Advanced BGA Substrate Manufacturer
Advanced BGA Substrate Manufacturer.High speed and high frequency material packaging substrate Manufacturer. Advanced packaging substrate production process and technology
Advanced BGA Substrate (ABS) is a cutting-edge solution revolutionizing the landscape of integrated circuit packaging. Engineered with precision and innovation, ABS offers unparalleled performance, reliability, and versatility for a wide range of high-performance electronic applications.
At its core, ABS embodies a sophisticated design that incorporates advanced substrate materials, fine-line technology, and high-density interconnects. This intricate construction enables ABS to deliver superior signal integrity, thermal management, and electrical performance compared to traditional BGA substrates.
With ABS, electronic devices can achieve new heights of functionality and efficiency. From mobile devices and computers to automotive electronics and aerospace technologies, ABS empowers manufacturers to push the boundaries of innovation while meeting the demands of modern electronic systems.
In essence, ABS represents the pinnacle of technological advancement in integrated circuit packaging, driving the development of smaller, more powerful, and more reliable electronic devices. With its unparalleled performance and versatility, ABS is poised to shape the future of electronics for years to come.
What is an Advanced BGA Substrate (ABS)?
An Advanced BGA Substrate (ABS) is a highly sophisticated platform used primarily in the packaging of integrated circuits (ICs), especially for high-performance applications. BGA stands for Ball Grid Array, which is a type of surface-mount packaging used for integrated circuits that utilizes tiny balls of solder as connectors between the IC and the printed circuit board (PCB). The “Advanced” in ABS refers to enhancements in the substrate’s design and material properties that accommodate the increasing demands for higher performance, greater functionality, and more compact sizes in modern electronic devices.
ABS typically features finer lines, smaller vias (holes drilled in the substrate for electrical connection), and more layers than standard BGA substrates. These improvements allow for more intricate routing of electrical pathways and support for higher densities of electrical connections. The substrate itself is often made from materials with better electrical properties and thermal stability, such as advanced resin systems or ceramic materials. These materials help manage the thermal and mechanical stresses experienced by electronic components during operation and can contribute to the overall reliability and performance of the device.
Advanced BGA substrates are crucial in applications requiring high-speed signal transmission and high-frequency operation, such as in mobile devices, computers, networking equipment, and in automotive and aerospace technologies. As devices become more powerful and smaller, the role of ABS becomes increasingly significant in enabling these advancements by supporting higher levels of integration and complexity in semiconductor devices.
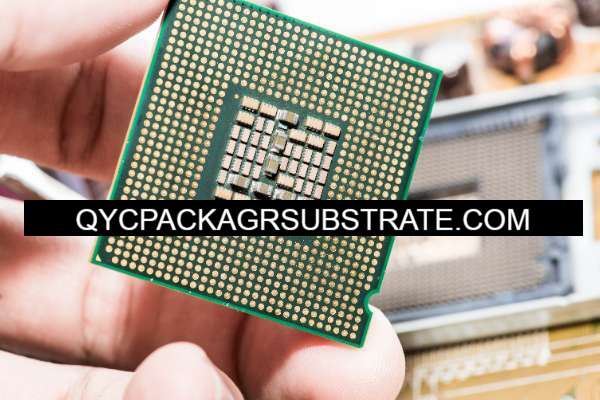
Advanced BGA Substrate Manufacturer
What are the ABS Design Guidelines?
Designing with Advanced BGA Substrates (ABS) involves adhering to specific guidelines to ensure optimal performance and reliability. Here are some common ABS design guidelines:
- Signal Integrity Considerations: Pay attention to signal integrity issues such as impedance matching, signal routing, and minimizing signal reflections. Ensure controlled impedance for high-speed signals to prevent signal degradation and electromagnetic interference (EMI).
- Power Delivery Network (PDN): Design a robust power delivery network with low impedance paths for supplying power to the ICs. Implement decoupling capacitors strategically to minimize voltage noise and fluctuations.
- Thermal Management: Incorporate thermal vias and thermal pads to enhance heat dissipation from the ICs to the PCB. Optimize the layout to distribute heat evenly across the substrate and prevent localized hotspots.
- Package Size and Routing Density: Balance the size of the ABS with the required routing density and signal integrity constraints. Ensure adequate space for routing high-density interconnects while maintaining signal integrity and thermal performance.
- Layer Stackup Design: Design the layer stackup to accommodate signal routing, power distribution, and thermal management requirements. Use multiple layers to reduce signal crosstalk and interference.
- Component Placement: Optimize the placement of components, including ICs, passive components, and connectors, to minimize signal distortion, reduce signal path lengths, and facilitate efficient routing.
- Solder Mask and Silkscreen: Use solder mask openings and silkscreen markings to facilitate accurate soldering and assembly processes. Ensure proper alignment of solder mask openings with BGA pads to prevent solder bridging and short circuits.
- Reliability Considerations: Design for reliability by considering factors such as mechanical stress, thermal cycling, and environmental conditions. Ensure adequate clearance and spacing between components to prevent solder joint fatigue and mechanical failures.
- Manufacturability and Assembly: Design for manufacturability by adhering to standard PCB manufacturing processes and assembly guidelines. Minimize the complexity of the design to streamline the manufacturing and assembly processes.
- Documentation and Design Reviews: Document the design thoroughly, including schematics, layout files, design constraints, and manufacturing specifications. Conduct design reviews with stakeholders to identify and address potential issues early in the design process.
By following these guidelines, designers can ensure the successful integration of ABS into electronic devices, achieving optimal performance, reliability, and manufacturability.
What is the ABS Fabrication Process?
The fabrication process for Advanced BGA Substrates (ABS) involves several steps to create the intricate substrate structures needed for high-performance integrated circuits. Here’s a general overview of the ABS fabrication process:
- Substrate Material Selection: Choose a suitable substrate material based on the application requirements, such as FR-4 (epoxy-based substrate), high-speed laminate, or ceramic material. The choice depends on factors like electrical performance, thermal conductivity, and cost.
- Preparation of Substrate Material: Prepare the substrate material by cutting it into the desired size and shape, typically in the form of a panel or sheet. The substrate material may undergo surface treatment processes to enhance adhesion and facilitate subsequent manufacturing steps.
- Layer Stackup Design: Determine the layer stackup configuration based on the design requirements, including the number of layers, signal routing, power distribution, and thermal management considerations. Each layer may consist of conductive traces, insulating layers, and vias for interconnection.
- Lamination: Bond the layers of substrate material together using heat and pressure in a process known as lamination. This step forms a solid, multi-layered structure with conductive traces and vias embedded within the substrate.
- Drilling and Vias Formation: Drill holes or vias in the substrate material to establish electrical connections between different layers. Advanced drilling techniques, such as laser drilling, may be used to achieve precise hole sizes and positioning.
- Conductor Patterning: Apply a thin layer of conductive material, such as copper, onto the surface of the substrate using processes like sputtering, electroplating, or chemical deposition. The conductive material is patterned to create the desired circuit traces and pads.
- Etching: Use chemical etching or plasma etching to remove excess conductive material and define the circuit traces and features with high precision. Etching removes the unwanted copper while leaving behind the desired conductive patterns on the substrate.
- Surface Finish: Apply a surface finish to protect the exposed copper surfaces from oxidation and facilitate soldering during assembly. Common surface finishes include electroless nickel immersion gold (ENIG), organic solderability preservative (OSP), and immersion silver.
- Solder Mask Application: Apply a solder mask layer over the substrate surface to insulate the conductive traces and define solderable areas for component attachment. The solder mask is typically cured using ultraviolet (UV) light and then selectively removed to expose the solder pads.
- Final Inspection and Testing: Conduct thorough inspection and testing of the fabricated ABS to ensure compliance with design specifications, including dimensional accuracy, electrical continuity, and reliability. Advanced inspection techniques, such as automated optical inspection (AOI) and electrical testing, may be employed to validate the quality of the substrates.
Once the ABS fabrication process is complete, the substrates are ready for assembly with integrated circuits and other electronic components to manufacture high-performance electronic devices.
How do you manufacture an ABS?
Manufacturing an Advanced BGA Substrate (ABS) involves a series of intricate processes aimed at creating a high-performance platform for integrated circuits. Here’s a detailed overview of the ABS manufacturing process:
- Design and Prototyping: The process begins with the design phase, where engineers create a detailed layout of the substrate, considering factors such as signal routing, power distribution, thermal management, and mechanical integrity. Prototyping may involve creating initial samples to validate the design concept.
- Substrate Material Selection: Choose a suitable substrate material based on the application requirements and performance specifications. Common substrate materials include FR-4 (epoxy-based), high-speed laminates, and ceramics. The choice depends on factors such as electrical properties, thermal conductivity, and cost-effectiveness.
- Preparation of Substrate Material: Prepare the substrate material by cutting it into the desired size and shape, typically in the form of panels or sheets. The substrate material may undergo surface treatment processes, such as cleaning and roughening, to enhance adhesion and facilitate subsequent manufacturing steps.
- Layer Stackup Design: Determine the layer stackup configuration based on the design requirements, including the number of layers, signal routing, power distribution, and thermal management considerations. Each layer may consist of conductive traces, insulating layers, and vias for interconnection.
- Lamination: Bond the layers of substrate material together using heat and pressure in a process known as lamination. This step forms a solid, multi-layered structure with conductive traces and vias embedded within the substrate. The lamination process ensures strong adhesion between layers and provides mechanical stability to the substrate.
- Drilling and Vias Formation: Drill holes or vias in the substrate material to establish electrical connections between different layers. Advanced drilling techniques, such as laser drilling, may be used to achieve precise hole sizes and positioning. The vias are plated with conductive material to create electrical pathways between the layers.
- Conductor Patterning: Apply a thin layer of conductive material, typically copper, onto the surface of the substrate using processes like sputtering, electroplating, or chemical deposition. The conductive material is patterned to create the desired circuit traces, pads, and interconnects using photolithography and etching techniques.
- Surface Finish Application: Apply a surface finish to protect the exposed copper surfaces from oxidation and facilitate soldering during assembly. Common surface finishes include electroless nickel immersion gold (ENIG), organic solderability preservative (OSP), and immersion silver.
- Solder Mask Application: Apply a solder mask layer over the substrate surface to insulate the conductive traces and define solderable areas for component attachment. The solder mask is typically applied using screen printing or spray coating techniques and cured using ultraviolet (UV) light.
- Final Inspection and Testing:Conduct thorough inspection and testing of the fabricated ABS to ensure compliance with design specifications and quality standards. This may include dimensional inspection, electrical continuity testing, and reliability testing to validate the performance and reliability of the substrates.
Once the ABS manufacturing process is complete, the substrates are ready for assembly with integrated circuits and other electronic components to manufacture high-performance electronic devices. Each step in the manufacturing process requires precision, attention to detail, and adherence to quality control measures to produce ABS with superior performance and reliability.
How much should an ABS cost?
The cost of an Advanced BGA Substrate (ABS) can vary significantly depending on various factors such as:
- Complexity of Design:More complex designs with higher layer counts, finer trace widths, and tighter tolerances typically incur higher manufacturing costs due to increased material and processing requirements.
- Substrate Material: The choice of substrate material can greatly impact the cost. Materials like high-speed laminates or ceramics tend to be more expensive than standard FR-4 substrates due to their superior electrical properties and performance characteristics.
- Manufacturing Process: Advanced manufacturing processes, such as laser drilling, sequential lamination, and advanced surface finishes, can add to the overall manufacturing cost. Additionally, processes that require specialized equipment or expertise may incur additional expenses.
- Volume and Scale: Economies of scale play a significant role in determining the cost of ABS. Larger production volumes generally lead to lower per-unit costs due to optimized manufacturing processes and bulk purchasing of materials.
- Quality and Reliability Requirements: Meeting stringent quality and reliability standards may necessitate additional testing, inspection, and process controls, which can increase the overall cost of production.
- Customization and Special Features: Customized features, such as unique shapes, sizes, or special material properties, can increase the cost of ABS production. Similarly, the incorporation of advanced technologies, such as embedded passive components or advanced packaging techniques, may also impact costs.
- Supplier and Location: The choice of supplier and manufacturing location can influence costs due to differences in labor rates, overhead expenses, and logistical factors.
Given these variables, it’s challenging to provide a specific cost for ABS without knowing the specific requirements of the design and production. Typically, ABS costs can range from a few dollars to several tens of dollars per unit, with prices varying based on the aforementioned factors. Companies involved in ABS manufacturing can provide detailed cost estimates based on the specific design and production requirements.
What is ABS base material?
The base material of an Advanced BGA Substrate (ABS) refers to the primary substrate material used as the foundation for constructing the substrate layers and circuitry. Several types of materials can serve as the base material for ABS, each offering different properties and characteristics suited to specific application requirements. Some common ABS base materials include:
- FR-4 (Flame Retardant 4): FR-4 is a widely used epoxy-based laminate material composed of woven glass fabric impregnated with an epoxy resin. It is known for its excellent electrical insulation properties, mechanical strength, and affordability. FR-4 is suitable for a wide range of applications and is commonly used in consumer electronics, telecommunications, and industrial equipment.
- High-Speed Laminates: High-speed laminates are engineered materials optimized for high-frequency signal transmission and impedance control. These laminates typically incorporate specialized resin systems and reinforcement materials to minimize signal loss and distortion at high frequencies. High-speed laminates are used in applications requiring high-speed data transmission, such as high-performance computing, telecommunications, and aerospace electronics.
- Ceramic Substrates: Ceramic substrates are made from materials such as alumina (aluminum oxide) or aluminum nitride (AlN) and offer exceptional thermal conductivity, mechanical stability, and reliability. Ceramic substrates are well-suited for applications requiring high-power dissipation, thermal management, and reliability in harsh operating environments. They are commonly used in power electronics, RF/microwave applications, and automotive electronics.
- Metal Core Substrates: Metal core substrates feature a layer of metal, such as aluminum or copper, sandwiched between insulating layers. These substrates offer superior thermal conductivity and heat dissipation properties, making them ideal for applications requiring efficient thermal management, such as LED lighting, power electronics, and automotive applications.
- Flexible Substrates: Flexible substrates are made from thin, flexible materials such as polyimide or polyester film. These substrates offer advantages such as flexibility, lightweight, and compactness, making them suitable for applications requiring conformal or bendable electronics, such as wearable devices, flexible displays, and medical implants.
The choice of ABS base material depends on various factors, including electrical performance requirements, thermal management needs, mechanical constraints, cost considerations, and specific application demands. Designers select the most appropriate base material based on these factors to achieve the desired performance and reliability in their electronic devices.
Which company manufactures ABS?
Many companies are involved in the manufacture of Advanced BGA Substrate (ABS). Some of the major manufacturers include internationally renowned electronic component manufacturers, semiconductor companies, and companies specializing in PCB (Printed Circuit Board) and packaging technologies.
For example, companies like Intel in the United States, Delta Electronics in Taiwan, Hitachi in Japan, and Infineon in Germany typically develop and produce high-performance packaging and circuit board technologies, including ABS, internally.
In addition, some companies specializing in PCB manufacturing also participate in ABS production. For example, companies like Nippon Mektron in Japan, Sanmina in the United States, and Tripod Technology in Taiwan also offer ABS manufacturing services on their production lines.
In our company, we can also manufacture ABS. As a company focused on electronic component manufacturing, we have advanced production equipment and technology, as well as the professional knowledge and experience required to manufacture high-performance ABS. Our manufacturing process strictly follows international standards and adopts the most advanced techniques and processes to ensure that the quality and performance of our products meet customer requirements.
Our ABS manufacturing capabilities include the following:
- Design and Engineering Support: We have a team of experienced engineers who can provide comprehensive services from design to engineering support. We work with customers to customize ABS designs to ensure they meet performance and reliability requirements.
- Material Selection and Procurement: We collaborate with globally recognized material suppliers to ensure the use of high-quality substrates and chemical materials. We select suitable materials according to customer requirements to meet specific application needs.
- Advanced Manufacturing Processes: We utilize advanced manufacturing processes and equipment, including precision printing, etching, drilling, surface treatment, and inspection equipment. These devices enable high-precision manufacturing and reliability testing to ensure product quality and performance at the highest level.
- Quality Control and Testing: We strictly adhere to quality control standards and conduct comprehensive quality inspections and tests at each manufacturing stage. From raw materials to finished products, we perform rigorous inspections to ensure that our products meet customer specifications and requirements.
In conclusion, as a company with extensive experience and professional expertise, we have the capability to manufacture high-performance ABS and provide customized solutions and quality services to our customers. We are committed to establishing long-term partnerships with customers to drive the development and innovation of electronic technology.
What are the 7 qualities of good customer service?
Good customer service is characterized by several key qualities that contribute to positive customer experiences and satisfaction. Here are seven qualities of good customer service:
- Responsiveness: Good customer service involves promptly addressing customer inquiries, concerns, and requests. Responding to customer needs in a timely manner demonstrates attentiveness and shows that their satisfaction is a priority.
- Empathy: Empathy involves understanding and acknowledging the customer’s perspective, emotions, and concerns. Good customer service representatives show empathy by listening actively, expressing understanding, and showing genuine concern for the customer’s situation.
- Communication Skills: Effective communication is essential for providing good customer service. This includes clear and concise verbal communication, active listening, and the ability to convey information in a manner that is easily understood by the customer.
- Problem-solving Ability: Good customer service involves the ability to effectively address and resolve customer issues and problems. Customer service representatives should be skilled at identifying root causes, offering solutions, and taking appropriate action to resolve issues to the customer’s satisfaction.
- Professionalism: Professionalism encompasses maintaining a positive attitude, being courteous and respectful, and adhering to company policies and procedures. Good customer service representatives exhibit professionalism in their interactions with customers, regardless of the situation.
- Product Knowledge: Good customer service requires a thorough understanding of the company’s products or services. Customer service representatives should possess comprehensive product knowledge to effectively answer customer questions, provide assistance, and offer relevant recommendations.
- Consistency: Consistency is key to delivering good customer service across all interactions and touchpoints. Customers expect consistent levels of service quality, reliability, and responsiveness each time they interact with a company. Consistently meeting or exceeding customer expectations fosters trust and loyalty.
By embodying these qualities, businesses can cultivate strong relationships with their customers, enhance satisfaction levels, and differentiate themselves in a competitive marketplace.
FAQs
What is ABS?
ABS stands for Advanced BGA Substrate. It is a sophisticated platform used in the packaging of integrated circuits (ICs), particularly for high-performance applications.
What are the key features of ABS?
ABS features advanced substrate materials, fine-line technology, high-density interconnects, and enhanced thermal management capabilities. It supports higher levels of integration, performance, and reliability compared to standard BGA substrates.
What are the applications of ABS?
ABS is used in a wide range of applications requiring high-speed signal transmission, high-frequency operation, and compact form factors. Common applications include mobile devices, computers, networking equipment, automotive electronics, and aerospace technologies.
How does ABS differ from standard BGA substrates?
ABS offers enhancements in substrate design, material properties, and manufacturing processes compared to standard BGA substrates. It typically features finer lines, smaller vias, more layers, and superior thermal management capabilities, making it suitable for demanding high-performance applications.
What are the advantages of using ABS?
The advantages of ABS include improved signal integrity, higher density interconnects, enhanced thermal performance, and greater reliability compared to standard BGA substrates. ABS enables the development of smaller, more powerful electronic devices with superior performance characteristics.
How is ABS manufactured?
ABS is manufactured through a series of processes including substrate material preparation, layer stackup design, lamination, drilling and vias formation, conductor patterning, surface finish application, solder mask application, and final inspection and testing.
What factors influence the cost of ABS?
The cost of ABS depends on factors such as the complexity of design, substrate material, manufacturing process, volume and scale of production, quality and reliability requirements, customization, and supplier and location considerations.
Where can I find ABS manufacturers?
ABS manufacturers include semiconductor companies, electronic component manufacturers, PCB manufacturers, and companies specializing in packaging technologies. Many of these companies offer ABS manufacturing services as part of their product offerings.
How can I ensure the quality of ABS?
To ensure the quality of ABS, it is essential to work with reputable manufacturers who adhere to stringent quality control standards and industry best practices. Additionally, thorough testing and inspection should be conducted throughout the manufacturing process to validate product performance and reliability.