
- Patterning: Photolithography or other patterning techniques are used to define the desired circuit patterns on each layer of the substrate. A photoresist material is applied to the substrate surface, exposed to UV light through a photomask, and developed to selectively remove the photoresist, leaving behind the desired pattern.
- Etching: The exposed areas of the substrate are etched away using wet or dry etching processes, leaving behind the conductive traces and vias defined by the patterned photoresist. Etching may involve chemical etchants or plasma etching techniques, depending on the substrate material and desired precision.
- Plating: Electroplating or other metal deposition techniques are used to deposit additional metal layers onto the substrate surface, enhancing conductivity and providing a surface for solder attachment. Plating may also be used to fill vias and create solder bumps or balls for attachment to integrated circuits.
- Solder Mask Application: A solder mask layer is applied to the substrate surface to protect the conductive traces and vias from environmental damage and to define the areas where solder will be applied for component attachment. Solder mask application may involve screen printing or inkjet printing techniques.
- Surface Finish: The substrate surface is treated with a surface finish to improve solderability and ensure reliable solder joints during assembly. Common surface finishes include electroless nickel immersion gold (ENIG), electroless nickel electroless palladium immersion gold (ENEPIG), and hot air solder leveling (HASL).
- Testing and Inspection: The manufactured substrates undergo comprehensive testing and inspection to ensure they meet quality standards and specifications. Electrical testing, dimensional inspection, and visual inspection are performed to identify any defects or anomalies that may affect performance or reliability.
- Packaging and Delivery:Once the substrates pass inspection, they are packaged and prepared for delivery to customers or assembly partners. Packaging methods may include trays, tape and reel, or other formats suitable for the specific application and handling requirements.
Throughout the manufacturing process, stringent quality control measures are implemented to ensure the production of high-performance ultra-small BGA substrates suitable for a wide range of electronic applications.
How much should Ultra-small BGA Substrates cost?
The cost of ultra-small BGA substrates can vary widely depending on various factors such as materials used, complexity of design, manufacturing processes, and quantity ordered. Here are some key considerations that can impact the cost:
- Materials: The choice of substrate materials can significantly affect the cost. High-performance materials such as polyimide or ceramic substrates generally command higher prices compared to standard organic substrates like FR-4.
- Design Complexity: Ultra-small BGA substrates with intricate patterns, fine pitch traces, and multiple layers will typically cost more to manufacture due to the increased complexity involved in fabrication.
- Manufacturing Processes: The specific manufacturing techniques and processes used to produce the substrates can influence the cost. For example, advanced processes such as laser drilling, sequential build-up (SBU), or via-in-pad technology may incur additional expenses.
- Volume: Economies of scale apply in manufacturing, meaning that larger production volumes typically result in lower unit costs. Ordering higher quantities of ultra-small BGA substrates can lead to significant cost savings per unit.
- Quality Requirements: Meeting certain quality standards and certifications may add to the cost of production. For applications requiring stringent reliability and performance specifications, additional testing and quality control measures may be necessary, increasing overall costs.
- Additional Features: Incorporating special features such as impedance control, blind vias, buried vias, or specialized surface finishes can add to the cost of the substrates.
- Supplier and Location: The choice of supplier and their location can impact pricing. Suppliers with advanced manufacturing capabilities and efficient supply chains may offer competitive prices.
Given these factors, it’s challenging to provide a precise cost estimate for ultra-small BGA substrates without specific details about the requirements of the project. However, as a rough estimate, ultra-small BGA substrates can range in cost from a few dollars to tens of dollars or more per unit, depending on the factors mentioned above. It’s advisable to consult with substrate manufacturers or suppliers to obtain accurate cost estimates based on the specific requirements of your project.
What is Ultra-small BGA Substrates base material?
Ultra-small BGA (Ball Grid Array) substrates can be manufactured using various base materials depending on the specific requirements of the application. Some common base materials include:
- Organic Substrates (e.g., FR-4): Organic substrates are widely used in electronics manufacturing due to their cost-effectiveness and ease of fabrication. FR-4, a type of epoxy-based laminate, is one of the most commonly used organic substrates for PCBs (Printed Circuit Boards). It provides good electrical insulation and mechanical strength, making it suitable for many applications.
- Polyimide: Polyimide substrates offer excellent thermal stability, flexibility, and chemical resistance, making them suitable for high-temperature and harsh-environment applications. They are often used in flexible PCBs and applications where space constraints or thermal management are critical.
- BT Resin (Bismaleimide Triazine): BT resin substrates offer high thermal performance and reliability, making them suitable for high-speed and high-frequency applications. They provide low dielectric loss and good signal integrity, making them ideal for applications such as telecommunications and networking.
- Ceramics (e.g., Alumina, Silicon): Ceramic substrates offer superior thermal conductivity, mechanical stability, and reliability compared to organic materials. Alumina (aluminum oxide) and silicon are commonly used ceramics in semiconductor packaging due to their excellent thermal properties and compatibility with high-frequency applications.
- Specialized Materials: In some cases, specialized materials such as liquid crystal polymer (LCP) or silicon substrates may be used for ultra-small BGA substrates to meet specific performance requirements, such as high-frequency applications or miniaturized devices.
The choice of base material for ultra-small BGA substrates depends on factors such as thermal management, electrical performance, mechanical stability, cost, and manufacturability. Designers and engineers select the most suitable material based on the requirements of the application and the desired performance characteristics of the substrate.
Which company makes Ultra-small BGA Substrates?
There are many companies producing ultra-small BGA (Ball Grid Array) substrates, including major semiconductor manufacturers such as Intel in the United States, TSMC (Taiwan Semiconductor Manufacturing Company) in Taiwan, and Samsung Electronics in South Korea. In addition, there are also specialized electronics manufacturing companies that offer ultra-small BGA substrates, such as Panasonic in Japan and Schweizer Electronic in Switzerland.
As for our company, we are also capable of manufacturing ultra-small BGA substrates. We possess advanced manufacturing equipment and technology to meet the demand for high-performance, reliable substrates from our customers. Our manufacturing process includes advanced material selection, precise process control, and stringent quality inspection to ensure the production of high-quality products that meet customer requirements.
Our strengths include:
- Customization Capability: We can customize ultra-small BGA substrates according to specific customer requirements, including dimensions, layers, materials, etc., to meet the needs of different applications.
- Professional Team: We have an experienced engineering team and technical personnel who can provide professional technical support and consulting services to help customers optimize designs and solve production issues.
- Quality Assurance: We strictly adhere to ISO quality management systems and employ advanced testing equipment and methods for quality control, ensuring that each ultra-small BGA substrate meets customer requirements and standards.
- Fast Delivery: With efficient production capacity and flexible scheduling, we can deliver customer orders promptly to meet their production needs.
Through our efforts and professional capabilities, we can provide customers with high-quality, reliable ultra-small BGA substrates, helping them succeed in various electronic applications.
What are the 7 qualities of good customer service?
Good customer service is characterized by several key qualities that contribute to positive experiences for customers. Here are seven important qualities:
- Responsiveness: Good customer service involves being prompt and proactive in addressing customer inquiries, concerns, and requests. Responding to customer needs in a timely manner demonstrates attentiveness and a commitment to customer satisfaction.
- Empathy: Empathy is essential for understanding and relating to customers’ feelings, perspectives, and situations. Customer service representatives who demonstrate empathy can effectively connect with customers, validate their experiences, and provide personalized support.
- Clarity: Clear communication is crucial for delivering good customer service. Customer service representatives should communicate information, instructions, and solutions in a concise, easy-to-understand manner, avoiding jargon or technical language that may confuse customers.
- Professionalism: Professionalism entails maintaining a courteous, respectful demeanor and adhering to established standards of conduct when interacting with customers. Professional customer service representatives demonstrate integrity, reliability, and accountability in their actions.
- Problem-solving skills: Effective problem-solving skills are essential for resolving customer issues and addressing challenges that arise. Customer service representatives should be proactive in identifying solutions, taking ownership of problems, and following through until resolution is achieved.
- Adaptability: Good customer service requires adaptability to accommodate diverse customer needs, preferences, and communication styles. Customer service representatives should be flexible and resourceful, adjusting their approach as needed to meet the unique requirements of each customer interaction.
- Consistency: Consistency is key to building trust and credibility with customers. Providing consistently high-quality service across all customer interactions, channels, and touchpoints reinforces the organization’s commitment to excellence and fosters long-term customer loyalty.
By embodying these qualities, organizations can deliver exceptional customer service experiences that leave a positive impression on customers and contribute to overall customer satisfaction and loyalty.
FAQs
What are the advantages of ultra-small BGA substrates?
Ultra-small BGA substrates offer several advantages, including increased component density, improved thermal performance, enhanced signal integrity, and reduced form factor. They enable the development of smaller, lighter, and more powerful electronic devices.
What applications are ultra-small BGA substrates used in?
Ultra-small BGA substrates are used in various electronic applications where space is at a premium, including mobile devices, wearables, IoT (Internet of Things) devices, automotive electronics, medical devices, and consumer electronics.
How are ultra-small BGA substrates manufactured?
The manufacturing process for ultra-small BGA substrates involves several key steps, including substrate material selection, layer formation, patterning, etching, plating, solder mask application, surface finish, testing, and inspection. Advanced materials and precision manufacturing techniques are used to produce high-performance substrates.
What factors should be considered when designing with ultra-small BGA substrates?
Design considerations for ultra-small BGA substrates include pad layout, via placement, thermal management, signal integrity, power distribution, assembly considerations, mechanical stability, component placement, design for manufacturability, and testing and validation.
How much do ultra-small BGA substrates cost?
The cost of ultra-small BGA substrates can vary depending on factors such as materials used, design complexity, manufacturing processes, volume ordered, quality requirements, and additional features. It’s advisable to consult with substrate manufacturers for accurate cost estimates based on specific project requirements.
Which companies manufacture ultra-small BGA substrates?
Several companies manufacture ultra-small BGA substrates, including major semiconductor manufacturers such as Intel, TSMC, and Samsung Electronics, as well as specialized electronics manufacturing companies. Additionally, some companies offer customization services for ultra-small BGA substrates.