Ajinomoto(ABF) Substrate Manufacturer
Ajinomoto(ABF) Substrate Manufacturer and Microtrace Substrate vender. We use advanced Msap and Sap technology to produce the multilayer interconnection ABF substrates from 4 to 22 layers.
Ajinomoto (ABF) Substrate is a specialized medium meticulously designed to foster optimal microbial growth in various biotechnological applications. Crafted by Ajinomoto Co., Ltd., a pioneering leader in food and biotechnology industries, ABF Substrate offers a precise balance of nutrients, including carbon sources, nitrogen compounds, vitamins, and minerals, essential for robust microbial cultivation.
Tailored for versatility, ABF Substrate accommodates a broad spectrum of microorganisms, encompassing bacteria, fungi, yeast, and beyond, facilitating diverse research, industrial processes, and pharmaceutical developments. Its formulation ensures consistent performance, reliability, and reproducibility, empowering scientists and engineers to achieve desired outcomes with confidence.
ABF Substrate’s adaptability spans from laboratory-scale experiments to large-scale industrial bioprocessing, contributing to advancements in enzyme production, antibiotic synthesis, and pharmaceutical manufacturing. With stringent quality control measures and a commitment to excellence, Ajinomoto delivers a substrate that epitomizes precision, innovation, and efficacy in microbial cultivation.
What is Ajinomoto (ABF) Substrate?
Ajinomoto (ABF) substrate is a specialized medium used in biotechnology and microbiology for the cultivation of microorganisms, particularly bacteria, fungi, and yeast. Developed by Ajinomoto Co., Inc., a Japanese company known for its production of amino acids and food seasonings, ABF substrate provides an ideal environment for microbial growth and metabolism.
The composition of ABF substrate typically includes a carefully balanced mixture of nutrients essential for microbial growth, such as carbon, nitrogen, vitamins, and minerals. These nutrients are formulated to support the specific requirements of the target microorganism, ensuring optimal growth rates and biomass production.
ABF substrate is often used in research laboratories, industrial bioprocessing facilities, and pharmaceutical companies for various applications, including the production of enzymes, antibiotics, and other biologically active compounds. Its versatility and consistency make it a preferred choice for microbial cultivation in both academic and commercial settings.
In addition to its use in biotechnology, ABF substrate also finds applications in food and beverage production. Its high-quality ingredients and precise formulation make it suitable for fermentation processes in the food industry, contributing to the development of flavors, textures, and nutritional profiles in various food products.
Overall, Ajinomoto (ABF) substrate serves as a reliable and effective medium for cultivating microorganisms, facilitating research and development efforts in biotechnology, pharmaceuticals, and food science. Its standardized composition and proven performance make it a valuable tool for scientists and engineers working in microbial fermentation and related fields.
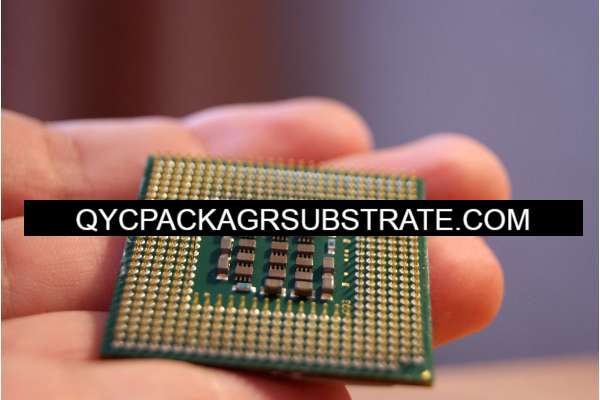
Ajinomoto(ABF) Substrate Manufacturer
What are the Ajinomoto (ABF) Substrate Design Guidelines?
The specific design guidelines for Ajinomoto (ABF) substrate may vary depending on the intended application and the requirements of the microorganism being cultivated. However, some general principles and considerations typically guide the formulation of ABF substrate:
- Nutrient Composition: ABF substrate is designed to provide all essential nutrients required for microbial growth, including carbon, nitrogen, vitamins, minerals, and trace elements. The precise composition may vary based on the metabolic needs of the target microorganism.
- Optimal pH: The pH of the substrate is carefully controlled to create an environment conducive to microbial growth. Most microorganisms have an optimal pH range for growth, and ABF substrate is formulated to maintain this pH range throughout the cultivation process.
- Oxygen Requirements: The oxygen availability in the substrate is important for aerobic microorganisms. ABF substrate design may include mechanisms to ensure adequate oxygen transfer to support microbial respiration.
- Sterility: Contamination can jeopardize the integrity of microbial cultures and compromise experimental results. Therefore, ABF substrate design includes measures to ensure sterility, such as autoclaving or sterile filtration of components.
- Batch-to-Batch Consistency: Consistency in substrate composition is crucial for reproducible results in microbial cultivation. Design guidelines emphasize the importance of quality control measures to maintain uniformity across different batches of ABF substrate.
- Scale-Up Considerations: ABF substrate should be scalable to accommodate various production scales, from laboratory research to industrial bioprocessing. Design guidelines may include provisions for scaling up production while maintaining the integrity of the substrate.
- Cost Efficiency: While providing optimal growth conditions for microorganisms, ABF substrate design also considers cost efficiency. This may involve optimizing nutrient concentrations and sourcing affordable raw materials without compromising performance.
- Compatibility with Downstream Processing: ABF substrate design takes into account compatibility with downstream processing steps, such as harvesting, extraction, and purification of microbial products. Substrate components should not interfere with these processes or compromise product purity.
By adhering to these design guidelines, developers can create ABF substrate formulations tailored to specific microbial cultures and applications, ensuring reliable and reproducible results in microbial cultivation and bioprocessing.
What is the Ajinomoto (ABF) Substrate Fabrication Process?
The fabrication process for Ajinomoto (ABF) substrate involves several steps to prepare a medium that provides the necessary nutrients and conditions for microbial growth. While specific details may vary based on the formulation and intended application, a typical fabrication process includes the following stages:
- Raw Material Selection: High-quality raw materials are selected based on their suitability for microbial cultivation and the desired composition of the substrate. These may include carbon sources (such as sugars or carbohydrates), nitrogen sources (such as amino acids or peptides), vitamins, minerals, and other essential nutrients.
- Weighing and Mixing: The selected raw materials are weighed according to the formulation recipe. Precision is crucial to ensure the correct composition of the substrate. The weighed materials are then thoroughly mixed to achieve homogeneity and uniform distribution of nutrients.
- Sterilization: To prevent contamination and ensure the sterility of the substrate, the mixture is subjected to sterilization. This is typically done using autoclaving, which involves exposing the substrate to high-pressure steam at elevated temperatures for a specified period. Alternatively, sterile filtration may be used for heat-sensitive components.
- pH Adjustment: The pH of the substrate is adjusted to the optimal range for the growth of the target microorganism. Acids or bases may be added to achieve the desired pH, and pH indicators or probes may be used to monitor and control pH throughout the process.
- Packaging and Storage: Once sterilized and pH-adjusted, the ABF substrate is transferred to sterile containers, such as bottles, flasks, or bags, depending on the intended application and scale of production. Proper labeling and documentation are essential for traceability and quality control. The packaged substrate may be stored under controlled conditions until ready for use.
- Quality Control: Quality control measures are implemented throughout the fabrication process to ensure the consistency, purity, and performance of the ABF substrate. This may include testing for sterility, pH, nutrient concentration, and absence of contaminants before, during, and after fabrication.
By following these steps, manufacturers can produce Ajinomoto (ABF) substrate formulations that meet the specific requirements of microbial cultivation applications, from research and development to industrial bioprocessing. Each stage of the fabrication process is carefully controlled to optimize the growth conditions for microorganisms and ensure the reproducibility of results.
How do you manufacture Ajinomoto (ABF) Substrate?
The manufacturing process of Ajinomoto (ABF) substrate involves several key steps to create a specialized medium suitable for microbial cultivation. While the exact process may vary depending on the specific formulation and intended application, here is a general outline of how Ajinomoto (ABF) substrate is manufactured:
- Raw Material Selection:High-quality raw materials are carefully selected based on their composition and suitability for supporting microbial growth. These may include carbon sources (such as glucose, sucrose, or starch), nitrogen sources (such as amino acids, peptides, or ammonium salts), vitamins, minerals, and other essential nutrients.
- Formulation Development: The formulation of the ABF substrate is developed based on the nutritional requirements of the target microorganism and the desired characteristics of the final product. This may involve adjusting the concentrations of various nutrients to optimize growth rates, biomass yield, and product quality.
- Weighing and Mixing: The selected raw materials are accurately weighed according to the formulation recipe. Precision is essential to ensure the reproducibility and consistency of the substrate. The weighed materials are then thoroughly mixed to achieve homogeneity and uniform distribution of nutrients.
- Sterilization: To eliminate microbial contaminants and ensure the sterility of the substrate, the mixture is subjected to sterilization. This is typically achieved through autoclaving, which involves exposing the substrate to high-pressure steam at elevated temperatures for a specified period. Alternatively, sterile filtration may be used for heat-sensitive components.
- pH Adjustment: The pH of the substrate is adjusted to the optimal range for the growth of the target microorganism. Acids or bases may be added to achieve the desired pH level, and pH indicators or probes may be used to monitor and control pH throughout the process.
- Packaging and Storage: Once sterilized and pH-adjusted, the ABF substrate is transferred to sterile containers, such as bottles, flasks, or bags, depending on the intended application and scale of production. Proper labeling and documentation are essential for traceability and quality control. The packaged substrate may be stored under controlled conditions until ready for use.
- Quality Control: Quality control measures are implemented throughout the manufacturing process to ensure the consistency, purity, and performance of the ABF substrate. This may include testing for sterility, pH, nutrient concentration, and absence of contaminants before, during, and after fabrication.
By following these steps, manufacturers can produce Ajinomoto (ABF) substrate formulations that meet the specific requirements of microbial cultivation applications, ranging from research and development to industrial bioprocessing. Each stage of the manufacturing process is carefully controlled to optimize growth conditions for microorganisms and ensure the reproducibility of results.
How much should Ajinomoto (ABF) Substrate cost?
The cost of Ajinomoto (ABF) substrate can vary depending on several factors, including the formulation complexity, raw material costs, production scale, and market demand. Since Ajinomoto (ABF) substrate is a specialized medium used in biotechnology, microbiology, and related fields, it tends to be priced higher than standard culture media due to its specific composition and performance characteristics.
The cost of Ajinomoto (ABF) substrate may be influenced by the following factors:
- Raw Material Costs: The cost of raw materials used in the formulation of ABF substrate, such as sugars, amino acids, vitamins, and minerals, can fluctuate based on market conditions and availability. Prices may vary depending on factors such as purity, sourcing, and volume discounts.
- Formulation Complexity: ABF substrate formulations may vary in complexity depending on the nutritional requirements of the target microorganism and the desired characteristics of the final product. More complex formulations with specialized nutrients or additives may incur higher production costs.
- Production Scale: Economies of scale can significantly impact the cost of manufacturing ABF substrate. Larger production volumes may result in lower per-unit production costs due to efficiencies in raw material procurement, manufacturing processes, and overhead expenses.
- Quality Control Standards: Stringent quality control measures to ensure product consistency, purity, and performance can add to the overall production costs of ABF substrate. Investments in quality assurance, testing equipment, and compliance with regulatory standards may contribute to higher prices.
- Market Demand and Competition: Market dynamics and competition within the biotechnology and microbiology sectors can influence pricing strategies for ABF substrate. Factors such as market demand, supply chain disruptions, and competitor pricing may impact the pricing decisions of manufacturers.
It’s important for consumers to consider the value proposition of Ajinomoto (ABF) substrate, taking into account factors such as performance, reliability, reproducibility, and technical support offered by the manufacturer. While ABF substrate may have a higher upfront cost compared to standard culture media, its specialized formulation and performance benefits may justify the investment for certain applications requiring precise control over microbial growth conditions.
What is Ajinomoto (ABF) Substrate base material?
The base materials of Ajinomoto (ABF) substrate typically include a combination of organic and inorganic compounds that serve as the primary sources of carbon, nitrogen, vitamins, minerals, and other essential nutrients for microbial growth. While the exact composition may vary depending on the specific formulation and intended application, here are some common base materials that may be used:
- Carbon Sources: Sugars (such as glucose, sucrose, fructose), carbohydrates (such as starches), organic acids (such as citric acid, acetic acid), and other carbon-containing compounds provide energy and carbon for microbial metabolism.
- Nitrogen Sources: Amino acids (such as glutamate, lysine, arginine), peptides, proteins, ammonium salts (such as ammonium sulfate, ammonium chloride), and nitrogen-containing compounds serve as nitrogen sources for protein synthesis and cell growth.
- Vitamins: Various vitamins, including B-complex vitamins (such as thiamine, riboflavin, niacin), vitamins A, C, D, E, and K, are added to support metabolic pathways and enzymatic reactions essential for microbial growth and metabolism.
- Minerals and Trace Elements: Inorganic salts containing essential minerals and trace elements, such as potassium, magnesium, calcium, iron, zinc, copper, manganese, and others, are included to provide cofactors for enzymatic reactions and maintain cellular homeostasis.
- Buffering Agents: Buffering agents such as phosphate buffers or citrate buffers may be added to maintain the pH of the substrate within the optimal range for microbial growth.
- Stabilizers and Additives: Stabilizers, antioxidants, and other additives may be incorporated into the substrate to enhance stability, shelf-life, and performance.
The specific combination and concentration of these base materials in Ajinomoto (ABF) substrate formulations are carefully optimized to meet the nutritional requirements of the target microorganism and achieve desired growth characteristics. Additionally, quality control measures ensure the consistency, purity, and performance of the base materials to support reproducible results in microbial cultivation applications.
Which company produces Ajinomoto (ABF) Substrate?
Ajinomoto (ABF) Substrate is produced by the Japanese company Ajinomoto Co., Ltd. As a globally renowned food and biotechnology company, Ajinomoto focuses on manufacturing high-quality seasonings, additives, and bioproducts. They have developed Ajinomoto (ABF) Substrate, a specialized medium for microbial cultivation, providing an ideal growth environment.
With extensive experience and expertise, Ajinomoto’s ABF substrate products are carefully designed and optimized to meet various microbial cultivation needs. These substrate products undergo rigorous quality control to ensure the stability and purity of their components, thus offering reliable performance and consistent results.
Our company is also capable of producing Ajinomoto (ABF) Substrate, drawing on Ajinomoto’s experience and technology. Equipped with advanced manufacturing facilities and a professional team, we can customize ABF substrate products with different formulations according to customer requirements. We are committed to delivering high-quality, reliable products and ensuring compliance with industry standards and regulations through strict quality control procedures.
Our production process includes raw material procurement, formulation design, manufacturing, quality control, and packaging. We pay attention to the details of the production process and quality control at each stage to ensure that the final products meet customer expectations in terms of quality and performance.
As a trusted partner, we are dedicated to providing high-quality Ajinomoto (ABF) Substrate products and professional technical support to our customers. We are willing to collaborate with customers to drive advancements in microbial cultivation and biotechnology, contributing to human health and quality of life.
What are the 7 qualities of good customer service?
Certainly! Good customer service is characterized by several key qualities that contribute to positive experiences and relationships with customers. Here are seven essential qualities:
- Promptness:Good customer service involves responding to inquiries, concerns, and requests in a timely manner. Whether it’s answering a phone call, replying to an email, or addressing a customer’s question in person, promptness demonstrates respect for the customer’s time and urgency.
- Empathy: Empathy is the ability to understand and share the feelings of others. In customer service, empathy means putting yourself in the customer’s shoes, acknowledging their emotions, and showing genuine concern for their needs and challenges.
- Clear Communication: Effective communication is essential for conveying information, resolving issues, and building rapport with customers. Good customer service representatives communicate clearly, using language that is easy to understand, and actively listen to ensure they understand the customer’s needs.
- Product Knowledge: Good customer service requires a thorough understanding of the products or services being offered. Customer service representatives should be knowledgeable about product features, benefits, pricing, and policies so they can provide accurate information and assist customers effectively.
- Problem-Solving Skills: Customer service often involves addressing problems or complaints. Good customer service representatives are adept at identifying issues, analyzing situations, and finding appropriate solutions that meet the customer’s needs and expectations.
- Professionalism: Professionalism encompasses qualities such as courtesy, respect, integrity, and reliability. Good customer service representatives conduct themselves in a professional manner, remaining calm and composed, even in challenging situations, and treating customers with courtesy and respect.
- Follow-Up: Following up with customers after their interaction demonstrates care and commitment to their satisfaction. Good customer service representatives may follow up to ensure that issues have been resolved satisfactorily, gather feedback, or offer additional assistance, showing appreciation for the customer’s business.
By embodying these qualities, businesses can deliver exceptional customer service experiences that foster trust, loyalty, and positive word-of-mouth recommendations, ultimately contributing to long-term success and customer satisfaction.
FAQs
What is Ajinomoto (ABF) Substrate?
Ajinomoto (ABF) Substrate is a specialized medium used for microbial cultivation in biotechnology, microbiology, and related fields. It provides essential nutrients and optimal growth conditions for various microorganisms.
What are the components of Ajinomoto (ABF) Substrate?
The components of ABF substrate typically include carbon sources, nitrogen sources, vitamins, minerals, and other essential nutrients necessary for microbial growth. The exact composition may vary depending on the formulation and application.
What microorganisms can be cultured using Ajinomoto (ABF) Substrate?
ABF substrate can support the growth of a wide range of microorganisms, including bacteria, fungi, yeast, and other microbial species commonly used in research, industrial bioprocessing, and pharmaceutical applications.
How is Ajinomoto (ABF) Substrate prepared for use?
ABF substrate is typically prepared by dissolving the powdered or granulated formulation in sterile water or another suitable solvent according to the manufacturer’s instructions. The pH may be adjusted as needed, and the substrate is sterilized before use to prevent contamination.
What are the advantages of using Ajinomoto (ABF) Substrate?
ABF substrate offers several advantages, including consistent performance, reproducibility, and the ability to customize formulations to meet specific microbial cultivation requirements. It provides an ideal growth environment for microorganisms, resulting in high biomass yield and product quality.
How should Ajinomoto (ABF) Substrate be stored?
ABF substrate should be stored in a cool, dry place away from direct sunlight and moisture. It is important to follow the manufacturer’s instructions for storage conditions to maintain the stability and integrity of the substrate.
Can Ajinomoto (ABF) Substrate be used in industrial-scale bioprocessing?
Yes, Ajinomoto (ABF) Substrate is suitable for use in industrial-scale bioprocessing applications, including the production of enzymes, antibiotics, pharmaceuticals, and other biologically active compounds. It can be scaled up to meet production requirements while maintaining performance and consistency.
Where can I purchase Ajinomoto (ABF) Substrate?
Ajinomoto (ABF) Substrate may be available for purchase directly from the manufacturer or through authorized distributors specializing in laboratory and bioprocessing supplies. Customers can contact Ajinomoto or their local distributor for pricing and availability information.