Semiconductor FC BGA substrate Manufacturer
What is a Semiconductor FC BGA Substrate?
Semiconductor FC BGA substrate Manufacturer. the Package Substrate will be made with Showa Denko and Ajinomoto High speed materials.or other types high speed materials and high frequency materials.
A semiconductor FC BGA substrate is a type of semiconductor packaging technology, with the full name “Flip Chip Ball Grid Array.” This technology is commonly used for the packaging and connection of integrated circuits (ICs), especially in high-density, high-performance semiconductor devices.
In a semiconductor FC BGA substrate, the chip is flipped and directly connected to the substrate, rather than through traditional wire bonds. The method of connecting the chip to the substrate typically involves micro-solder bumps or solder balls. The layout of the substrate usually consists of an array of metal balls connected to the chip pads, which are connected to the chip via methods like thermal bonding.
The advantages of FC BGA substrates include shorter signal transmission paths, higher connection density, lower resistance and inductance, better thermal performance, and improved mechanical strength. These characteristics make FC BGA substrates widely adopted in high-performance applications such as high-speed communication, computer processors, graphics processors, and other fields.
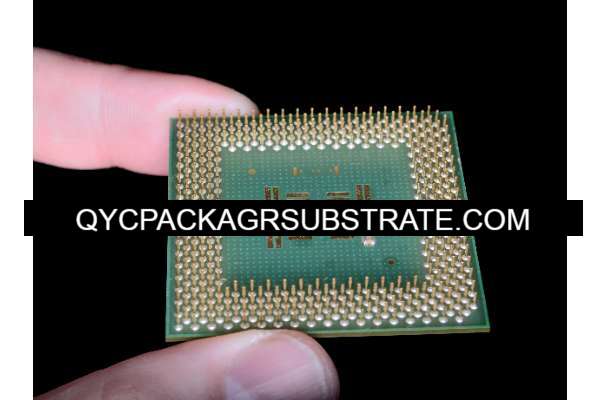
Semiconductor FC BGA substrate Manufacturer
What are the Functions of Semiconductor FC BGA Substrates?
The function of a semiconductor FC BGA substrate is to provide packaging and connection for integrated circuits (ICs). Specifically, its functions include:
- Chip encapsulation: The FC BGA substrate serves as a platform for encapsulating the chip, enabling it to be connected to the external world and protected.
- Chip-to-substrate connection: The FC BGA substrate flips the chip and directly connects it to the substrate through methods such as metal balls or solder points, facilitating electrical connections between the chip and the substrate.
- Electrical connections: The metal balls or solder points on the FC BGA substrate provide electrical connections between the chip pins and the substrate, allowing signals and power to be transmitted between the chip and the substrate.
- Heat dissipation support: Since FC BGA substrates typically have large heat dissipation areas, they help to conduct the heat generated by the chip to the substrate, thereby aiding in heat dissipation and maintaining the chip’s normal operating temperature.
- Mechanical support: FC BGA substrates also provide mechanical support for the chip, helping to prevent damage to the chip during use.
Overall, the function of a semiconductor FC BGA substrate is to encapsulate the chip, connect it to the substrate, and provide necessary electrical connections, heat dissipation support, and mechanical support, enabling the chip to function properly in electronic devices.
What are the Different Types of Semiconductor FC BGA Substrates?
There are several different types of semiconductor FC BGA substrates, some of the common ones include:
- Standard FC BGA Substrate: These substrates typically feature a conventional layout and connection method, suitable for most applications.
- Low-Cost FC BGA Substrate: These types of substrates often employ simplified manufacturing processes or materials to reduce costs, suitable for cost-sensitive applications.
- High-Density FC BGA Substrate: These substrates have more connection points and a denser layout, capable of supporting higher integration and more complex circuit designs.
- High-Performance FC BGA Substrate: These types of substrates typically utilize higher-grade materials and manufacturing processes to achieve higher frequencies, lower resistance, and better thermal performance, suitable for high-performance computing, communication, etc.
- Multilayer FC BGA Substrate: These substrates feature multiple layers of routing and connections, enabling more complex circuit designs and greater functional integration.
- Thermal Management FC BGA Substrate: These substrates are specially designed to optimize heat dissipation performance to address the heat generated by high-power chips.
- Customized FC BGA Substrate: Customized FC BGA substrates can provide specific features and characteristics according to specific application requirements and design specifications, such as specific packaging materials, connection methods, or thermal designs.
These are some common types of semiconductor FC BGA substrates, and there may be other specific types of substrates based on different application needs and performance requirements.
What is the Relationship Between Semiconductor FC BGA Substrates and IC Packaging?
The relationship between semiconductor FC BGA substrates and IC packaging is close, as semiconductor FC BGA substrates are commonly used as a form of IC packaging.
IC packaging involves encapsulating a chip (also known as an integrated circuit) into a protective casing to protect the chip, provide electrical connections, and facilitate connection with other electronic devices. Semiconductor FC BGA substrates are a common IC packaging technology that achieves a compact, high-density packaging form by flipping the chip and directly connecting it to the substrate.
The relationship between semiconductor FC BGA substrates and IC packaging is reflected in several aspects:
- Providing a packaging platform: Semiconductor FC BGA substrates provide a platform for chip packaging, allowing the chip to be connected to the external world and protected. Based on this packaging form, IC manufacturers can choose different packaging sizes, shapes, and characteristics to meet various application requirements.
- Achieving electrical connections: Semiconductor FC BGA substrates establish electrical connections between the chip pins and the substrate through methods such as metal balls or solder points, allowing signals and power to be transmitted between the chip and the substrate.
- Providing thermal and mechanical support: Semiconductor FC BGA substrates typically have large heat dissipation areas and provide mechanical support for the chip, aiding effective heat dissipation and preventing chip damage during use.
- Influencing performance and characteristics: The choice of IC packaging (including the use of FC BGA substrates) affects the performance, thermal dissipation capability, cost, and other characteristics of the final product. Therefore, when selecting appropriate IC packaging, it is necessary to consider the relevant characteristics and advantages of FC BGA substrates.
In summary, semiconductor FC BGA substrates are a form of IC packaging that provides a packaging platform, achieves electrical connections, and influences the performance and characteristics of the final product.
What are the Differences Between Semiconductor FC BGA Substrates and Traditional PCBs?
There are several key differences between semiconductor FC BGA substrates and traditional PCBs:
- Packaging Method: Semiconductor FC BGA substrates are typically used for packaging chips (integrated circuits), designed to directly connect the chip and provide protection, electrical connections, and heat dissipation support. Traditional PCBs (Printed Circuit Boards) are usually used to connect and support various electronic components such as resistors, capacitors, transistors, etc., and they do not directly encapsulate chips but rather are used for connecting and supporting multiple electronic components.
- Connection Method: Chips on semiconductor FC BGA substrates are typically directly connected to the substrate using methods such as solder balls or pads, while traditional PCBs typically use soldering or insertion connections to connect various electronic components.
- Packaging Materials and Processes: The packaging materials and processes of semiconductor FC BGA substrates are usually designed to meet special requirements such as high temperature and high frequency to ensure the performance and stability of the chips. The packaging materials and processes of traditional PCBs may vary depending on the application but typically do not require special requirements for chip packaging.
- Application Fields: Semiconductor FC BGA substrates are mainly used for the packaging and connection of integrated circuits (ICs), suitable for high-performance, high-density electronic devices such as microprocessors, graphics processors, etc. Traditional PCBs are widely used in various electronic devices and applications, ranging from consumer electronics to industrial control systems and other fields.
Overall, semiconductor FC BGA substrates and traditional PCBs have clear differences in packaging method, connection method, packaging materials, and application fields, suitable for different types of electronic devices and application scenarios.
What are the Main Structure and Production Technologies of Semiconductor FC BGA Substrates?
The main structure and production technology of semiconductor FC BGA substrates are as follows:
Main Structure:
- Substrate: The foundational part of the semiconductor FC BGA substrate, typically made of dielectric material, used to support and connect the chip.
- Chip: The integrated circuit chip, connected to the substrate after flipping to achieve electrical connections and functionality.
- Metal Balls: Conductive balls used to connect the chip pins and the substrate, typically fixed between the chip and the substrate through soldering or other connection methods.
- Encapsulation Material: Material used to encapsulate and protect the chip, typically epoxy resin or other special materials.
Production Technology:
- Substrate Manufacturing: Substrate manufacturing typically involves substrate design, cutting, molding, and processing. Substrates are usually made of glass fiber-reinforced epoxy resin (FR-4) or other dielectric materials, molded and processed according to design requirements.
- Chip Fabrication: Chip fabrication is a critical step in semiconductor manufacturing, involving wafer processing, chip dicing, and testing, typically carried out in dedicated semiconductor fabrication facilities.
- Solder Ball Connection: Solder balls are formed on both the chip and the substrate, and the chip is aligned and flipped onto the substrate. The chip is then connected to the substrate through heating or other connection methods to establish electrical connections.
- Encapsulation and Testing: After chip connection, encapsulation is typically performed to wrap the chip in encapsulation material for protection. Testing is also conducted to ensure the functionality of the encapsulated chip.
Overall, the production of semiconductor FC BGA substrates involves multiple steps, including substrate manufacturing, chip fabrication, solder ball connection, encapsulation, and testing, requiring precise manufacturing technology and equipment support.
FAQs
What is a semiconductor FC BGA substrate?
A semiconductor FC BGA substrate is a type of packaging technology used for integrated circuits (ICs). It involves flipping the chip and directly connecting it to the substrate, typically using solder balls or pads.
What are the advantages of semiconductor FC BGA substrates?
Some advantages include shorter signal paths, higher connection density, lower resistance and inductance, better thermal performance, and improved mechanical strength compared to traditional packaging methods.
How are semiconductor FC BGA substrates different from traditional PCBs?
Semiconductor FC BGA substrates are primarily used for IC packaging, directly connecting and encapsulating chips. Traditional PCBs, on the other hand, are used for connecting and supporting various electronic components but do not encapsulate chips.
What are the main components of a semiconductor FC BGA substrate?
The main components include the substrate (base material), chip, metal balls (or solder pads), and encapsulation material for protecting the chip.
What are the production techniques involved in semiconductor FC BGA substrates?
Production techniques include substrate manufacturing (design, cutting, molding), chip fabrication (wafer processing, chip singulation, testing), ball bonding, encapsulation, and testing to ensure functionality.
What applications are semiconductor FC BGA substrates commonly used in?
They are often used in high-performance electronic devices such as microprocessors, graphic processors, high-speed communication devices, and other applications requiring compact, high-density packaging with enhanced thermal and electrical performance.
What considerations should be made when selecting semiconductor FC BGA substrates for a project?
Factors to consider include the electrical requirements, thermal management needs, size constraints, and cost considerations of the project, as well as the specific performance requirements of the integrated circuit being packaged.
What are some potential challenges associated with semiconductor FC BGA substrates?
Challenges may include ensuring proper alignment and connection during assembly, managing thermal dissipation effectively, and addressing any reliability concerns related to the solder joints or encapsulation material.