Cavity Substrate/PCB Manufacturer the Package Substrate will be made with Showa Denko and Ajinomoto High speed materials.or other types high speed materials and high frequency materials.
Cavity PCBs, short for Cavity Printed Circuit Boards, are a specialized type of electronic circuit board that features strategically incorporated void spaces or cavities within its design. These hollowed areas serve various functional purposes, catering to specific requirements in electronic applications.
The utilization of Cavity PCBs is prevalent in scenarios where precise design considerations are crucial. One primary application is in RF (Radio Frequency) technology, where these boards are employed to isolate sensitive components from external electromagnetic interference. The cavities act as protective enclosures, preventing signal leakage and ensuring optimal performance.
Moreover, Cavity PCBs contribute to the miniaturization of electronic devices. By integrating carefully planned cutouts, these boards enable the accommodation of components within the void spaces, reducing the overall size of the PCB. This feature is particularly advantageous in portable electronic devices and other space-constrained applications.
Another noteworthy application of Cavity PCBs is in thermal management. These boards can incorporate specific voids to house heat sinks or facilitate improved airflow within the electronic system. Efficient heat dissipation is crucial for maintaining the reliability and performance of electronic components, making Cavity PCBs valuable in devices where thermal considerations are paramount.
Manufacturing Cavity PCBs demands specialized techniques to ensure precision and structural integrity. Advanced methods such as milling or routing are commonly employed to create the cavities without compromising the overall strength of the PCB.
In essence, Cavity PCBs represent a sophisticated approach to electronic circuit design, offering tailored solutions for miniaturization, electromagnetic shielding, and thermal optimization in diverse electronic applications.
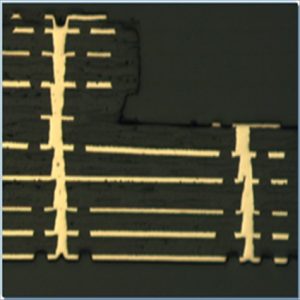
What functions does Cavity Substrate serve?
Cavity Substrates play a multifaceted role, showcasing diverse functions shaped by their design intricacies and applications. Here’s a glimpse into the distinctive roles these specialized substrates embrace:
Maestros of Miniaturization: Cavity Substrates take center stage as facilitators of electronic miniaturization. Through the strategic inclusion of voids or cavities, these substrates empower the efficient organization and integration of electronic components within spatially constrained environments.
Conductors of Thermal Symphony: Emulating the thermal management finesse of Cavity PCBs, Cavity Substrates conduct a symphony of heat dissipation. Carefully positioned voids serve as havens for heat sinks or facilitators of increased airflow, orchestrating the graceful dispersion of heat generated by electronic components.
Guardians Against EMI Onslaught: Cavity Substrates emerge as stalwart guardians against electromagnetic interference. The thoughtfully designed cavities morph into protective shields, safeguarding sensitive electronic components from external electromagnetic fields and quelling the disruptive effects of EMI on overall device performance.
Pillars of Structural Resilience: Delving into design nuances and material characteristics, Cavity Substrates become pillars of structural integrity in electronic systems. The judicious placement of voids imparts a robust and mechanically resilient character, a crucial attribute in applications that prioritize durability and reliability.
Strategists of Component Integration: Cavity Substrates serve as strategic orchestrators of component integration within designated void spaces. This feature proves invaluable in applications where the isolation of specific components is paramount for performance optimization or security considerations.
Harbingers of Acoustic Harmony: Venturing into realms such as audio or sensor technologies, Cavity Substrates might play a role in reshaping acoustic properties. Ingeniously positioned voids act as agents of change, influencing sound propagation or mitigating vibrations to meet specific acoustic prerequisites.
Crafters of Circuit Flexibility: Cavity Substrates empower engineers with the artistic freedom to craft customized circuit layouts tailored to exacting performance criteria. This adaptability positions the substrate as a versatile tool, adeptly suited for a spectrum of electronic systems with unique demands.
In essence, the functions of a Cavity Substrate mirror its versatility, addressing challenges in miniaturization, thermal management, EMI shielding, structural robustness, component integration, acoustic refinement, and the artistry of designing bespoke circuit configurations.
What are the different types of Cavity Substrate?
Cavity Substrates encompass a rich variety of types, each intricately crafted to serve specific roles across diverse applications. Let’s embark on a journey through the unique attributes of these variants:
Metal Core Cavity Substrates (MCPCB): Robust and efficient, MCPCBs feature a metal core, often hewn from aluminum or copper, delivering exceptional thermal conductivity. They shine in applications such as LED lighting and power electronics, where adept heat dissipation is indispensable.
Ceramic Cavity Substrates: Rooted in ceramics like aluminum nitride (AlN) or alumina (Al2O3), these substrates excel in both thermal conductivity and electrical insulation. Their resilience finds a natural fit in high-power electronic applications.
Polymer Cavity Substrates: Infused with the flexibility of polymers or composite materials, these substrates prioritize adaptability and cost-effectiveness. Suited for wearable electronics, Polymer Cavity Substrates strike a delicate balance between weight considerations and flexibility.
Hybrid Cavity Substrates: Operating as material alchemists, hybrid substrates seamlessly merge elements to strike a balance between thermal efficiency, electrical insulation, and cost-effectiveness. Imagine a metal core dancing in harmony with a polymer layer—a true embodiment of versatility.
RF Cavity Substrates: Precision-engineered for radio frequency (RF) applications, these substrates minimize signal losses and confront electromagnetic interference head-on. Armed with specialized dielectric materials and intricate cavity structures, RF Cavity Substrates elevate performance in the RF spectrum.
Flex Cavity Substrates: Embracing flexibility through materials like polyimide or flexible PCBs, these substrates cater to applications demanding adaptability or conformation to irregular shapes. Devices with bending requirements find a steadfast ally in the pliability of Flex Cavity Substrates.
Multilayer Cavity Substrates: Unfurling a layered tapestry of materials, these substrates empower intricate circuit designs and streamlined component integration. A favored choice for applications yearning for high-density circuits and advanced functionalities.
Thick Film Cavity Substrates: Tapping into the finesse of thick-film technology, these substrates involve the meticulous deposition of ceramic paste on a substrate. Stepping into the spotlight in sensor applications and hybrid circuits, Thick Film Cavity Substrates epitomize precision and distinctive structures.
Choosing a Cavity Substrate is akin to orchestrating a symphony. Engineers navigate this diverse landscape, aligning substrate types seamlessly with the performance criteria and design aspirations of their projects.
How is Cavity Substrate related to PCB manufacturing?
The synergy between Cavity Substrates and the domain of PCB (Printed Circuit Board) manufacturing is profound, shaping the landscape of electronic devices by influencing both performance and design intricacies. The dynamic interplay between these elements unfolds through various dimensions:
Harmonious Integration into PCB Designs:
Cavity Substrates seamlessly weave into the fabric of PCB designs, assuming roles as central components or additional layers, adapting to the nuanced requirements of specific designs.
Elevated Thermal Governance:
In the realm of PCB manufacturing, Cavity Substrates, particularly those endowed with metal cores, emerge as champions of advanced thermal management.
Their structural ingenuity, featuring voids and cavities, orchestrates the strategic placement of heat sinks, amplifying the PCB’s prowess for efficient heat dissipation—an imperative attribute to stave off overheating in electronic components.
Crafters of Miniaturization:
The deliberate inclusion of Cavity Substrates in PCBs serves as an artisanal touch to the intricate canvas of miniaturization, crafting an environment conducive to the compact orchestration of electronic components.
This artistic endeavor proves invaluable in applications where spatial constraints demand a reduction in size.
Stalwarts of Structural Resilience:
Cavity Substrates contribute significantly to the tapestry of PCB robustness. The intentional arrangement of voids and cavities fortifies the structural integrity, a foundational element in scenarios anticipating mechanical stress or vibrations.
Artisans of Adaptable Circuitry:
A defining brushstroke of Cavity Substrates lies in their fluidity, empowering engineers to paint customized circuit layouts tailored to the exacting strokes of performance criteria.
This dynamic flexibility proves instrumental in the creation of bespoke circuits for a diverse array of electronic symphonies.
Masters of Electromagnetic Harmony:
Certain Cavity Substrates, sculpted with specific materials and structural nuances, don the mantle of guardians against electromagnetic interference (EMI).
This shielding prowess assumes a pivotal role in applications where safeguarding sensitive components from the siren calls of external electromagnetic fields is a non-negotiable mandate.
Dance Partners in High-Frequency Designs:
RF (Radio Frequency) Cavity Substrates take center stage in the ballet of PCB manufacturing, pirouetting gracefully in high-frequency applications. Their choreography minimizes signal losses and interference, elevating the performance in frequency-sensitive vignettes.
Alchemy of Diverse Materials:
Cavity Substrates present a palette of material choices, a kaleidoscope ranging from metals to ceramics and polymers. The selection is akin to a painter’s choice of hues, dictated by the distinctive demands of the application.
This material medley influences thermal conductivity, electrical properties, and the overall symphony of performance, endowing engineers with a spectrum of options for compositional harmony.
In essence, the symbiosis of Cavity Substrates and PCB manufacturing is a ballet of innovation and purpose. Cavity Substrates choreograph the intricate pas de deux with PCBs, addressing thermal sonatas, choreographing the dance of miniaturization, fortifying the structural fortresses, facilitating adaptable circuitry, and introducing specialized notes. The orchestrated integration of Cavity Substrates into PCB designs stands as a testament to the artistry of electronic devices, where every stroke and nuance is calibrated for an opus of optimal functionality and reliability.
How does Cavity Substrate differ from traditional PCBs?
Cavity Substrates deviate significantly from the conventional landscape of traditional PCBs (Printed Circuit Boards), marking their distinct presence through unique attributes that redefine structural norms, thermal dynamics, and application versatility. Let’s embark on a journey through the nuances that distinguish them:
Architectural Uniqueness:
Traditional PCBs: Embrace a straightforward, flat design sans intentional voids, adhering to a two-dimensional paradigm. Materials like fiberglass or FR-4 are the customary building blocks.
Cavity Substrates: Introduce deliberate voids or cavities within the substrate, weaving a narrative of intricate three-dimensional architectures. This deliberate structuring allows for tailored configurations, catering to the specific demands of diverse applications.
Thermal Symphony:
Traditional PCBs: Lean on conventional avenues for heat dissipation, leveraging surface area and copper traces. Supplementary measures, such as heat sinks or thermal vias, may come into play.
Cavity Substrates: Particularly those graced with metal cores, such as Metal Core PCBs (MCPCBs), elevate the thermal performance. The artful integration of cavities facilitates the seamless addition of heat sinks, contributing to a superior thermal symphony. This makes them instrumental in applications where stringent thermal requirements take center stage.
Miniaturization Choreography:
Traditional PCBs: While technological strides allow for smaller designs, traditional boards may grapple with limitations in the pursuit of miniaturization, bound by their inherent two-dimensional nature.
Cavity Substrates: Purposeful inclusion of voids serves as the choreographer for efficient space utilization, fostering an environment conducive to miniaturization. This feature proves indispensable in applications where spatial constraints dictate the need for compact and intricately designed boards.
Flexibility Ballet:
Traditional PCBs: Adorned with a cloak of rigidity, traditional boards lack the fluidity needed for applications demanding flexibility or conformity to irregular shapes.
Cavity Substrates: Enter the stage with a variety of performances, including flexible PCBs within their repertoire. This adaptability proves instrumental in applications where the board must gracefully flex or conform to unconventional shapes.
Application-Specific Sonata:
Traditional PCBs: Find themselves at home in a diverse array of electronic devices, spanning consumer electronics to industrial machinery.
Cavity Substrates: Garner applause in applications with specific thermal or spatial prerequisites. Metal Core Cavity Substrates, for instance, take the spotlight in high-power LED lighting, automotive electronics, and power electronics where superior heat dissipation is a non-negotiable demand.
Material Symphony:
Traditional PCBs: Conventional compositions feature materials like FR-4, a composite marriage of epoxy resin and fiberglass, for the substrate.
Cavity Substrates: Contribute to a more diverse symphony of material choices, spanning metals (aluminum or copper for metal cores), ceramics (aluminum nitride, alumina), and polymers. The selection of materials orchestrates a harmonious performance, aligning with the unique demands of the application.
Cost Dynamics Ballet:
Traditional PCBs: Take center stage as the cost-effective stalwarts, their manufacturing processes imbued with simplicity.
Cavity Substrates: Engage in a more intricate dance, especially in specialized designs like Metal Core Cavity Substrates. This complexity may influence the grand cost dynamics of production.
In essence, Cavity Substrates etch their identity by introducing intentional voids, heralding advancements in thermal efficiency, miniaturization, and flexibility. The choice between Cavity Substrates and traditional PCBs becomes a narrative shaped by the unique demands of each application, with the former stepping into the limelight where thermal prowess and spatial optimization claim center stage.
What is the main structure and production technology of Cavity Substrate?
The symphony of Cavity Substrate unfolds through a meticulous dance of structure and production technologies, with Metal Core Cavity Substrates (MCPCBs) serving as our featured performer. Let’s embark on a journey to unravel the layers of their composition and the intricate steps involved in their production.
Harmony in Structure:
Metal Core Overture:
At the heart of MCPCB lies a robust metal core, a canvas often crafted from either aluminum or copper. This metallic foundation sets the stage for thermal prowess and mechanical resilience.
Dielectric Interlude:
A layer of dielectric material takes center stage above the metal core, performing a vital role in insulating the substrate electrically. This layer ensures a harmonious separation between the metal core and the conductive traces.
Conductive Traces Choreography:
Enter the dance of conductive traces, etched or printed onto the dielectric layer. These intricate pathways form the circuitry, connecting the electronic components in an orchestrated arrangement.
Cavities as Artful Crescendos:
The defining feature of Cavity Substrates emerges with deliberate cavities designed into the substrate. These voids are like artistic crescendos, strategically placed to house components, facilitate heat sinks, or serve other functional nuances.
Solder Mask and Silkscreen Elegance:
A layer of solder mask is elegantly applied, safeguarding the conductive traces from unintended soldering during assembly. Silkscreen may also be delicately added, a subtle touch for indicating component placement and conveying essential information.
Production Ballet:
Metal Core Prelude:
The ballet commences with the preparation of the metal core, a tailored cut of aluminum or copper, setting the stage for the forthcoming acts.
Dielectric Layer Enchantment:
A layer of dielectric material is enchantingly applied to the metal core, a dance achieved through methods like lamination or thermal transfer. This dielectric layer is carefully chosen for its insulating charm.
Conductive Traces Waltz:
Conductive traces make their entrance, intricately patterned onto the dielectric layer through processes like etching or the finesse of traditional PCB manufacturing. The waltz of connectivity begins.
Cavity Ballet:
Cavities take center stage, crafted with precision through milling, routing, or drilling processes. The choreography of these voids is tailored to the specific needs of the application, a ballet of form and function.
Solder Mask and Silkscreen Flourish:
The application of solder mask and silkscreen is a flourish of the artist’s brush. The mask shields, and the silkscreen adds visual notes, completing the aesthetic composition.
Component Mounting Pas de Deux:
Electronic components elegantly perform their pas de deux, finding their place within the designed cavities and connecting through the intricate conductive traces.
Assembly and Finishing Crescendo:
The grand crescendo arrives with the assembly of additional components and the final touches for the MCPCB’s ultimate purpose. Additional layers, coatings, or encapsulations add the finishing notes to the performance.
In essence, the structure and production of Cavity Substrates, embodied by the MCPCB, unfold as a captivating symphony where each element plays a crucial role. The dance of metal, dielectric layers, conductive traces, and deliberate cavities orchestrates a harmonious blend of form and function, creating a masterpiece in the realm of electronic substrate technology.
Frequently Asked Questions (FAQs)
What Advantages Does a Cavity Substrate Offer?
The utilization of Cavity Substrates brings forth advantages like superior thermal management, heightened possibilities for miniaturization, and adaptability to specific component requirements. These substrates find particular relevance in applications where effective heat dissipation is paramount.
In What Ways Do Cavity Substrates Differ from Traditional PCBs?
Distinctive in their design featuring intentional voids, Cavity Substrates set themselves apart from traditional PCBs. This unique construction empowers them with improved heat dissipation, enhanced miniaturization capabilities, and flexibility in catering to specific component needs, deviating from the conventional two-dimensional nature of PCBs.
What Does the Manufacturing Process of Cavity Substrates Entail?
The manufacturing journey of Cavity Substrates encompasses several steps. This includes the preparation of the metal core (if applicable), application of a dielectric layer, patterning of conductive traces, creation of intentional cavities, and the addition of protective layers like solder mask and silkscreen. The specific processes may vary based on the type of Cavity Substrate and its intended application.
Can Cavity Substrates be Integrated into Flexible Electronics?
Indeed, specific types of Cavity Substrates, such as flexible PCBs adorned with intentional voids, lend themselves well to flexible electronics. The adaptability and flexibility of these substrates make them fitting for applications where the board necessitates conformity to irregular shapes or undergoes bending.
What Varieties of Cavity Substrates Exist?
Yes, various types of Cavity Substrates exist, differentiated by the materials utilized. This includes metal core substrates (aluminum or copper), ceramic substrates, and flexible substrates. Each type caters to specific application needs, spanning thermal management, high-frequency performance, or flexibility.
What Considerations Should Guide the Selection of a Cavity Substrate Manufacturer?
When selecting a Cavity Substrate manufacturer, key considerations include their experience in producing substrates for similar applications, the breadth of materials and technologies offered, adherence to robust quality control processes, and the ability to meet specific customization requirements. Evaluating their track record and customer reviews is also imperative to ascertain reliability.
Conclusion
In conclusion, Cavity Substrates emerge as a dynamic and innovative realm within the landscape of electronic components, reshaping the narrative of traditional PCBs. With intentional voids and strategic cavities, these substrates introduce a symphony of advantages, from enhanced thermal management and miniaturization opportunities to a heightened adaptability to diverse application needs.
The deliberate structuring of materials, including metals like aluminum or copper, ceramics, and polymers, defines the versatility of Cavity Substrates. Their role in thermal dynamics, especially in high-power applications, underscores their significance in contemporary electronics.
The manufacturing journey of Cavity Substrates is a carefully choreographed process, involving the preparation of metal cores, the application of dielectric layers, and the precise patterning of conductive traces. The intentional creation of voids and the addition of protective layers contribute to substrates that not only meet but exceed the demands of modern electronic applications.
As we navigate the nuanced dance between intentional voids and enhanced functionalities, the applications span diverse industries, from LED lighting to power electronics, showcasing the adaptability and prowess of Cavity Substrates.
In essence, Cavity Substrates redefine the conventional notions of PCBs, presenting a symphony of design, technology, and functionality. Whether it’s in the realm of thermal efficiency, miniaturization, or tailored configurations, Cavity Substrates have firmly established themselves as pivotal players in the ever-evolving landscape of electronic components.